In the complex world of fluid dynamics, the role of a check valve cannot be overstated. Check valves, sometimes referred to as one-way valves, are pivotal devices in various industries, notably plumbing, oil and gas, and manufacturing. A check valve is engineered to permit the flow of fluids in a singular direction while preventing any backward flow, safeguarding against potential system failures.
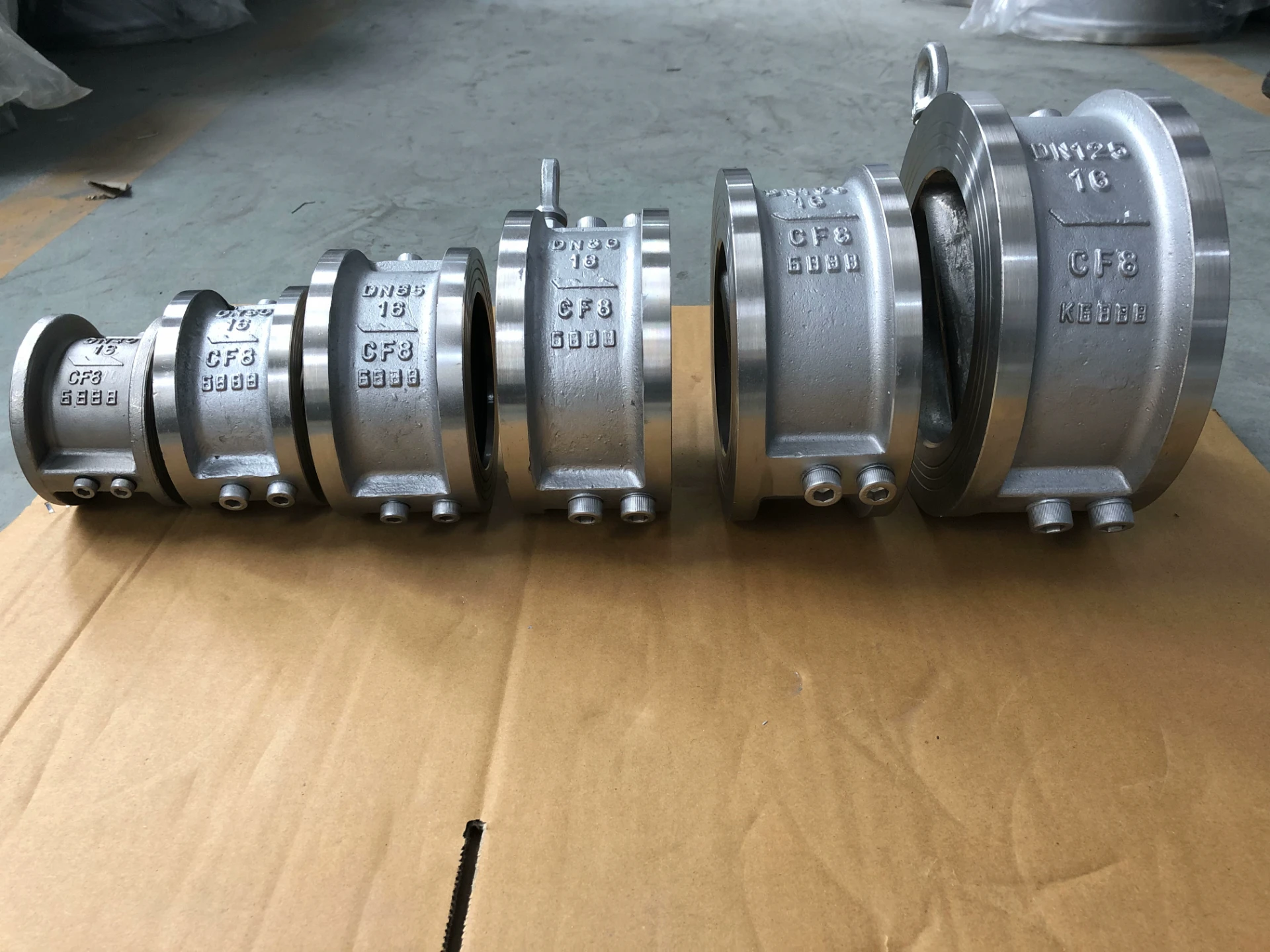
The core principle behind a check valve is its ability to leverage the fluid pressure itself to open and close the valve mechanism. When fluid flows in the intended direction, it exerts pressure on a disc, ball, or swing configuration, depending on the design, which opens the valve. Conversely, pressure from any backflow will force the valve to close, thus preventing reverse movement of the fluid.
Industries have a variety of options when it comes to the type of check valve best suited to their specific applications. Swing check valves, which utilize a disc that swings on a hinge, are prevalent in systems where low-pressure conditions are present. They are highly effective in water and wastewater treatments due to their simplicity and reliability. On the other hand, ball check valves, featuring a spherical ball that rotates against a seat to stop reverse flow, are beneficial in smaller diameter piping or applications requiring minimal space.
