In the industrial world, the significance of pipe fittings reducers cannot be overstated. These essential components play a pivotal role in systems where varying pipe sizes need to be connected seamlessly, ensuring efficient flow and pressure management. A deep dive into the world of pipe fittings reducers reveals a fascinating blend of engineering, mechanics, and materials science.
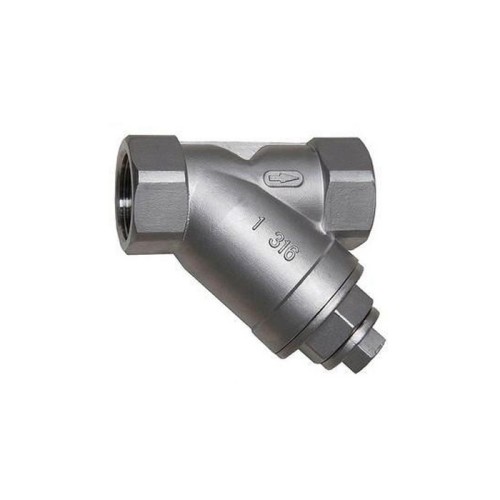
Pipe fittings reducers come in two main types concentric and eccentric. Concentric reducers are typically deployed in vertical piping systems. Their symmetrical shape ensures even distribution of pressure, thus minimizing the risk of turbulence and cavitation. This makes them ideal for applications involving fluid flow that must maintain a consistent velocity and direction. In contrast, eccentric reducers are often used in horizontal piping systems. Their off-center alignment helps in avoiding the accumulation of air bubbles or pockets, making them indispensable in scenarios where pressurized liquid needs to be drained or flushed effectively.
The material choice for a pipe fitting reducer is crucial, given that it must withstand various environmental conditions, pressures, and chemical exposures. Common materials include stainless steel, carbon steel, and PVC. Stainless steel reducers are renowned for their durability and high resistance to corrosion, which makes them suitable for harsh environments, such as those found in chemical processing plants. Carbon steel reducers, while not as corrosion-resistant, offer excellent strength and are cost-effective for use in general industrial applications. PVC reducers, on the other hand, are ideal for low-pressure and non-corrosive environments, providing a lightweight and cost-efficient solution.
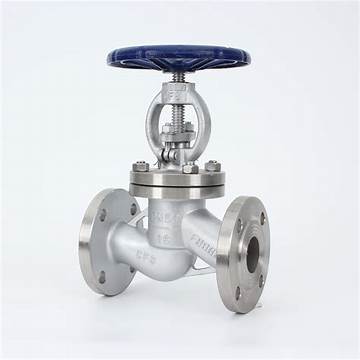
From an engineering perspective, one of the biggest challenges in designing and selecting reducers is ensuring compatibility across different piping standards and sizes. Engineers must carefully consider factors such as wall thickness, pressure rating, and temperature tolerance. This necessitates a profound understanding of the piping system's operational environment and the specific requirements of the process flow.
pipe fittings reducer
Installation expertise is another critical component in the effective utilization of pipe fittings reducers. Proper alignment and secure fitting are paramount to prevent leaks and ensure a long lifespan for the piping system. Misalignment can lead to increased wear, potential failures, and costly maintenance. Therefore, employing skilled technicians who are adept at interpreting engineering diagrams and executing precise installation procedures is essential.
Innovative developments in manufacturing technologies have further enhanced the capabilities of pipe fittings reducers. Advanced techniques such as 3D printing and laser cutting have allowed for the production of custom reducers with exceptional precision, tailored to specific industrial needs. Furthermore, these technologies contribute to reduced waste and improved sustainability efforts in the manufacturing process.
The authority and credibility of a manufacturer or supplier are vital considerations when selecting pipe fittings reducers. Established brands with a proven track record often provide detailed product certifications and adhere to international standards, ensuring reliability and safety. These manufacturers frequently offer extensive warranties and after-sales support, which are invaluable in maintaining a secure and efficient piping system.
In conclusion, pipe fittings reducers are indispensable components of modern industrial piping systems. Their ability to accommodate varying pipe sizes while ensuring optimal flow dynamics underscores their importance across various industries. The expertise involved in their design, material selection, and installation speaks volumes of their complexity and essentiality. As technological advancements continue to evolve, the future of pipe fittings reducers promises even greater efficiency and innovation, solidifying their role in the engineering landscape.