High temperature butterfly valves are indispensable components used in various industries for regulating fluid flow at elevated temperatures. These specialized valves boast remarkable resilience, making them suitable for applications where standard valves might fail. Based on hands-on expertise and profound industry knowledge, this overview delves into their design, applications, and benefits that make them a preferred choice in demanding environments.
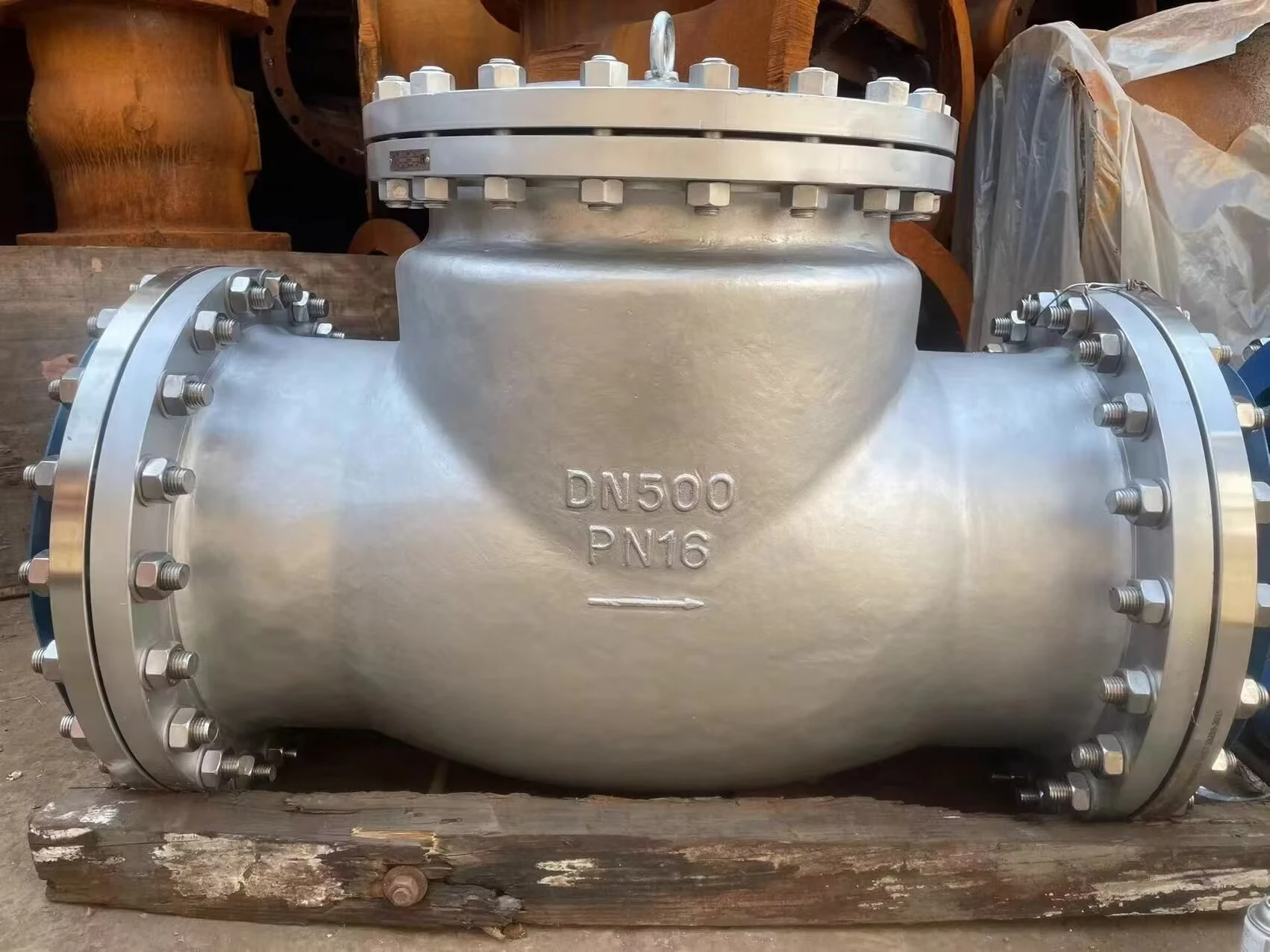
High temperature butterfly valves are known for their robust engineering, designed to withstand intense thermal conditions. They generally consist of a round disc mounted on a rotating shaft, which is key to controlling flow. The design allows for quick shut-off, akin to the turning of a butterfly’s wings, hence the name. Their construction involves materials such as stainless steel, Inconel, or Hastelloy, which are known for their superior heat resistance and durability under stress. These specialized materials help maintain the valve's integrity, even when subjected to high degrees of thermal expansion and contraction.
The applications for these valves span across various high-demand industries. In the petrochemical sector, they play a critical role in managing the flow of crude oil and natural gas during processing. Within power generation, especially in coal-fired plants, high temperature butterfly valves are crucial in the circulation of steam and combustion gases. Similarly, in the manufacturing of steel and other metals, these valves ensure efficient furnace operations by controlling the flow and pressure of gases used in heating processes.
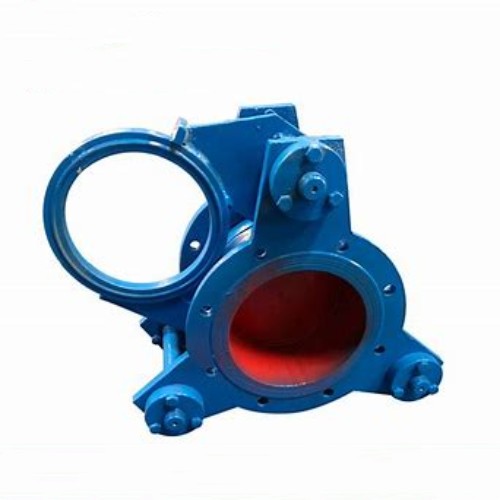
One of the key advantages of high temperature butterfly valves lies in their compact and lighter structure compared to other types of valves, such as gate or globe valves. This not only makes installation more manageable but also reduces the overall weight burden on piping systems. From a performance standpoint, their design offers minimal resistance to fluid flow, which translates to less pressure loss and energy efficiency — a crucial consideration in large-scale industrial systems aiming to minimize operational costs.
high temperature butterfly valve
Further strengthening their allure is the low maintenance requirement. Given their simplistic design with fewer moving parts, these valves experience reduced wear and tear over time. Replaceable seat rings are common, offering an economical means to extend valve service life without necessitating complete valve replacement. This feature further enhances trustworthiness, as plant operators can rely on their sustained performance without frequent interventions.
Choosing a high temperature butterfly valve should involve assessing the specific needs of the application, such as the degree of temperature, pressure conditions, and type of medium that will flow through the system. Collaborating with credible suppliers who have an extensive track record increases the assurance of acquiring valves that meet these stringent demands. Always ensure compliance with relevant industry standards like API, ANSI, or ASME to uphold operational safety and efficiency.
In conclusion, high temperature butterfly valves represent a vital segment of industrial equipment focused on performance and reliability. Their expertise-backed design, coupled with their cost-effective operation and reduced maintenance needs, paves the way for their continued prominence in industries dealing with high-temperature applications. Making informed choices backed by authoritative sources assures investments in these valves yield consistent outcomes, aligning with both production objectives and safety standards.