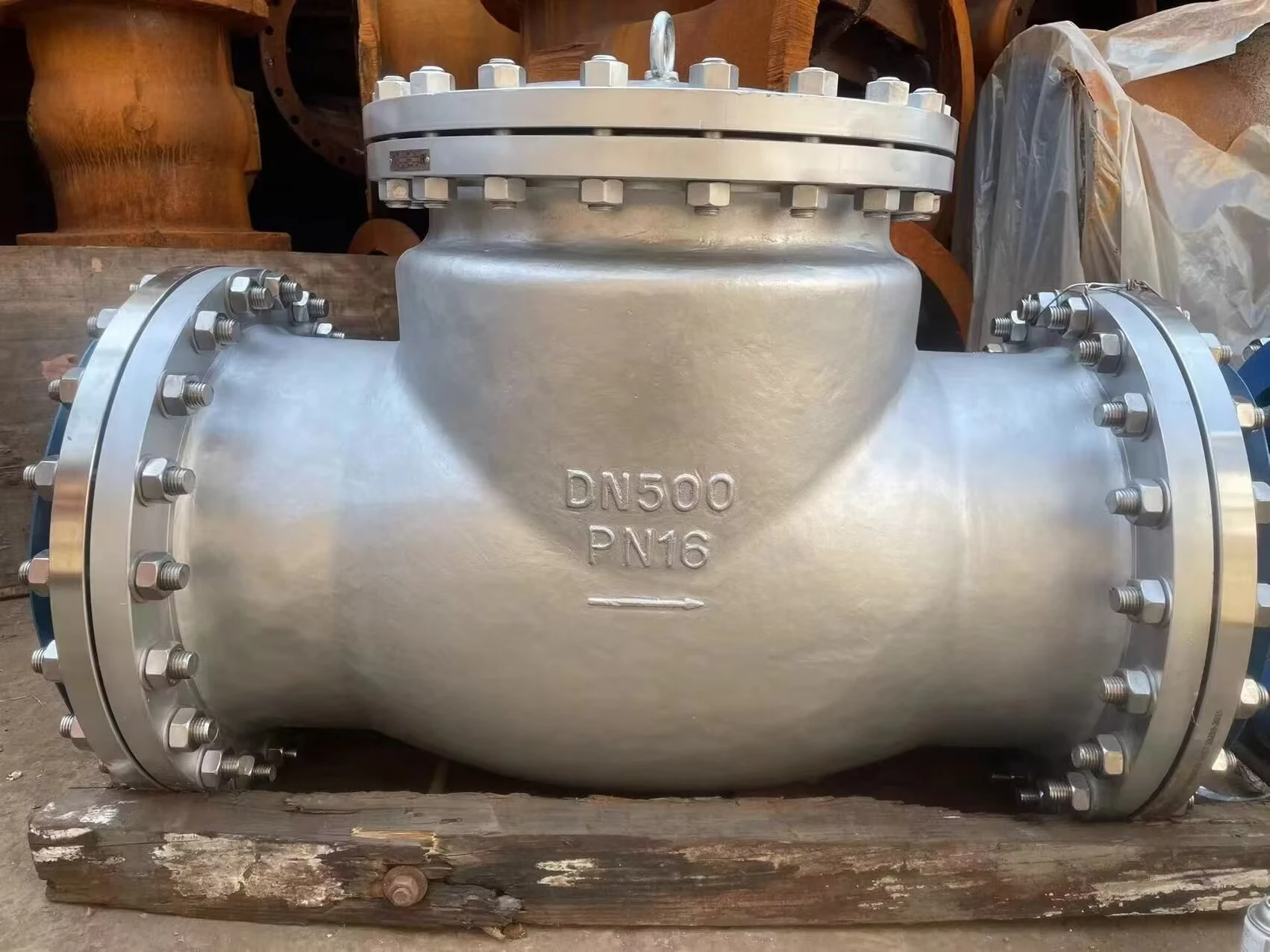
Additionally, the choice of materials in check valves significantly impacts their performance and longevity. Stainless steel check valves, for instance, offer excellent resistance to corrosion and are ideal for industries dealing with harsh chemicals. Meanwhile, PVC check valves find their strengths in applications involving water systems due to their lightweight and cost-effective nature.
check valve
Expertise in selecting the appropriate check valve involves considering factors such as the fluid type, operating temperature, pressure conditions, and required flow performance. Professional consultation with manufacturers ensures the selection of the optimum valve tailored to specific industrial needs, thereby enhancing system efficiency and reducing operational downtimes.
An often overlooked yet critical aspect of maintaining check valve systems is regular inspection and maintenance. Over time, wear and tear, debris accumulation, or improper installation can impair the valve's functioning. Scheduled maintenance, which includes cleaning and replacing worn components, is crucial for the valve's long-term operation. Employing innovative technologies like predictive maintenance can preemptively identify issues, thereby eliminating sudden failures and extending the lifespan of the system.
The environmental aspect of check valves cannot be ignored. Modern advancements have led to the development of check valves with improved sealing technologies that minimize leaks, thus conserving fluids and reducing environmental impact. This design consideration aligns with global initiatives towards sustainable and eco-friendly industrial processes.
In conclusion, check valves serve as guardians of seamless fluid dynamics across various industrial applications. Their ability to enhance safety, improve operational efficiency, and adapt to diverse operational demands underscores their indispensable role in modern infrastructure. By opting for high-quality materials, engaging in regular maintenance practices, and embracing innovative technologies, industries can maximize the potential of check valves, ensuring reliable and sustainable operations.