Flat faced flanges are a pivotal component in various industrial applications, providing a seamless connection between pipes, valves, pumps, and other essential equipment. These flanges are characterized by their flat surface, which allows for a complete, direct contact with the connecting component, ensuring a tighter seal and enhanced stability. For industries that depend on the flawless operation of piping systems, such as oil and gas, chemical processing, and power generation, flat faced flanges offer an optimal solution.

To delve into the extensive benefits of flat faced flanges, it's crucial to consider their design, materials, and application contexts. Their flat face design is deliberately crafted to interact with either a full-face gasket or flat face-to-flat face connections. This construction minimizes misalignment and uneven stress distribution, thereby reducing the likelihood of leaks or structural failures. The simplistic, yet effective nature of flat faced flanges is a testament to their reliability, making them a preferred choice in environments where safety and durability are paramount.
Material selection is a cornerstone in the manufacturing of flat faced flanges. Commonly, these flanges are made from robust materials such as stainless steel, carbon steel, and ductile iron. Each of these materials offers unique properties that cater to specific industrial needs. Stainless steel flat faced flanges, for instance, provide exceptional resistance to corrosion and extreme temperatures, making them ideal for chemical and petrochemical industries. On the other hand, carbon steel flanges deliver high strength and toughness, better suited for high pressure and high-stress environments.
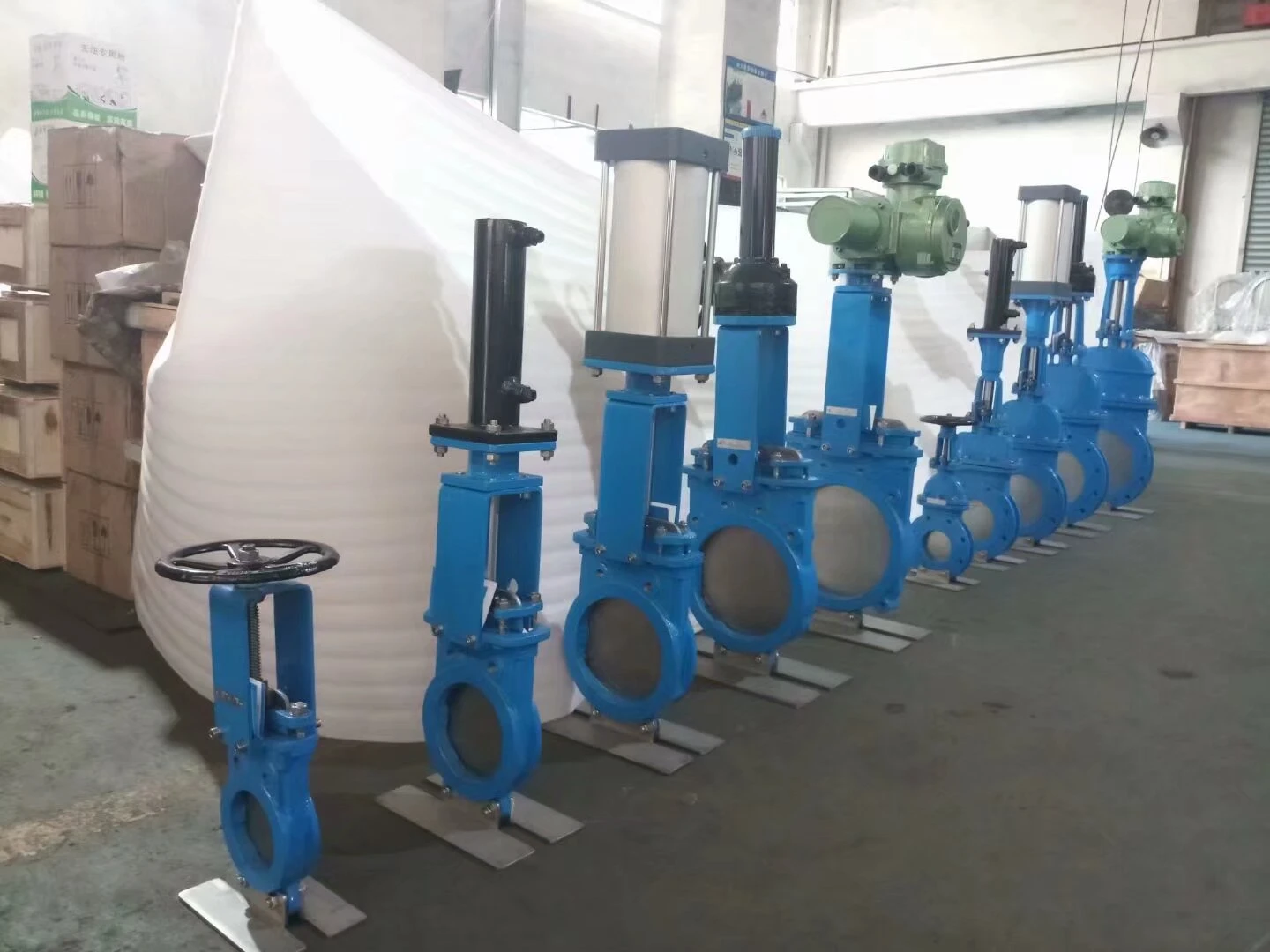
In addition to their mechanical advantages, flat faced flanges support easy maintenance and installation. Their design facilitates straightforward connection with piping systems, requiring minimal tools and expertise. This ease of installation reduces downtime during maintenance, allowing industries to maintain optimal operational efficiency. Technicians appreciate the simplicity of flat faced flanges, which contributes to faster assembly and disassembly processes, enhancing productivity and reliability in maintenance procedures.
flat faced flanges
Safety remains a top priority in industries deploying complex piping systems, and flat faced flanges contribute significantly to maintaining this safety.
Their flat surface, which demands the use of a full-face gasket, ensures maximum sealing across the flange face. This stringent sealing capability prevents hazardous substance leaks, protecting both the workforce and the environment. Furthermore, by minimizing misalignment, flat faced flanges reduce the potential for vibration and noise within piping systems, diminishing the risk of mechanical failure over time.
In terms of standards and compliance, flat faced flanges conform to numerous international standards, including those established by ANSI, ASME, and DIN. These standards assure that the flanges meet rigorous safety, quality, and efficiency criteria, allowing them to be used confidently in a multitude of global applications. Companies can thus ensure compatibility and interoperability when employing flat faced flanges across diverse projects and regions.
Investing in quality flat faced flanges is integral to the successful operation of piping systems. Choosing the right flange involves considerations of material compatibility with the medium being transported, the environmental conditions of operation, and the pressure and temperature ratings necessary for the specific application. Engaging with a reputable supplier who offers comprehensive product support and guidance is essential in acquiring the appropriate flanges that meet the demands of your project.
As industries continue to evolve and address new challenges, the role of reliable components like flat faced flanges becomes increasingly vital. Their contribution to operational success, safety, and efficiency underscores their importance in the industrial spectrum. By leveraging the inherent advantages of flat faced flanges, businesses can secure a competitive edge through enhanced infrastructure resilience and reduced operational risks.