Gate valve flanges play an essential role in numerous industrial applications, providing connectivity and support to the gate valves that control fluid flow. This article aims to unravel the complexities and nuances of gate valve flanges, focusing on the aspects that make them crucial components in the machinery and construction sectors.
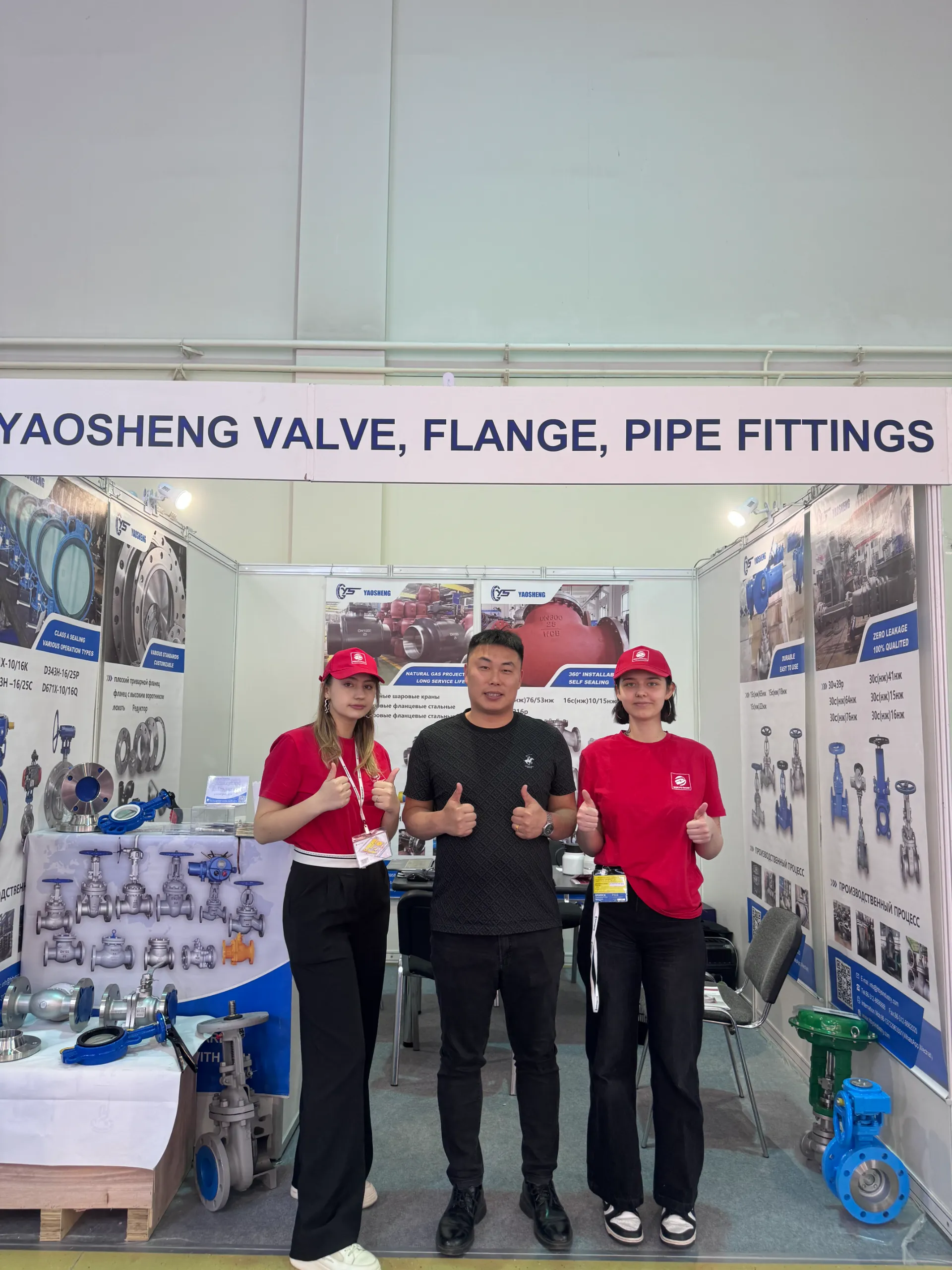
Gate valve flanges are designed to ensure a robust connection system which aids in reducing leakages, vibration, and unwanted pressure loss in piping systems. When selecting the appropriate gate valve flange, various material compositions come into play, such as stainless steel, carbon steel, and alloys, each suited for different environmental and operational requirements. Stainless steel flanges, for instance, are renowned for their durability and resistance to corrosion, making them ideal for applications involving harsh chemical processing environments.
