The Unparalleled Excellence of Weld Neck Flanges A Pioneering Solution in Pipeline Integrity
In the realm of industrial engineering and pipeline systems, one component that stands out for its robustness and efficiency is the weld neck flange. Often referred to as a WN or WNF, this specialized fitting has become a cornerstone in ensuring the seamless flow of fluids and gases across various industries, from oil and gas to chemical processing.
Weld neck flanges, with their distinctive design, feature a raised ring on the pipe's shoulder that transitions seamlessly into the pipe wall. This unique structure makes them ideal for high-pressure and high-temperature applications where integrity is paramount. The term weld neck refers to the fact that the pipe is directly welded to the flange, eliminating the need for or threaded connections, thus minimizing potential leaks and enhancing safety.
The manufacturing process of a weld neck flange is meticulous, utilizing advanced forging techniques to create a strong, uniform body that can withstand immense loads. The critical weld lines are placed at the base, ensuring that the connection between the pipe and the flange is as strong as possible. This feature not only saves time during installation but also reduces the risk of stress corrosion cracking, a common issue with other types of flanges.
Moreover, the weld neck flange's ability to withstand repetitive thermal cycling, a characteristic of many industrial processes, makes it a reliable choice in environments where temperature fluctuations are frequent. Its robustness extends to its corrosion resistance, often treated with anti-corrosive coatings or materials to prolong service life in harsh conditions Its robustness extends to its corrosion resistance, often treated with anti-corrosive coatings or materials to prolong service life in harsh conditions
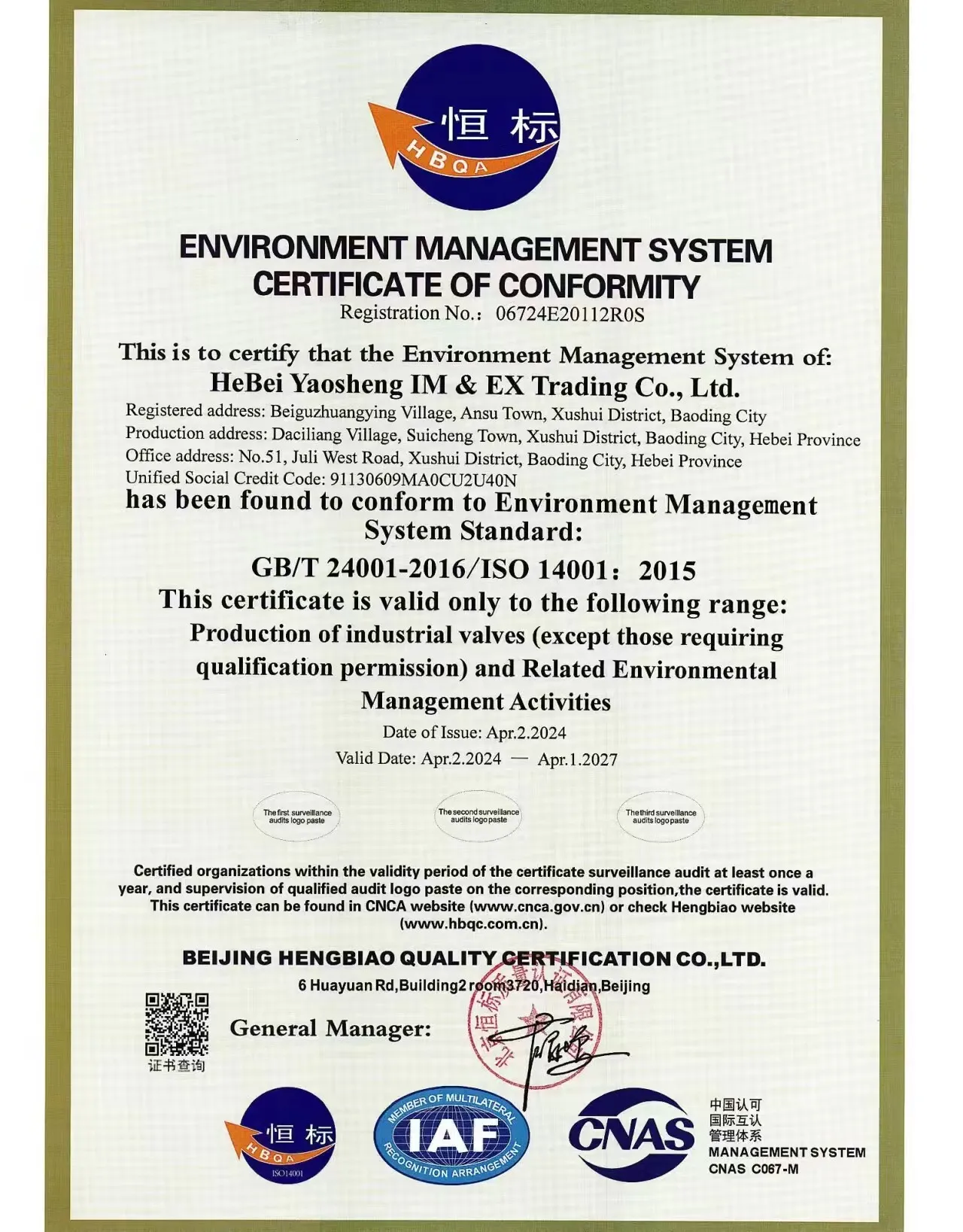
Its robustness extends to its corrosion resistance, often treated with anti-corrosive coatings or materials to prolong service life in harsh conditions Its robustness extends to its corrosion resistance, often treated with anti-corrosive coatings or materials to prolong service life in harsh conditions
weldneck flange.
In terms of maintenance, weld neck flanges are relatively easy to inspect and repair, as the entire pipe is accessible through the flange's flat face. This accessibility minimizes downtime and reduces overall operational costs, making them a cost-effective solution for long-term projects.
However, it's crucial to note that the selection of a weld neck flange depends on specific project requirements. It's not a one-size-fits-all solution, and engineers must carefully evaluate factors like pressure ratings, material compatibility, and environmental conditions before specifying them.
In conclusion, the weld neck flange, with its combination of strength, durability, and ease of maintenance, has revolutionized pipeline design and operation. Its role in ensuring reliability, safety, and efficiency in industrial processes cannot be overstated. As technology advances and industries continue to push boundaries, the weld neck flange remains a testament to the power of engineering innovation and the pursuit of excellence in materials science.