Check valves are integral components in a variety of industrial and domestic systems, playing a critical role in fluid control. These devices, also known as one-way valves, allow fluid, whether liquid or gas, to flow through them in only one direction. This capability prevents backflow, a common issue that can cause system inefficiencies or failures.
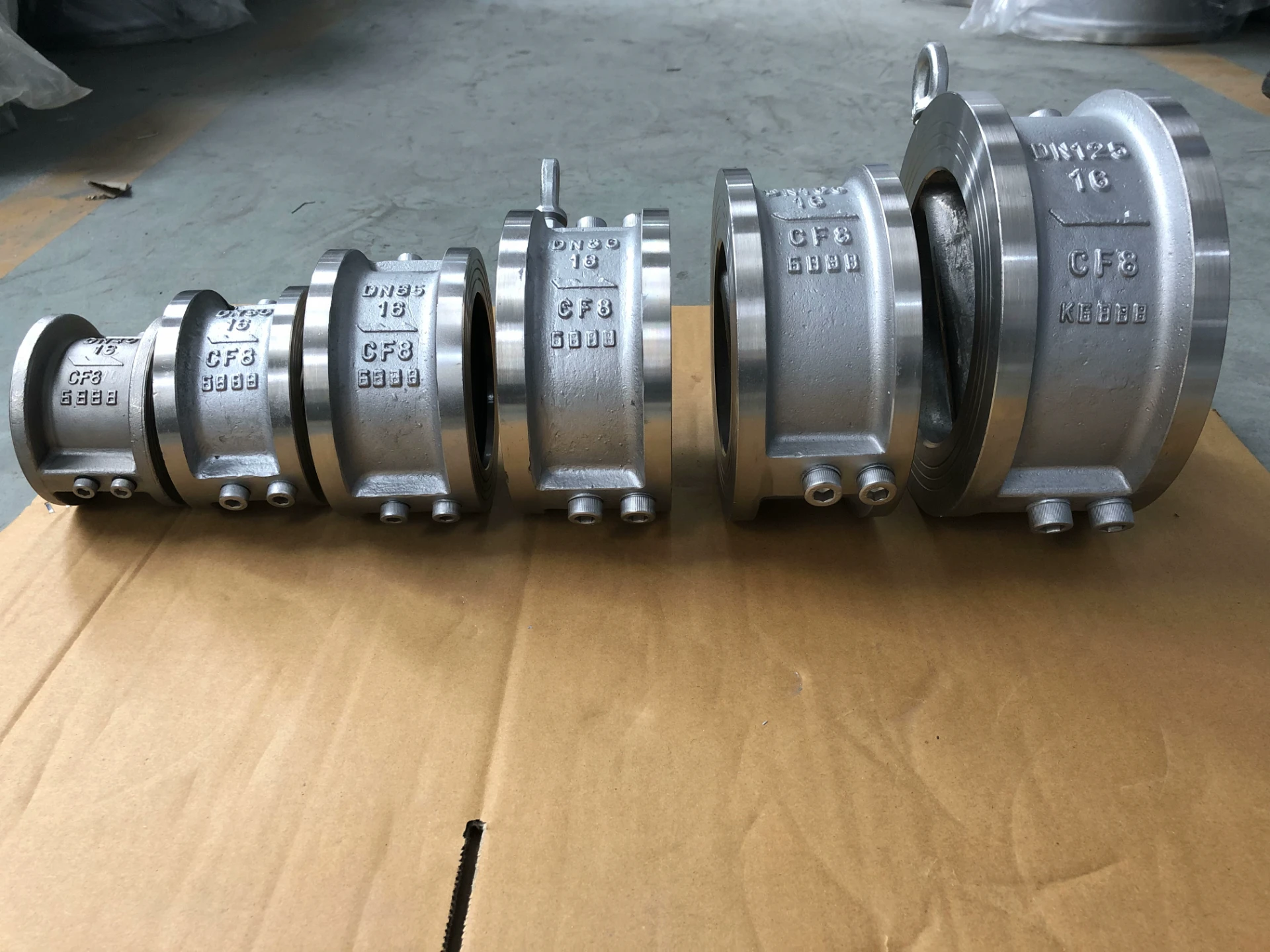
In the realm of expertise and design, check valves come in several types, each suitable for different applications. The most commonly used varieties include swing check valves, lift check valves, and ball check valves, each offering unique advantages based on their construction and the environment in which they are used. Swing check valves, for example, are often preferred for systems with low-pressure drops, as their disc swings away from the seat to allow flow and returns to its place to stop reverse flow. Lift check valves, on the other hand, are more suited to high-pressure systems, where their disc lifts off the seat as pressure increases.
Authoritativeness in the manufacturing of check valves is demonstrated by adherence to international standards and rigorous testing. High-quality check valves are generally composed of durable materials such as stainless steel, brass, and various polymers, which are carefully selected based on the media they will encounter and the expected environmental conditions. Manufacturers who demonstrate commitment to quality often have ISO 9001 certification, ensuring consistent production standards and reliable performance.
