Understanding the Significance of 12 Inch Check Valve Manufacturing in Industrial Processes
In the complex world of industrial engineering, a seemingly small component can play a monumental role. The 12 inch check valve factory is one such example, where precision manufacturing and quality control meet to ensure seamless fluid management systems. This article delves into the intricacies of these valves, their function, and the importance of their manufacturing process.
A check valve, often referred to as a non-return valve, is a simple device that allows fluid to flow through it in only one direction. It automatically prevents backflow, ensuring the directional flow in pipelines. In the context of a 12 inch model, we are referring to a valve designed to accommodate large-scale operations, typically found in heavy-duty industrial applications such as oil and gas, water treatment, and chemical processing plants.
The size of the valve - 12 inches in this case - signifies its capacity to manage substantial fluid volumes. This makes them indispensable for maintaining the integrity of large pipeline networks, preventing reverse flow which could lead to equipment damage or process disruptions.
The manufacturing process of a 12 inch check valve is a blend of art and science. It begins with the selection of high-grade materials that can withstand extreme conditions, such as high pressure, temperature fluctuations, and corrosive fluids. These materials might include stainless steel, carbon steel, or specialized alloys, depending on the specific application requirements.
The production line then involves precision machining, welding, and assembly, all under stringent quality control measures. Each valve undergoes rigorous testing, including pressure tests and functionality checks, to ensure they meet industry standards and client specifications Each valve undergoes rigorous testing, including pressure tests and functionality checks, to ensure they meet industry standards and client specifications
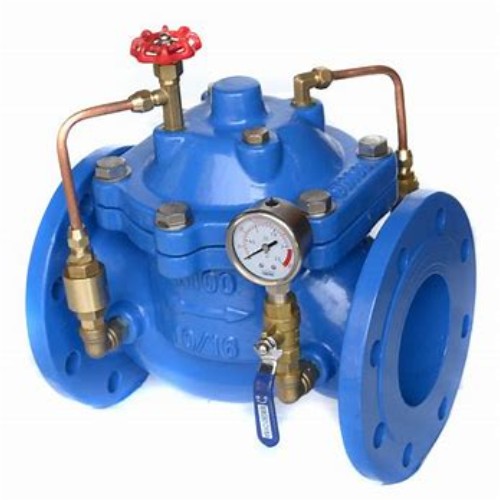
Each valve undergoes rigorous testing, including pressure tests and functionality checks, to ensure they meet industry standards and client specifications Each valve undergoes rigorous testing, including pressure tests and functionality checks, to ensure they meet industry standards and client specifications
12 inch check valve factory. This attention to detail guarantees reliable performance even in the most demanding environments.
The 12 inch check valve factories are not just manufacturing units; they are centers of innovation and technological advancement. They continuously adapt to evolving industry needs, incorporating new designs, materials, and technologies to enhance efficiency, durability, and safety. For instance, some factories now produce valves with noise reduction features, anti-corrosion coatings, or remote monitoring capabilities.
Moreover, the economic impact of these factories cannot be overlooked. They contribute significantly to local economies by providing jobs, fostering technical expertise, and driving exports. Their products play a vital role in global infrastructure, ensuring the smooth operation of industries that form the backbone of many economies.
In conclusion, the 12 inch check valve factory represents more than just a production facility; it symbolizes the intersection of engineering excellence, industrial safety, and economic prosperity. Its role in safeguarding critical processes, preventing potential disasters, and enabling efficient flow management underscores the importance of investing in high-quality valve manufacturing. As technology advances and industry demands evolve, these factories will continue to innovate, pushing the boundaries of what a simple yet essential component like a check valve can achieve.