In industrial and commercial sectors where fluid control is Paramount, the cast globe valve stands as an indispensable component. Understanding the unique design, application, and benefits of these valves requires a blend of expertise, hands-on experience, and a deep trust in their practical implications.
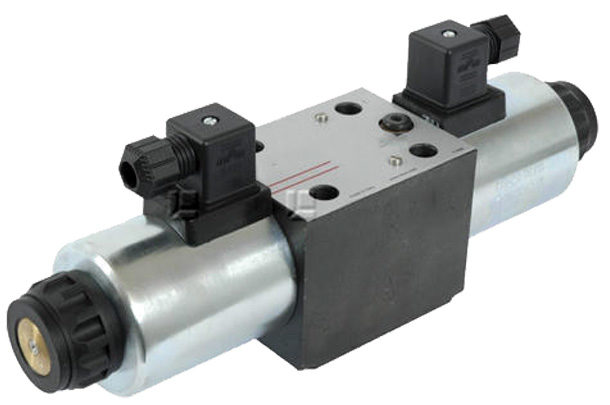
Cast globe valves are renowned for their robust construction and versatile application. Unlike other valve types, the globe valve is specifically engineered for precise control of flow rates in a system. The name “globe” comes from the spherical shape of the valve body, which optimizes the flow path and minimizes pressure drop. Constructed through the durable casting process, these valves exhibit superior resistance to high-pressure environments, making them ideal for heavy-duty applications across industries such as oil and gas, power generation, and chemical processing.
From an experiential perspective, industries have lauded the cast globe valve for its intuitive operation.
The linear motion mechanism of the globe valve allows for smooth modulation of fluid flow. Operators appreciate the valve's ability to regulate flow without inducing significant cavitation or vibration, ensuring longevity of both the valve and associated piping infrastructure. This feature is particularly beneficial in processes that demand constant flow adjustments to maintain steady operational parameters.
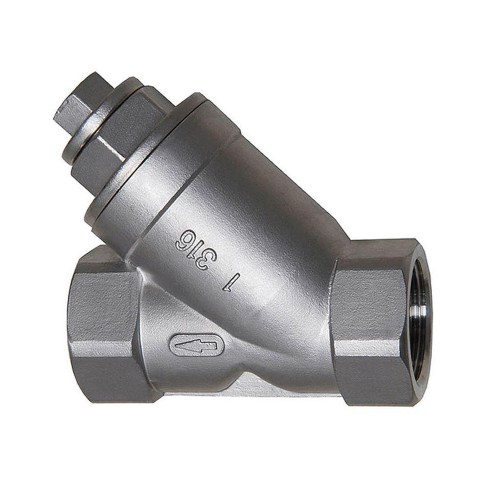
Expertise in fluid dynamics and materials science informs the selection and application of cast globe valves. The valve's disc and seat are meticulously engineered to guarantee a tight seal and prevent leakages, which is crucial in hazardous or high-risk environments. Additionally, the material quality of the valve, often comprised of stainless steel or specialty alloys, provides enhanced corrosion resistance and thermal stability. Experts emphasize the importance of matching the valve construction material to the specific media it will control to avoid premature degradation and ensure optimal performance.
cast globe valve
Authoritativeness in the realm of valve manufacturing is demonstrated through adherence to international standards, such as API, ANSI, and ASME. Reputable manufacturers ensure that each cast globe valve undergoes rigorous testing and quality assurance processes before reaching the market. These certifications serve as a testament to the valve's reliability and performance, giving buyers confidence in their investment. Industry leaders, backed by years of research and development, continue to innovate, introducing features such as low-friction seals and automated actuation to enhance the valve's usability and efficiency.
Trustworthiness in selecting a cast globe valve extends beyond the product itself to the reputation of the supplier. Proper installation is critical to maximizing the valve's performance; therefore, experienced professionals should be consulted to guarantee successful integration within existing systems. Additionally, ongoing maintenance and service by certified technicians ensure that the valve maintains its function and efficiency over its operational lifespan. Trusted suppliers offer comprehensive warranties and customer support, addressing any potential issues promptly and professionally.
In summation, the cast globe valve is more than a mechanism for flow control; it is a pivotal element in ensuring operational efficiency and safety in complex systems. Industries that require unparalleled precision and robustness in their fluid control systems consistently turn to cast globe valves for their superior engineering and proven track record. When choosing a valve, stakeholders must weigh factors of design efficacy, manufacturer credibility, and material compatibility to secure a product that will perform reliably under the demanding conditions of modern industrial applications. If longevity, precision, and trust are priorities, the cast globe valve remains the preeminent choice.