In industrial applications where precision and reliability are paramount, the needle gate valve emerges as a superior choice, embodying expertise and authority in fluid control technology. With a design that exudes trustworthiness, the needle gate valve serves as an indispensable component across various sectors, from petrochemical plants to water treatment facilities.
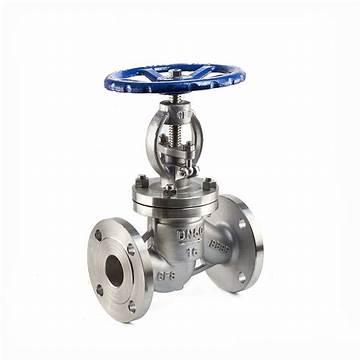
The needle gate valve, characterized by its slender plunger design, offers unparalleled flow control accuracy. This meticulous control is achieved through the valve's long, tapered needle-like point, which meticulously regulates the flow of media with precision unmatched by conventional valve types. This attention to detail in design not only enhances performance but also prolongs the durability of the valve, contributing to less frequent maintenance and reduced operational costs.
Engineered with the principle of fine-tuning in mind, the needle gate valve is especially favored in applications requiring minimal flow rates. Its precise handling makes it ideal for scenarios that demand exact measurement of liquid flow, such as in laboratory settings and chemical dosing systems. This specificity in its use underscores its professionalism in meeting industry demands where even the slightest deviation in flow can lead to significant operational setbacks.
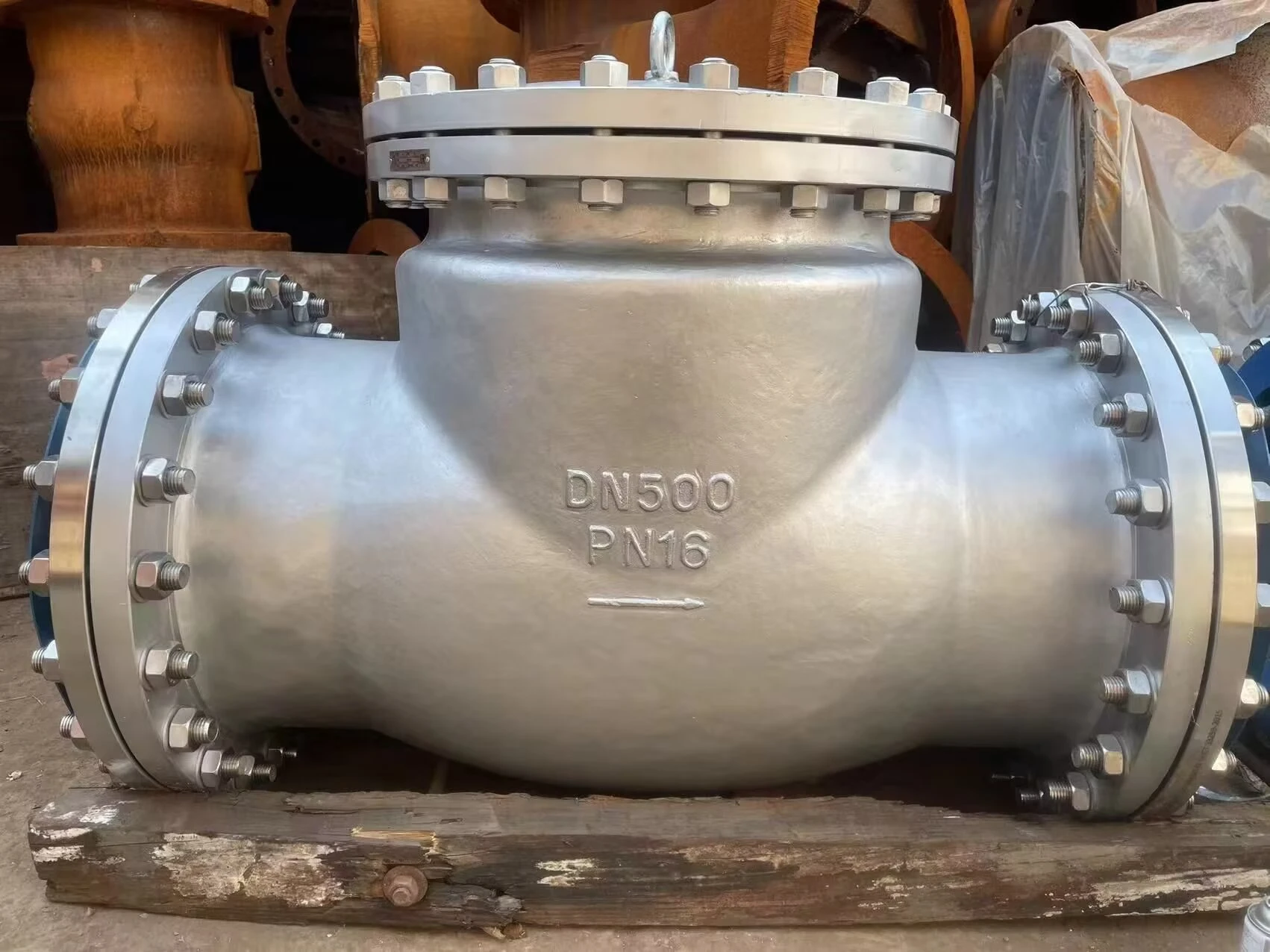
Manufacturers of needle gate valves adhere to stringent quality controls, ensuring that each valve meets rigorous industry standards. This commitment to excellence reinforces the valve's authority in sectors prone to challenging environments, such as oil and gas industries where high pressures and temperatures are constants. The robust materials employed in manufacturing these valves, such as stainless steel and high-grade alloys, further emphasize their reliability and long-standing performance, even under the most demanding conditions.
In terms of operational efficiency, the needle gate valve showcases expert craftsmanship. Its design allows for minimal frictional loss, ensuring that energy consumption is kept to a minimum. This energy efficiency not only contributes to a sustainable operation but also reduces costs over time, presenting a compelling case for industries focused on maximizing their operational budgets without compromising on quality or performance.
needle gate valve
Incorporating needle gate valves into fluid control systems is a decision steeped in trust and authority. End-users consistently report high satisfaction and reliability rates, citing the valve’s ability to deliver consistent performance over extended periods. Testimonials from industry experts highlight the valve’s adaptability and resilience, pointing to case studies where these valves have significantly improved system efficiency and reliability.
Trustworthiness is further amplified by the comprehensive testing each valve undergoes before reaching the market. Rigorous assessments validate the valve’s capability to withstand extreme operational conditions, fortifying its reputation as a dependable solution. This meticulous vetting process reassures stakeholders of the needle gate valve’s quality and performance, enhancing trust in its application.
The growing reliance on needle gate valves underscores an industry-wide recognition of their unparalleled expertise and dependability. As industries increasingly prioritize precision, sustainability, and cost-effectiveness, needle gate valves stand out as a beacon of authoritative engineering. Their continued evolution, driven by technological advancements and material innovations, positions them as a cornerstone of modern fluid control solutions.
In conclusion, the needle gate valve's dominance in precision fluid management is a testament to its design excellence and reliability. Through a blend of engineering expertise, rigorous testing, and superior material selection, these valves offer a compelling solution for industries demanding the highest standards of operational precision and trustworthiness. As new technological frontiers emerge, the needle gate valve remains poised to adapt, thereby cementing its role as an essential component in the landscape of industrial flow control.