Installation and material compatibility are key areas of expertise when it comes to maximizing the efficacy of gate valve flanges. It is essential to match the flange material to the valve it connects to, ensuring uniform stress distribution and temperature tolerance. Experienced engineers often conduct thorough inspections to check for surface defects and dimensional inaccuracies, which can severely impact flange performance.
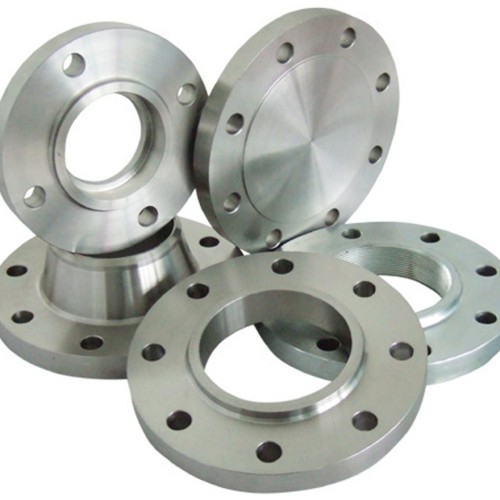
Another critical consideration is the pressure class rating of the flange, which determines its suitability for various pressure environments, ranging from low to very high pressures. This rating, based on the American Society of Mechanical Engineers (ASME) standards, ensures that users align the operating conditions with the flange's structural capabilities, thereby maintaining system safety and performance reliability.
For those involved in the procurement or maintenance of industrial piping systems, understanding the flange face types is paramount. These include flat face (FF), raised face (RF), and ring-type joint (RTJ), each offering unique sealing capabilities for different operational environments. For example, RF flanges are widely used due to their versatility and are highly favored in settings where thermal fluctuations are prevalent.
gate valve flange
Expert-level insights from industry professionals emphasize the need for regular maintenance checks on gate valve flanges to ensure the long-term integrity of the system. Routine inspections can identify issues such as signs of wear, corrosion, or misalignment before they escalate into critical failures. Advanced non-destructive testing (NDT) methods, such as magnetic particle inspection or ultrasonic testing, are recommended to precisely evaluate flange condition without dismantling the system.
For authoritative guidelines and enhanced trustworthiness in handling gate valve flanges, regulatory compliance with standards such as the ASME B16.
5 for pipe flanges and flanged fittings is vital. Professionals in the field are advised to stay updated on evolving regulations and industry best practices to safeguard operational integrity and legal compliance.
The integration of technology within the realm of gate valve flange applications cannot be overstated. Smart technologies facilitate real-time monitoring and feedback, allowing for predictive maintenance strategies that can increase the lifespan of these components and reduce downtime. By incorporating sensors and leveraging data analytics, industries can optimize flange performance, predicting wear and tear while planning refurbishments or replacements in advance.
Ultimately, the authoritative use of gate valve flanges hinges on precise engineering, material adaptation, adherence to standards, and innovative maintenance strategies. For businesses seeking to leverage these flanges in their operational setups, fostering a relationship with reputable manufacturers and suppliers who demonstrate industry expertise is crucial. Their insights play a pivotal role in tailoring flange solutions to specific industry needs, ensuring a seamless integration that upholds fluid dynamics needs and operational efficiency.
Emphasizing the value of trust within supplier relationships can lead to access to cutting-edge flange technologies and materials, setting the stage for scalable operations that meet the ever-evolving demands of industrial applications. By anchoring on trustworthiness, manufacturers can present themselves not just as providers, but as partners committed to advancing reliability and innovation within the realm of gate valve flanges.