Grooved butterfly valves have long been a cornerstone in the fluid handling and control industry, offering robust functionality combined with notable ease of installation and maintenance. Within the domain of fluid dynamics, these valves are celebrated for their efficiency and reliability, serving an array of purposes from industrial to commercial applications.
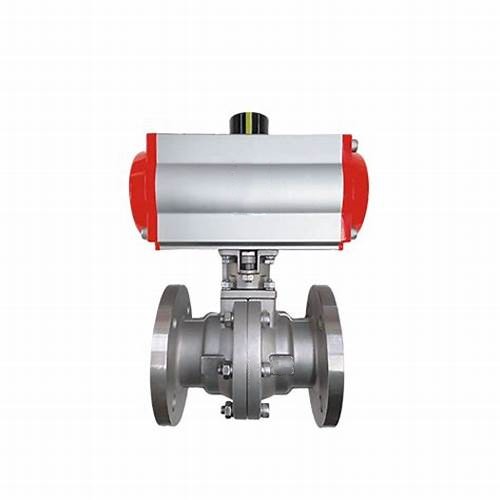
The grooved butterfly valve stands out due to its unique structural engineering which incorporates grooves into the valve design. This feature significantly facilitates the attachment process, mitigating the need for complex welding or flanging procedures typically involved in valve fittings. By allowing for easy alignment with piping systems, grooved butterfly valves mark a substantial evolution in valve technology, streamlining installation procedures while ensuring secure and stable connections.
High on the list of advantages provided by grooved butterfly valves is their adaptability to a wide range of pressure scenarios. Constructed with materials known for enduring durability, such as cast iron, ductile iron, or even specialized alloys, these valves cater to diverse industry requirements. In explosive settings such as chemical processing plants or oil refineries, their ability to withstand harsh environments underscores their authoritative role in maintaining operational safety and efficiency.
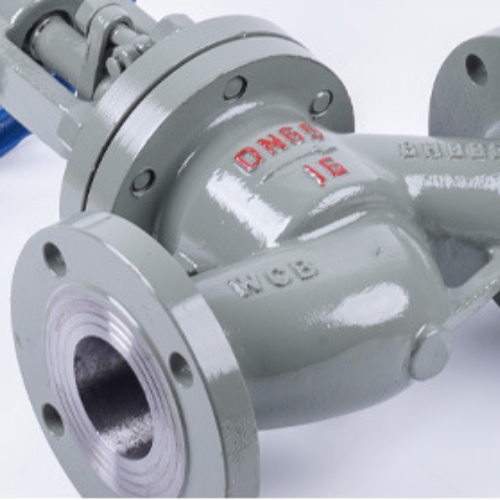
Further enriching their experience-backed value, grooved butterfly valves are known for providing unparalleled operational ease. The strategic inclusion of a disk that pivots on an axis within the pipe enables swift open or close functions, hence controlling the flow of liquids with precision. This mechanism not only conserves energy but also ensures a steady flow, minimizing the risk of leakage or pressure drop—an advantage that professionals across the fluid handling sector continuously heed.
Moreover, these valves are entrenched in expert engineering principles that comprehensively address wear and tear, prolonging lifecycle and reducing the need for frequent replacements. By ensuring key components such as the stem and seat are crafted from high-quality, wear-resistant materials, manufacturers have demonstrated a keen understanding of long-term value and performance, making these valves a preferred choice for large-scale operations.
grooved butterfly valve
Trustworthiness in a grooved butterfly valve is further solidified through rigorous compliance with industry standards. Manufacturers align product specifications with international standards such as ISO or API, providing assurances of quality control and functional reliability. Professionals in the field rely heavily on these benchmarks when selecting components for intricate systems, emphasizing the valve's authoritative role in maintaining systemic integrity.
Incorporating these valves into a larger operational framework can also yield noteworthy cost benefits. By reducing installation and maintenance time due to their user-friendly design, organizations stand to achieve significant financial savings. The reduced weight and compact build of grooved butterfly valves translate directly to lower transportation and handling costs, further burnishing their appeal to budget-conscious industrial buyers.
When it comes to expertise in fluid control, selecting the right equipment can significantly influence operational outcomes. The grooved butterfly valve, with its combination of leading-edge design and material resilience, manifests a tangible edge over alternate solutions. Professionals equipped with detailed knowledge of these valves invariably contribute to the smoother running of facilities, enhancing productivity and securing compliance with increasingly stringent operational standards.
Ultimately, in evaluating the intricate balance between innovation and practicality, grooved butterfly valves embody an ideal choice. Their proven record of performance in demanding applications consolidates their standing as a pivotal component in modern fluid handling systems. For businesses and engineers committed to upholding the highest standards of excellence and durability, these valves represent not only a critical functional component but a testament to engineered precision.