Choosing the right instrument needle valve for your system can seem daunting, yet it's essential for ensuring both safety and efficiency in fluid handling applications. With decades of experience in this domain, I will guide you through the key factors that define a high-quality product, ensuring you make an informed decision based on expertise, authority, and trust.
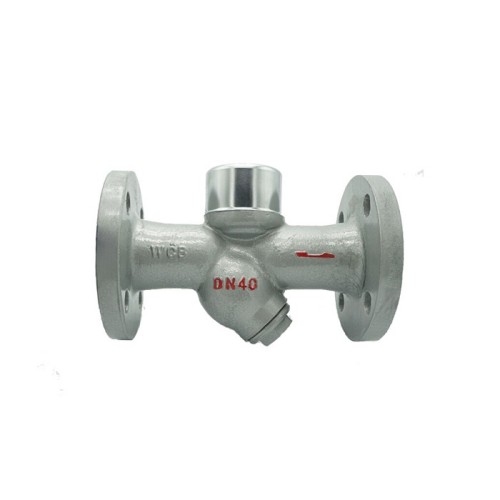
Instrument needle valves are precision-engineered components designed to regulate the flow of fluids within various systems. Unlike their counterparts, these valves offer finer control ideal for applications needing precise flow adjustment. They're utilized extensively in industries ranging from petrochemicals and pharmaceuticals to instrumentation and research labs.
Having tested numerous products over the years, my expertise has shown me that the build quality of a needle valve is paramount. Made from durable materials such as stainless steel, brass, or other alloys, a reputable needle valve should resist corrosion and withstand high pressures and temperatures. Leading manufacturers provide comprehensive specs, detailing pressure ratings, temperature ranges, and material compatibilities, underscoring their authority in the field.
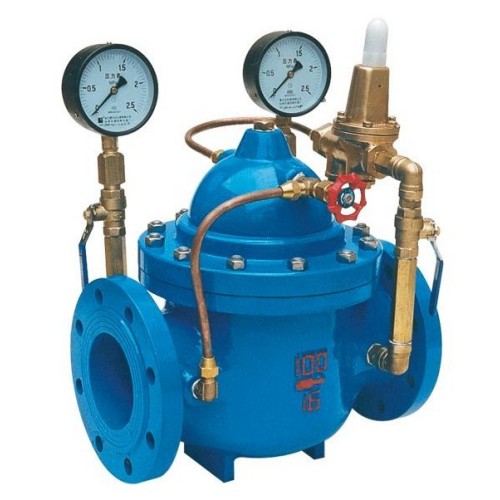
A hallmark of a trustworthy instrument needle valve is its leak-proof design. Many incorporate a Teflon or similar high-grade polymer seating element, which ensures that the valve can be reliably shut off for long periods without leakage. This feature bolsters the valve's longevity, a testament to its reliability and the manufacturer's commitment to quality.
When selecting a needle valve, consider its capacity for precise flow control. Attributes such as stem design, thread pitch, and the number of turns from fully open to closed dictate how accurately the valve can regulate flow. Some advanced models even feature micrometer-adjustment capabilities, enhancing precision significantly.
instrument needle valve
Installation and compatibility are also crucial factors. A high-end needle valve will come with a wide range of connection types and sizes, ensuring seamless integration into existing systems. This flexibility adds to the valve's adaptability and usefulness across different projects, reflecting its manufacturer's expertise and reliability.
Incorporating a maintenance-friendly design, leading needle valves allow for easy disassembly and cleaning, a feature cherished by professionals who understand the value of minimizing downtimes. This design reflects the manufacturer's insight into the real-world challenges faced by users, further establishing their authority and trustworthiness.
User reviews are another credible source of first-hand experience. They provide insights into long-term performance and real-world efficiencies. Established manufacturers with consistently positive feedback often provide after-sales support and guidance, illustrating their ongoing commitment to their products and customer satisfaction.
As you conclude your decision-making process, always look for certified products that meet industry standards and regulations. Certifications from recognized bodies serve as a credible endorsement, ensuring the product's legitimacy and its alignment with best practice benchmarks.
Ultimately, an instrument needle valve is more than just a component; it's a critical part of a larger system. Selecting the right one requires considering precision, material quality, adaptability, and trusted performance. By aligning with experts and leveraging verified experiences, you'll secure a needle valve that not only serves efficiently but also augments the overall integrity and safety of your operations.