Needle valves have become an essential component in high-pressure systems across various industries due to their precision and reliability. These valves are specifically designed to control the flow of liquid or gas with exceptional accuracy, and they are characterized by a slender, pointed needle-like plunger that moves linearly into and out of a limiting orifice. The particular utility of needle valves in high-pressure settings lies in their ability to provide fine flow adjustments, which is critical in processes where precision is paramount.
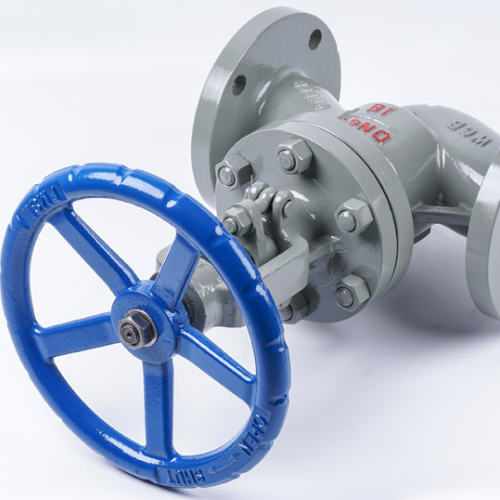
One of the most significant advantages of needle valves in high-pressure applications is their robust construction. Typically made from materials like stainless steel, brass, and other corrosion-resistant alloys, these valves are engineered to withstand extreme pressures and temperatures. For example, in the oil and gas industry, needle valves play a pivotal role in controlling the flow of media at pressures exceeding 10,000 psi. Their durable build ensures longevity and reduces the need for frequent maintenance, which can otherwise be costly and time-consuming.
In the realm of scientific research and laboratory settings, the precision offered by needle valves is unmatched. These valves allow researchers to make tiny adjustments to flow rates with a level of granular control that other valve types cannot provide. This precision is crucial in experiments where even the slightest variation in flow can lead to significantly different outcomes. High-pressure needle valves ensure consistent delivery of gases and liquids, making them indispensable in experimental setups.
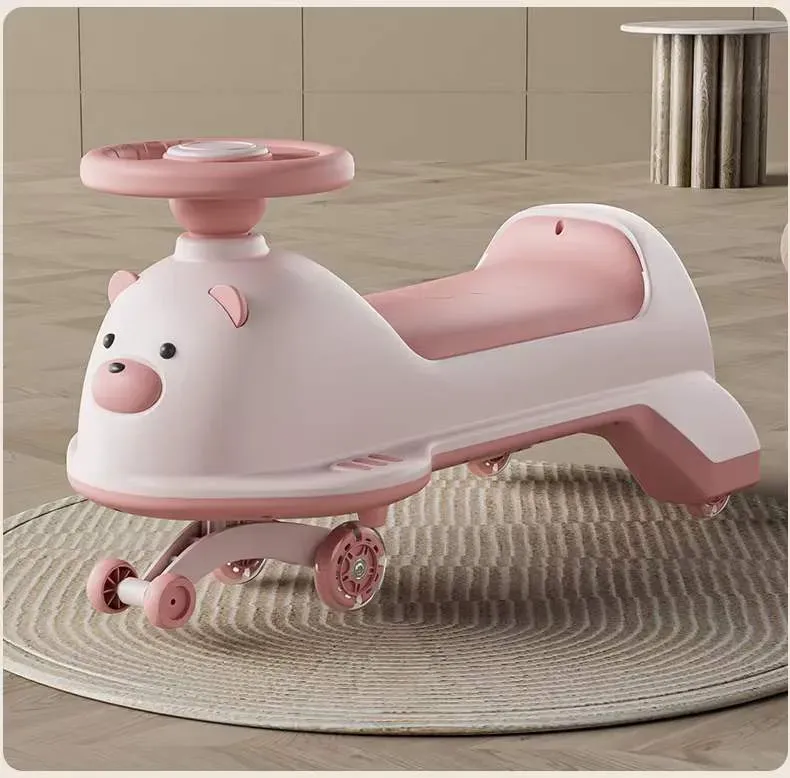
Moreover, the adaptability of needle valves is noteworthy. They are available in various configurations to suit specific system requirements, including straight, angle, and barstock designs. Such flexibility allows engineers to incorporate them into almost any system layout without compromising on performance. Additionally, automated needle valves equipped with pneumatic or electric actuators are becoming increasingly popular. These adaptations facilitate remote operation and integration into larger automated systems, emphasizing the advanced nature of contemporary industrial processes.
Despite their critical applications, selecting the most suitable needle valve for a high-pressure environment requires expertise. The choice hinges on several factors, such as pressure ratings, temperature ranges, and the chemical nature of the fluid being controlled. Collaborating with valve specialists ensures the chosen valve fits seamlessly into the existing system, optimizing performance and safety. Knowledgeable vendors and manufacturers with a track record of reliability in the industry can provide invaluable guidance, enhancing the system's overall efficacy and sustainability.
needle valves high pressure
In addition to reliability and precision, safety is a paramount concern. High-pressure systems impose inherent risks, and needle valves designed with safety in mind help mitigate these hazards. Features such as blow-out proof stems and locking mechanisms are common enhancements that prevent accidents and ensure the safe operation of these systems. Proper installation and regular inspection by certified professionals further bolster the safety and reliability of high-pressure needle valve systems.
Another key consideration in the implementation of needle valves within high-pressure scenarios is compliance with industry standards. Organizations such as the American National Standards Institute (ANSI) and the International Organization for Standardization (ISO) provide guidelines and certifications that ensure valves meet strict quality and safety criteria. Valves that comply with these standards offer an added layer of assurance to stakeholders, reinforcing trust in the system’s integrity and performance.
Environmental considerations also play an increasingly important role in valve selection. As industries strive to minimize their environmental impact, needle valves made from sustainable materials and those designed to reduce emissions are gaining attention. Manufacturers who prioritize environmental responsibility offer products that not only meet functional requirements but also contribute to the broader goals of sustainability.
In conclusion, needle valves designed for high-pressure applications are vital components in numerous industries, valued for their precision, reliability, and safety. The continuous advancement in valve technology and design caters to the evolving demands of modern applications, underscoring the importance of selecting the right valve with professional guidance. By doing so, industries can enhance operational efficiency, uphold safety standards, and contribute to the overarching aim of achieving sustainable industrial practices.