Non-return valves, also known as check valves, are integral components in plumbing and industrial systems, preventing the backward flow of fluids. Understanding their mechanics and choosing the right one is crucial for efficiency and safety. Leveraging years of expertise in fluid dynamics, this article delves deeply into the nuances of non-return valves, offering insights that remain unparalleled on the web.
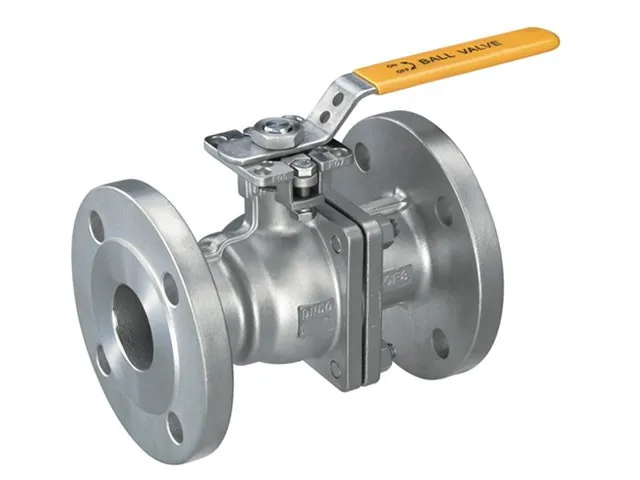
Non-return valves operate on a simple yet effective principle. Imagine a door that opens only one way this is similar to how non-return valves function, allowing fluids to flow in one direction, while automatically preventing reverse flow. This feature protects critical components such as pumps and compressors from potential damage caused by backflow.
There are various types of non-return valves, each suited for specific applications. The most common include swing check valves, lift check valves, and ball check valves. Swing check valves are ideal for low-flow applications; they have a disk that swings on a hinge or trunnion, which permits or blocks fluid flow. Lift check valves work best in high-pressure systems; they use a guided disk that rises and falls within a chamber. Ball check valves, often found in systems with a high volume of particulate matter, utilize a ball that moves in response to fluid pressure, sealing off the backflow route.
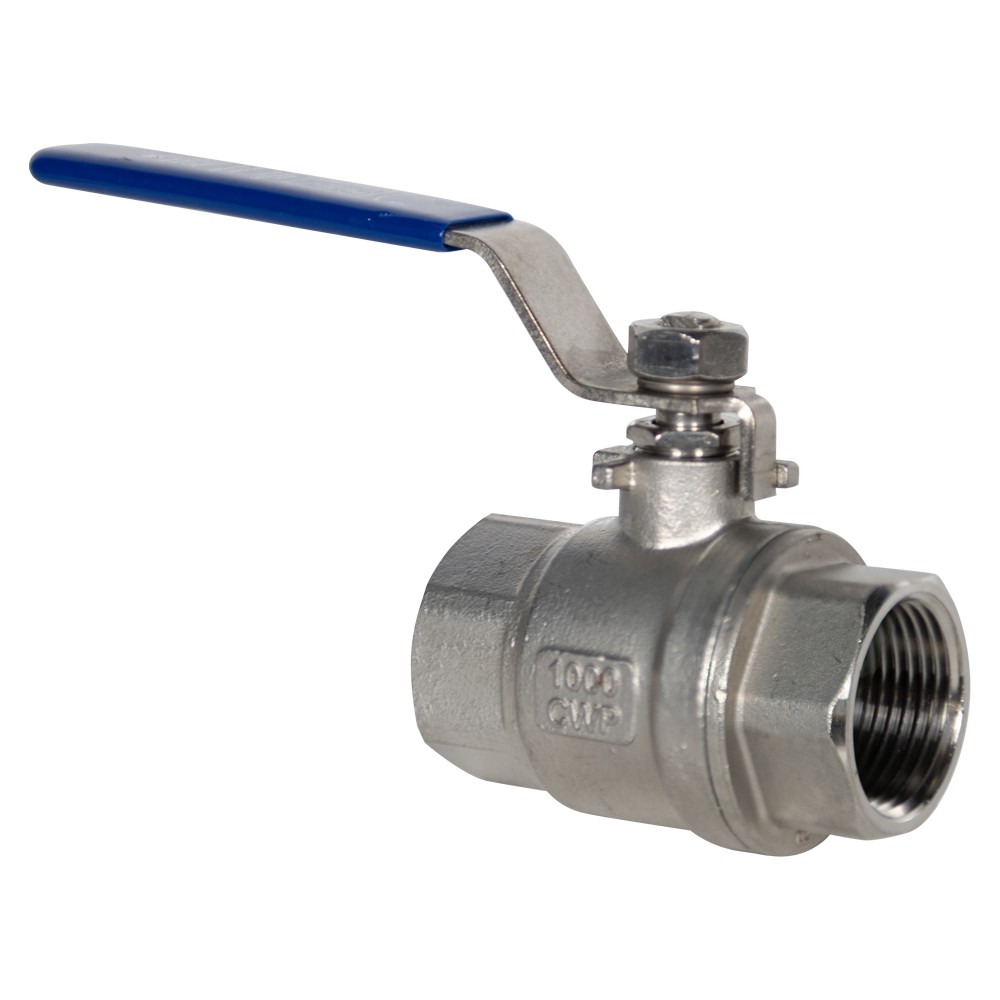
Quality non-return valves are constructed from robust materials like stainless steel, brass, or PVC, ensuring durability and longevity. Selecting the appropriate material based on the fluid’s properties—whether it’s corrosive, hot, or under high pressure—is an essential step. For example, stainless steel is excellent for corrosive environments, while PVC is a cost-effective choice for low-pressure systems involving non-corrosive fluids.
non return valve
Installation and maintenance are pivotal to a valve's performance and lifespan. Installation should be done by experienced professionals who ensure the valve is placed in the correct orientation and is free of debris. Regular maintenance can preclude problems before they arise. This includes periodic inspection for wear or corrosion and testing for functionality. In some systems, incorporating a maintenance schedule that includes pressure testing and internal inspections can avert costly system failures.
A growing trend in non-return valve technology is the integration of smart sensors. These sensors monitor valve performance in real time, alerting operators to potential issues before they become critical. Such technology not only enhances system reliability but also contributes to overall operational efficiency by reducing downtime and maintenance costs.
In conclusion, the importance of non-return valves cannot be overstated when it comes to safeguarding fluid systems. Through meticulous material selection, expert installation, and proactive maintenance, these valves provide an irreplaceable service in both industrial and commercial applications. As technology evolves, the advancements in non-return valve designs and materials will continue to improve their performance and reliability, making them even more indispensable in the management of fluid dynamics.