Understanding the Role of Plate Flange Manufacturers in Industrial Applications
Plate flanges, an integral part of piping systems, play a crucial role in connecting pipes, valves, pumps, and other equipment in various industries. These circular discs with holes in the center are primarily used to provide a strong and secure joint, ensuring the safe transportation of fluids or gases. The significance of plate flanges cannot be overstated, and behind their manufacture stands a dedicated industry that specializes in their production.
A plate flange manufacturer is a specialized entity that designs, engineers, and fabricates these vital components. They employ advanced technologies and high-quality materials to ensure that the flanges meet stringent industry standards such as ASME, ANSI, API, and EN. The manufacturing process typically involves cutting, forming, and machining raw metal plates into the desired shape and size, followed by rigorous quality control checks.
The choice of material is critical in plate flange manufacturing. Common materials include carbon steel, stainless steel, alloy steel, and aluminum, each chosen based on factors like corrosion resistance, temperature tolerance, and pressure ratings. For instance, stainless steel flanges are often used in corrosive environments, while carbon steel flanges are more cost-effective for general-purpose applications.
Manufacturers also offer different types of flanges, such as welding neck, blind, slip-on, lap joint, and threaded, each designed for specific applications and conditions. Welding neck flanges, for example, are preferred in high-pressure situations due to their gradual transition from pipe to flange, reducing stress concentrations Welding neck flanges, for example, are preferred in high-pressure situations due to their gradual transition from pipe to flange, reducing stress concentrations
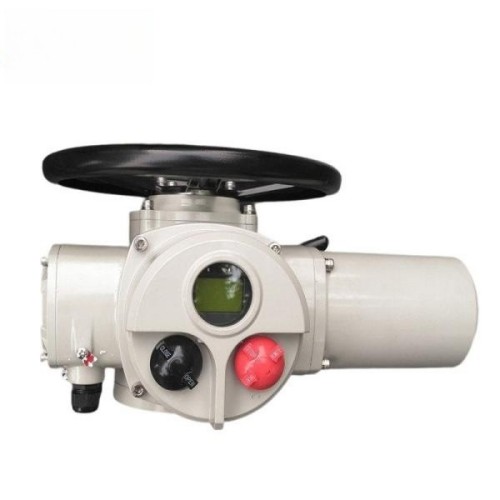
Welding neck flanges, for example, are preferred in high-pressure situations due to their gradual transition from pipe to flange, reducing stress concentrations Welding neck flanges, for example, are preferred in high-pressure situations due to their gradual transition from pipe to flange, reducing stress concentrations
plate flange manufacturer.
In addition to standard sizes, custom plate flange manufacturers cater to unique requirements, providing tailored solutions for non-standard diameters, thicknesses, and pressure ratings. This flexibility is essential in industries where pipes and equipment may have unconventional dimensions or require specialized connections.
The role of a plate flange manufacturer extends beyond production. They often provide technical support, assisting customers in selecting the right flange type and size for their specific application. They also ensure compliance with safety regulations and industry standards, minimizing potential risks in the operational phase.
In conclusion, plate flange manufacturers are the backbone of industries that rely on efficient piping systems. Their commitment to precision engineering, use of superior materials, and adherence to global standards ensure the reliability and longevity of these connectors. Whether it's oil and gas, chemical processing, power generation, or water treatment, the contribution of these manufacturers is indispensable in maintaining the integrity of industrial infrastructure. As technology advances and industry demands evolve, so too will the innovation and expertise of plate flange manufacturers, continuously shaping the future of pipeline connections.