When considering materials for industrial applications, cast iron valved components offer exceptional performance and dependability. Having been tested in varied environments and over time, cast iron retains its attractiveness due to several inherent properties, making it a top choice for many industries.
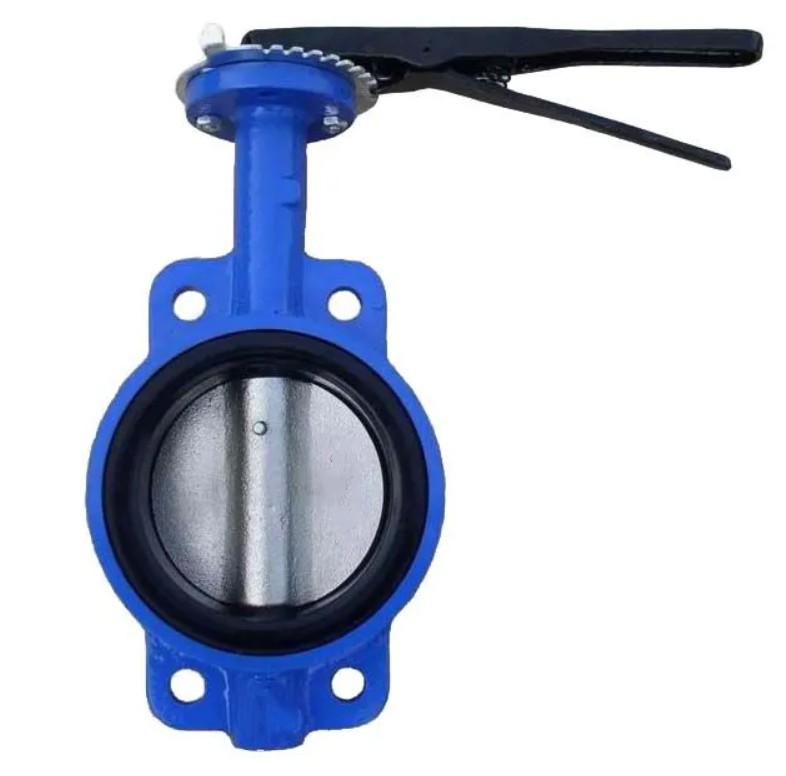
Cast iron remains unrivaled in its balance of cost-effectiveness and durability. In stark contrast to alloys like bronze or stainless steel, cast iron provides a more economical alternative without sacrificing performance. Its strength and ability to withstand substantial pressure make it indispensable in industrial settings, particularly when used in components such as valves that require reliability.
The composition of cast iron inherently imbues it with excellent wear resistance—a highly sought-after trait in valves expected to perform amidst harsh chemicals or extreme temperatures. This robustness is tied to its microstructure, fine-tuned through precise alloying and cooling processes, resulting in a material that resists abrasion and maintains integrity under stress more efficiently than many alternatives.
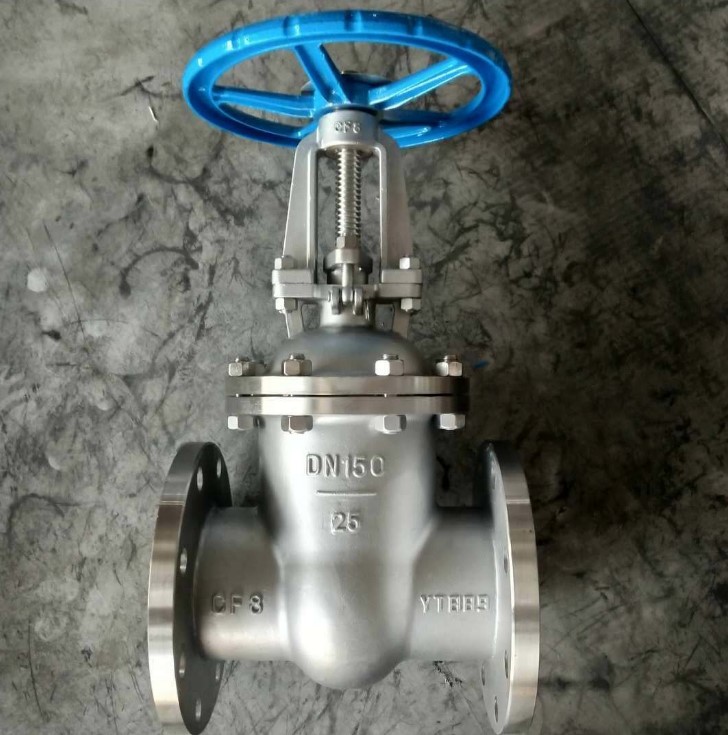
Corrosion resistance is another remarkable feature of cast iron valves, albeit not as pronounced as in stainless steel, but effectively enhanced through contemporary coatings and treatments. These protective measures not only extend the lifespan of the valves but also guarantee steady performance, crucial when valves operate in corrosive environments.
Ease of machining and manufacturing further solidify cast iron's role in valve production. Its workable nature allows for precision in casting complex, intricate designs, essential for producing components requiring tight dimensional tolerances. This precision ensures that valves will perfectly fit into existing systems, reducing installation friction and potential operational issues.
cast iron valved
While cast iron might evoke images of outdated techniques, ongoing innovations have elevated its applications in modern industries. Insularity, a significant consideration, is adequately managed in cast iron valves through design tweaks and alloy enhancements, mitigating risks associated with thermal expansion and contraction.
Real-world experiences echo these advantages, with cast iron valves consistently showcasing resilience in both controlled laboratory environments and actual field conditions. Industries ranging from oil and gas to municipal water treatment facilities report fewer malfunctions and maintenance concerns, attributing greater operational uptime and efficiency to the reliable function of these valved systems.
Experts in fluid dynamics and engineering frequently laud cast iron for its balanced properties, acknowledging that while not the ultimate pinnacle of material science, its pragmatic applications often surpass those of supposedly superior materials in specific scenarios. The acknowledgment from industry practitioners and engineering communities reaffirms cast iron's authority, and its established reputation boosts credibility among users.
Trust in cast iron valves is not merely a product of tradition but is continuously endorsed through practical demonstrations and expert testimony. Rigorous testing protocols in quality assurance processes assess and certify these components, making them worthy investments for stakeholders seeking reliable, performance-driven solutions.
Whether the need is for high-pressure systems, where reliability cannot be compromised or for more budget-conscious projects, cast iron valves stand as a testament to the ingenuity of material science. Their continued relevance is a testimony to finely tuned expertise, making them indispensable components in the intersection of past practicality and future innovation.