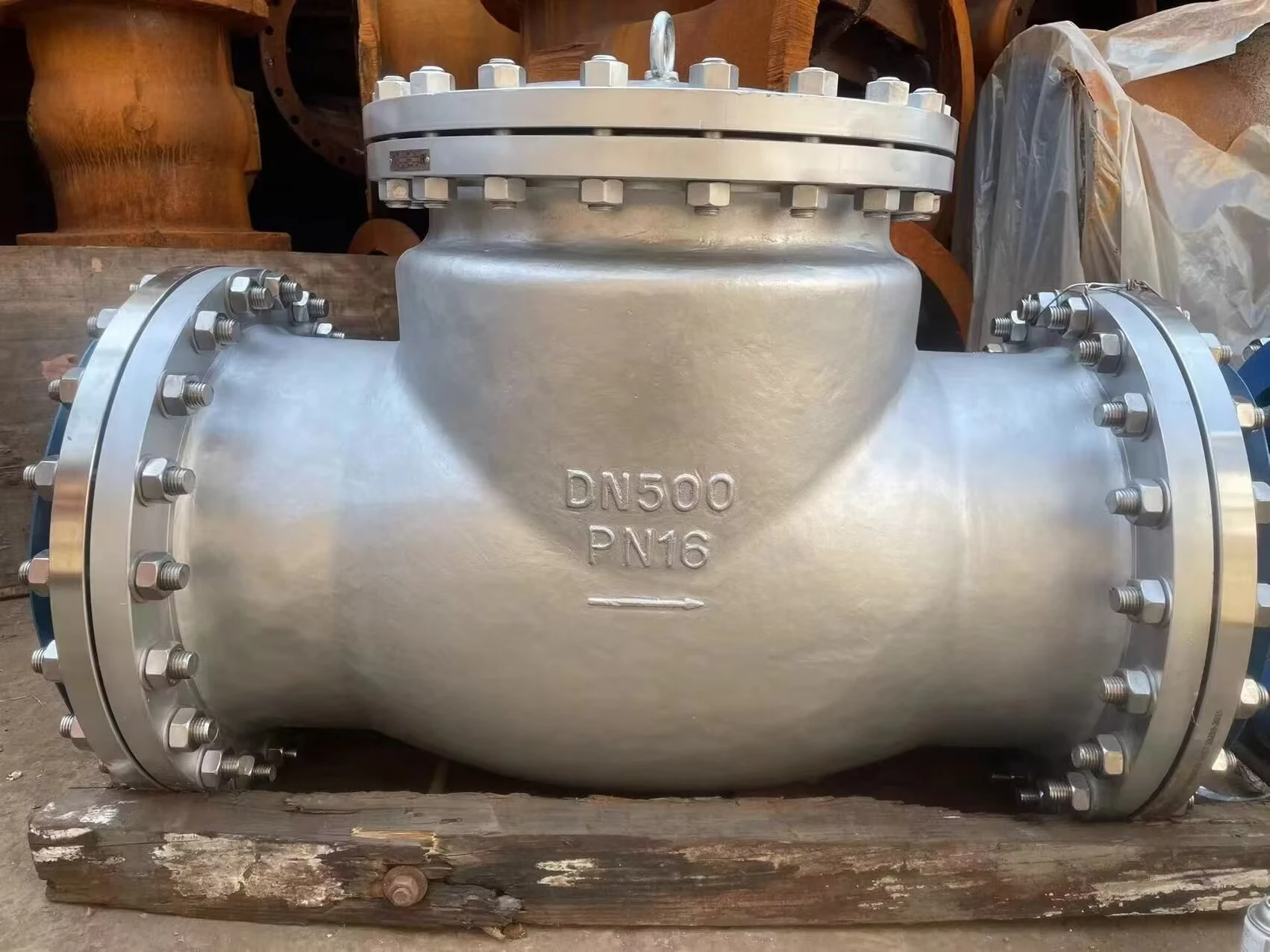
Reliability and trustworthiness in check valves are crucial, given their role in vast systems. A trustworthy check valve is one that has been tested under conditions that mimic real-world scenarios and exhibits durability and longevity. Users should look for valves that feature advanced anti-corrosion properties and wear-resistant features, as these aspects significantly contribute to a longer lifespan.
check valve
When selecting a check valve for a specific application, consider factors such as the type of fluid, temperature, pressure, and potential presence of solids or abrasives. Experience has shown that neglecting to properly match a check valve's specifications to its operational conditions can lead to premature valve failure or inefficient system performance. For example, in slurry systems, using a ball check valve with a soft material ball can minimize damage from particulate matter.
Additionally, installation and maintenance play substantial roles in the performance of check valves. Incorrect installation can lead to problems such as water hammer or excessive pressure drop, both of which can deteriorate system efficacy. Meanwhile, regular maintenance, including inspections for wear and the deposition of materials, helps ensure that valves continue to function optimally.
Insights drawn directly from industry usage highlight the importance of integrating check valves within the broader context of system design. An adept designer will incorporate check valves not merely as components but as critical elements that affect overall system reliability. Consultation with valve experts is recommended for complex systems, where precision in valve selection and usage can mean the difference between seamless operation and costly breakdowns.
In conclusion, check valves, with their diverse applications and crucial role in preventing reverse flow, are fundamental to any fluid control system. Their design, construction, and integration must be approached with a profound understanding of both their mechanical properties and the specific needs of the system they will serve. This combination of knowledge and practical application ensures not only optimal performance but also aligns with the highest benchmarks for safety and efficiency.