Understanding the 2 Threaded Ball Valve An Insight into Factory Production
In the world of industrial plumbing and fluid control systems, the 2 threaded ball valve stands as a crucial component, playing a pivotal role in regulating flow with precision and efficiency. This article delves into the manufacturing process of these valves, highlighting the intricacies and technological advancements that take place within the factory walls.
A 2 threaded ball valve, as the name suggests, is a valve with a diameter of 2 inches that features a spherical disc, the 'ball', as its primary mechanism. The ball has a bore through its center, which aligns with the valve's flow path when open, allowing fluid to pass. When rotated 90 degrees, the bore becomes perpendicular to the flow path, thereby blocking it, thus making it a highly efficient on/off valve.
The production of such a valve begins with raw material selection. High-quality materials like stainless steel, brass, or carbon steel are commonly used, chosen for their durability, corrosion resistance, and ability to withstand high pressure and temperature variations. These materials are then transformed into the required shapes through processes like forging, casting, or machining.
In the factory, the ball is precisely machined to ensure a perfect fit within the valve body. The threading process follows, where threads are cut onto the valve body and stem to allow for easy installation and removal. This is a critical step, as any deviation in thread quality could affect the valve's functionality and compatibility with other pipe fittings.
The seating mechanism, often made from resilient materials like PTFE (Teflon) or metal, is then added to ensure a leak-proof seal
The seating mechanism, often made from resilient materials like PTFE (Teflon) or metal, is then added to ensure a leak-proof seal
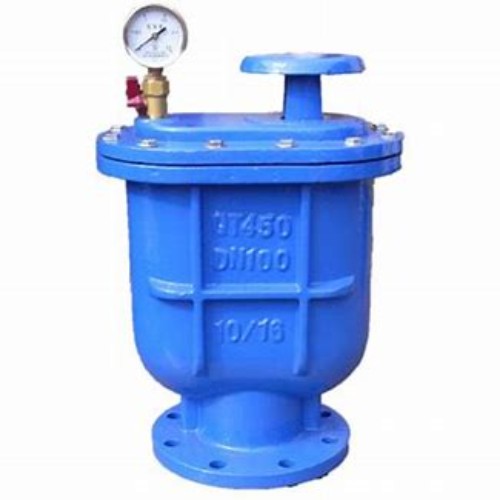
The seating mechanism, often made from resilient materials like PTFE (Teflon) or metal, is then added to ensure a leak-proof seal
The seating mechanism, often made from resilient materials like PTFE (Teflon) or metal, is then added to ensure a leak-proof seal
2 inch threaded ball valve factory. The ball is then inserted into the body, and the stem connected, allowing the ball to rotate and control the flow. Quality control checks are conducted at every stage to ensure compliance with industry standards and customer specifications.
Post-assembly, the valves undergo rigorous testing. Pressure tests are conducted to verify their sealing performance, while life cycle tests simulate prolonged usage to assess durability. Any faulty units are identified and rectified before they leave the factory.
The factory also incorporates advanced technologies like Computer-Aided Design (CAD) and Computer-Aided Manufacturing (CAM) to streamline the design and production process. These tools enable the creation of intricate valve designs and precision machining, enhancing both efficiency and accuracy.
In conclusion, the production of a 2 threaded ball valve in a factory is a testament to engineering prowess and precision manufacturing. It's a complex process that combines skilled craftsmanship with cutting-edge technology, all aimed at delivering a product that can reliably control fluid flow in various industrial applications. Understanding this process underscores the value of these seemingly simple yet vital components in our everyday infrastructure.