Welding neck flanges have become a cornerstone in industrial piping and have maintained a distinguished reputation for their reliability and effectiveness in complex systems. Their unique design, characterized by a long tapered hub and a smooth transition between its thickness and the pipe, effectively distributes stress over a broader area. This design element is the key to its strength and is a pivotal feature that sets it apart in industries ranging from oil and gas to power generation.
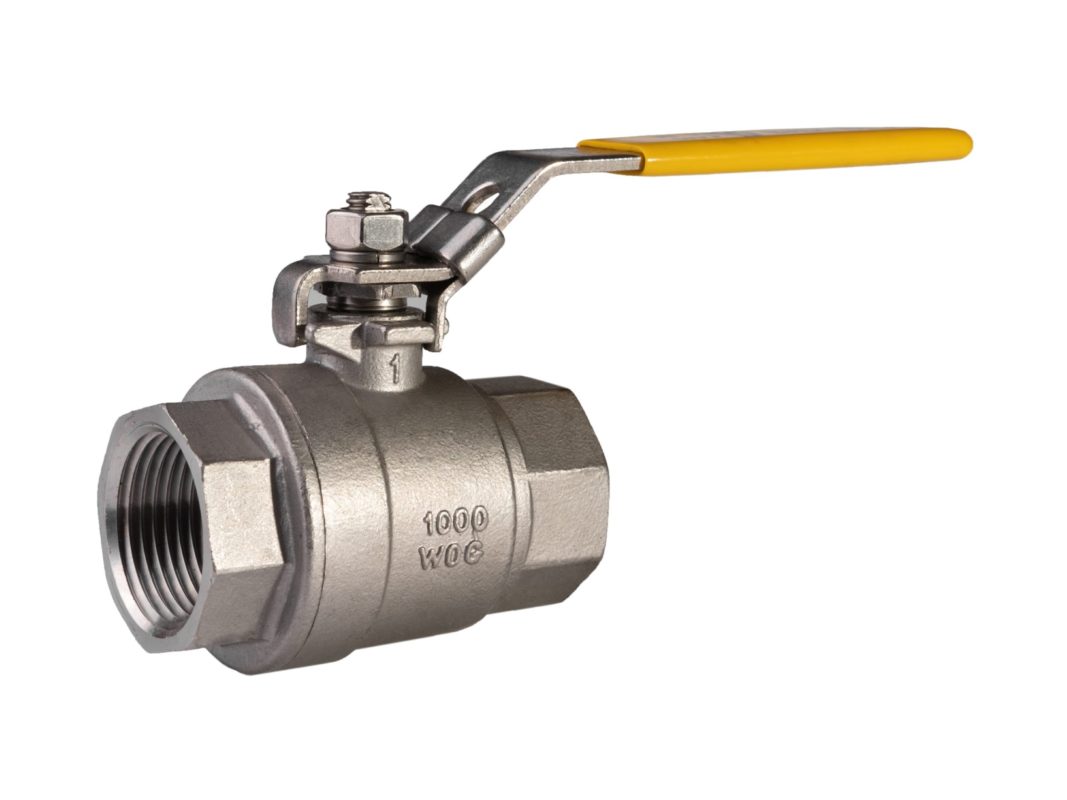
When considering the implementation of welding neck flanges, understanding the synergy between their design and function is paramount. Their longevity and ability to withstand extreme conditions make them indispensable for systems where safety and reliability cannot be compromised. The ability to facilitate a seamless flow within critical applications is not merely desirable but essential, ensuring no disruptions or weak points are present in the system.
Experience with welding neck flanges reveals their superiority in high-pressure environments. One of the most significant advantages of these flanges is their ability to accommodate pressure fluctuations and temperature variations without faltering. This adaptability is crucial not only in maintaining operational integrity but also in safeguarding against potential hazards that could arise due to component failure.
