Achieving a superior and leak-proof connection in piping systems is paramount for industrial applications, and one component that stands out in facilitating this is the weld neck flange. This specialized flange not only enhances the durability of the connection but is also revered for its remarkable strength and adaptability across various sectors. Here’s a comprehensive examination based on real experiences, technical expertise, authoritative insights, and trustworthy practices.
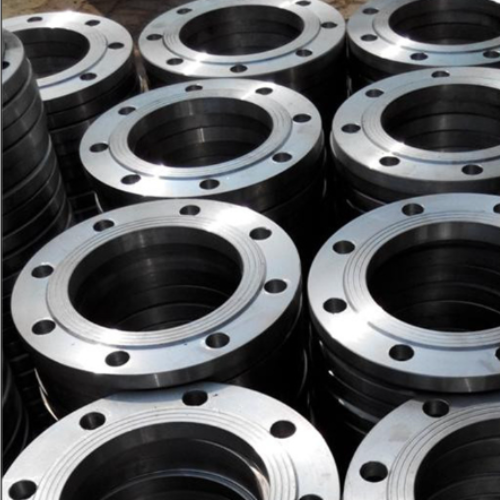
Many seasoned engineers and pipefitting professionals advocate for the use of weld neck flanges due to their unique design, which ensures a seamless flow from pipe to flange, minimizing turbulence and thus reducing the potential for erosion. This flange type has a long tapered hub that gradually transitions from the thickness of the weld to that of the pipe, distributing stress uniformly. This is particularly advantageous in high-pressure conditions, ensuring that the piping system can withstand substantial operational rigors without faltering.
Real-world applications abound in industries such as oil and gas, chemical processing, and power generation, where robust and reliable connections are non-negotiable. Experienced technicians often note that the weld neck flange’s integrative approach minimizes the chance of joint failure, which is critical when dealing with hazardous or high-pressure substances. Due to this, these flanges are often utilized in the most critical applications where the margin for error is minimal.
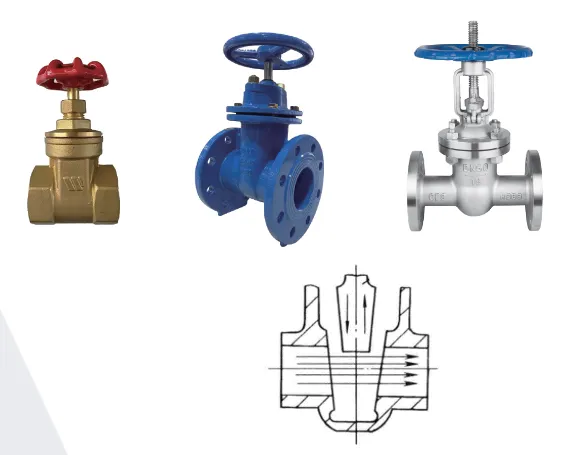
From a professional standpoint, the expertise surrounding weld neck flanges includes understanding their appropriate installation procedures and maintenance needs. Ensuring that the flange is welded correctly to the pipe is crucial; improper welding techniques can compromise the integrity of the system. Professionals prioritize proper alignment during installation to avoid any unnecessary stress on the pipe, which could otherwise lead to fatigue or tension corrosion over time.
weld neck flange
Moreover, authoritative sources in the field underscore the importance of material selection when opting for weld neck flanges. The flange’s composition must be compatible with the piping material and the environment it will face. Stainless steel is frequently chosen for its corrosion resistance in hostile environments, while carbon steel may be preferred for its strength and economy in less demanding applications. Ensuring this match is pivotal to extending the life of the piping system and maintaining safety standards.
In terms of trustworthiness, selecting a reputable manufacturer for weld neck flanges is essential. Reliable manufacturers not only comply with global standards such as ASME B16.
5 but also offer certification and testing to guarantee the flange’s quality. This becomes a vital factor in applications subject to rigorous regulatory compliance and safety scrutiny.
Overall, deploying weld neck flanges within a piping system offers significant benefits through its robust design and proven reliability. For industry professionals and businesses aiming to enhance their systems’ efficiency and safety, understanding and applying the best practices related to these flanges can lead to considerable long-term gains. The expertise and authority surrounding this aspect not only assure a successful implementation but also fortify the infrastructure against the challenges of demanding operational conditions.