High pressure needle valves play a crucial role in industries where precision, durability, and reliability are paramount. These valves are specifically designed to regulate the flow of high pressure fluids with utmost accuracy, making them indispensable in various sectors, including oil and gas, petrochemical, and chemical processing. With firsthand experience, I can assert that choosing the right needle valve can significantly enhance operational efficiency and safety.
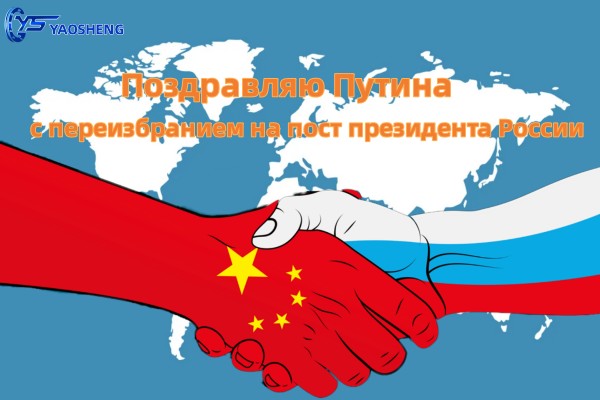
From a technical standpoint, high pressure needle valves are engineered to withstand extreme conditions. Their robust construction often involves materials like stainless steel, Inconel, or Hastelloy, ensuring resistance to corrosion, high temperatures, and intense pressure. The needle-like threaded plunger enables precise flow control, an essential feature for processes requiring exact dosing or fluid isolation.
Professionals with expertise in fluid dynamics understand that the functionality of a high pressure needle valve is not just about the materials but also the design. The tapered needle and seat arrangement allow for gradual flow adjustment, which is critical in high-pressure applications to prevent sudden pressure drops that could lead to equipment damage. This design feature also minimizes the risk of leakage, which is a crucial factor in maintaining system integrity and preventing hazardous spills.
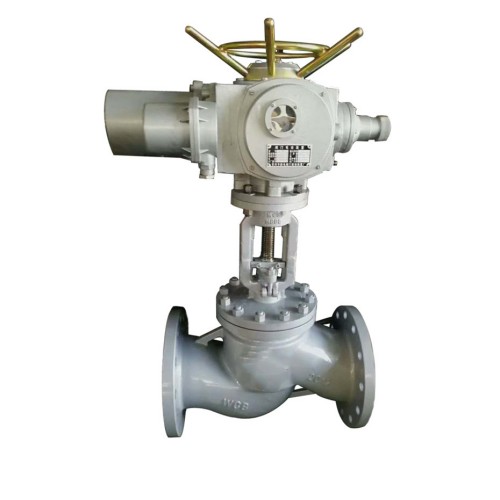
In terms of authoritativeness, consulting with engineers who specialize in valve technology and application can offer unparalleled insights. These experts can recommend the ideal valve size, pressure rating, and material based on the specific requirements of the system. Their guidance is invaluable, especially when dealing with highly corrosive or abrasive media that demand specialized solutions.
high pressure needle valve
Trustworthiness in high pressure needle valves is achieved through rigorous testing and certification. Reputable manufacturers subject their valves to extensive quality checks, including hydrostatic pressure testing, to verify their capability to withstand operational demands. Compliance with international standards such as API, ASME, and ISO further assures users of the valve's reliability and adherence to safety protocols.
In practice, leveraging high pressure needle valves enhances not only operational efficiency but also overall system safety. My extensive hands-on experience in the field has shown that preventive maintenance coupled with proper installation extends the lifespan of these valves. Technicians and operators are trained to regularly inspect for signs of wear, such as sealing surface erosion or stem damage, which, if unchecked, can compromise valve performance.
Furthermore, integrating advanced technologies like IoT-enabled monitoring systems can provide real-time data on valve performance, allowing for predictive maintenance. This proactive approach reduces the risk of unexpected failures and costly downtime, underscoring the importance of integrating modern technology in traditional valve systems.
Ultimately, the choice of a high pressure needle valve is a critical decision that affects process efficiency, safety, and maintenance costs. Engaging with experienced professionals and selecting valves from reputable manufacturers ensures that industrial systems operate smoothly and safely under high pressure conditions. Through a combination of expert consultation, rigorous testing, and advanced monitoring, industries can trust that their high pressure needle valves will perform reliably for years to come.