Pipe welding fittings are the unsung heroes in the vast world of piping systems, quietly performing their roles with precision and reliability. From sprawling industrial complexes to smaller residential setups, these components ensure seamless connectivity, safety, and efficiency. Understanding the intricacies of pipe welding fittings is fundamental for anyone diving into the plumbing or construction industry, as it directly impacts the longevity and functionality of any pipeline project.
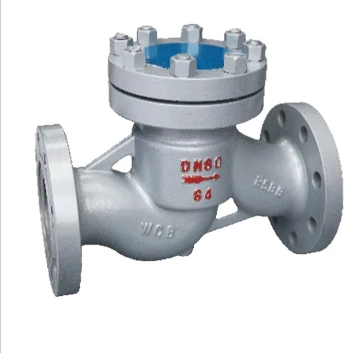
These fittings come in various forms, each designed for a specific purpose and function. Common types include elbows, tees, reducers, and caps. Their primary role is to guide the flow of liquids or gases, change the direction of the flow, connect different sizes of pipe, or stop the flow altogether.
Each type serves a unique function, making it vital to select the right fitting for the job.
In terms of experience, one should appreciate the nuances of the installation process. Welding pipe fittings requires a combination of skill and understanding of metallurgical properties. Different materials such as stainless steel, carbon steel, or copper-nickel have distinct properties and behave differently under the welding arc or torch. A seasoned welder recognizes that the welding technique, whether it's MIG, TIG, or Stick, must be chosen based on the fitting material to mitigate issues such as corrosion or thermal fatigue.
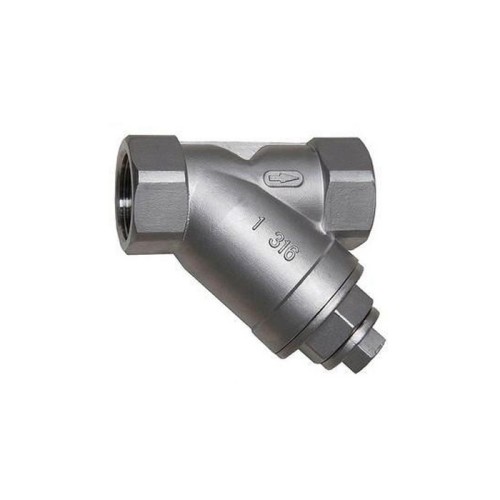
Expertise in this field doesn't just encompass knowledge of materials and techniques, but also an understanding of industry standards and codes. Organizations like the American Society of Mechanical Engineers (ASME) provide guidelines that ensure the safety and compatibility of welding fittings. Following these codes guarantees that the welded joints will withstand pressure changes and temperature fluctuations, safeguarding against catastrophic failures.
pipe welding fitting
Trustworthiness in pipe welding fittings stems from rigorous testing and quality control. Each fitting should undergo comprehensive evaluations, such as pressure testing, radiographic inspections, and ultrasonic examinations. This rigorous testing ensures that every fitting meets the high standards necessary for their demanding roles.
Furthermore, choosing a reputable supplier or manufacturer can significantly impact the quality of fittings. Renowned manufacturers invest in research and development to innovate and improve the durability and efficiency of their products. They also provide certificates of compliance, traceability documentation, and warranty information, further enhancing buyer confidence.
Finally, achieving authoritativeness in the realm of pipe welding fittings comes from consistent, successful application and an unblemished track record. Companies that exemplify authority often share case studies, testimonials, and data-backed results. They engage in continuous learning and adaptation to new technologies and methodologies, ensuring that they remain at the forefront of the industry.
In conclusion, pipe welding fittings may seem like a mundane part of the infrastructure, but they play a critical role that demands attention to detail, a sound understanding of materials and techniques, adherence to industry standards, and a commitment to quality assurance. By focusing on these core areas—experience, expertise, authoritativeness, and trustworthiness—professionals in this field can ensure the success and reliability of their piping systems. As technology evolves and new challenges arise, those who master these fundamentals will lead the way in delivering safe and efficient plumbing solutions.