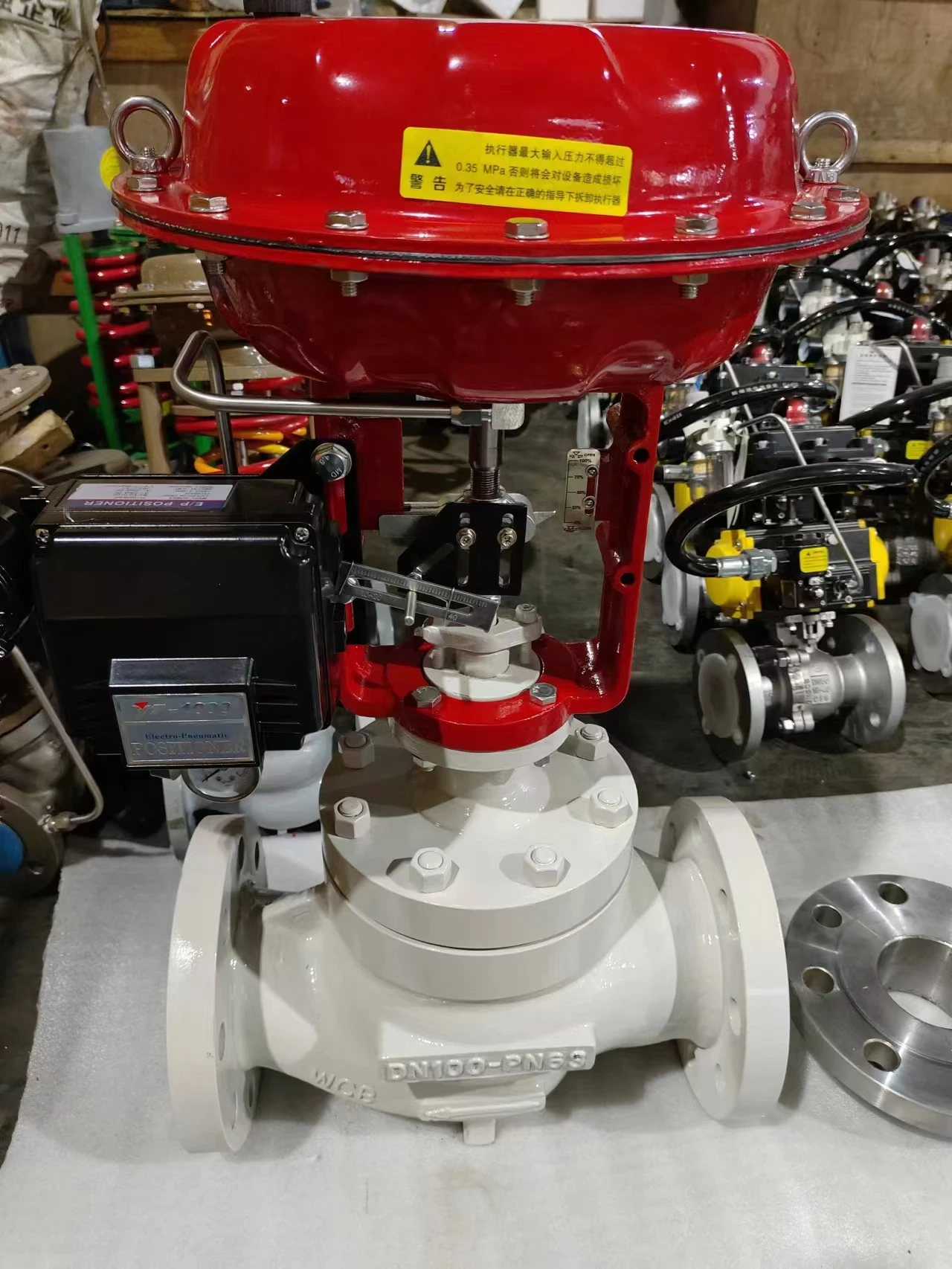
Moreover, welding neck flanges are revered for their ease of integration into existing systems. Their compatibility with various pipe sizes and materials makes them versatile, eliminating the need for specialized connectors or extensive modifications. This versatility reduces operational downtime significantly and makes them a cost-effective solution in the long term.
Professionally, the choice of material for welding neck flanges can vary depending on the specific application, with options ranging from stainless steel to more exotic alloys. Expertise in material science and a thorough understanding of the environment in which these flanges will operate are critical for selecting the appropriate material. This knowledge ensures that longevity and performance are optimized, particularly in corrosive or extreme temperature settings where improper materials could result in premature failure.
welding neck flange
In terms of authority, welding neck flanges meet and exceed various international standards such as ASME, ANSI, and DIN. These certifications are a testament to their quality and performance, providing an assurance of reliability and efficiency in global applications. The adherence to these rigorous standards positions welding neck flanges as the preferred choice for engineers and designers seeking assurance in their infrastructure components.
To build trustworthiness, industry professionals often rely on suppliers with a proven track record. The procurement of welding neck flanges from reputable manufacturers ensures that all components meet the specified standards and performance expectations. Thorough documentation and traceability are vital in maintaining trust, as they provide tangible evidence of the flange's capabilities and compliance.
In practice, the proper installation of welding neck flanges is just as critical as their selection. This involves precise alignment during welding to prevent any undue stress that could compromise their integrity.
Skilled technicians with experience in welding and alignment play a crucial role in ensuring that the flange performs as intended.
Ongoing maintenance and inspection further strengthen the trustworthiness of welding neck flanges. Regular assessments for wear, corrosion, and alignment help in preemptive detection of potential issues, allowing for timely interventions and the avoidance of costly downtime. Implementing a robust maintenance schedule based on the specific conditions at the site is an integral part of lifecycle management, enhancing the overall reliability and performance of these components.
In conclusion, the use of welding neck flanges is a testament to their unparalleled strength, versatility, and reliability in challenging applications. With a deep understanding and expertise in their application, they present a highly authoritative and trustworthy solution in industrial piping systems. Whether dealing with high pressures, extreme temperatures, or corrosive environments, welding neck flanges are the go-to solution for ensuring operational excellence and safety.