Pneumatic actuated butterfly valves have evolved into indispensable components in the industrial landscape, particularly revered for their efficiency and reliability. As an advanced, cutting-edge solution, these valves facilitate seamless flow control in various systems, aiding industries that span from water treatment to chemical processing. Examining their design intricacies and advantages reveals why they are a preferred choice in modern engineering applications.
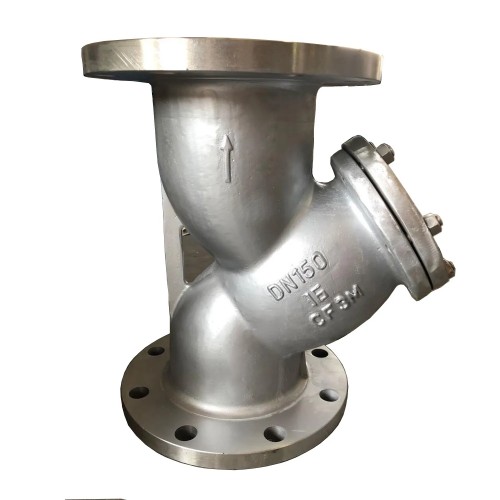
In essence, a pneumatic actuated butterfly valve operates through a circular disc or vane that rotates within the pipe to control fluid flow. The prime allure of using a pneumatic actuator in this scenario lies in its simplicity, speed, and efficiency. Unlike manual or electric actuators, pneumatic systems harness the power of compressed air to initiate movement, enabling rapid and precise control of the valve disc's orientation. This capability ensures minimal pressure drop while maximizing flow rate, an essential factor in high-demand environments.
One of the standout features of pneumatic actuated butterfly valves is their compact design, allowing for easy integration into existing piping systems without necessitating additional space. This makes them particularly advantageous in retrofitting projects or in industries where space is a premium commodity. Furthermore, their relatively lightweight construction reduces the overall system weight, which can significantly impact systems where load considerations are crucial.
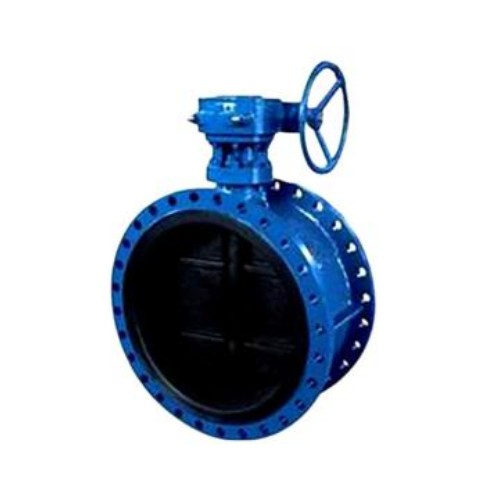
From an operational standpoint, the enhanced durability and reduced maintenance requirements of these valves are notable. Constructed with robust materials such as stainless steel, they offer excellent resistance against corrosion and environmental wear and tear. This aspect critically extends the life of the valve, ensuring consistent performance over time. Moreover, the pneumatic actuation system itself requires less upkeep compared to electrical systems, reducing downtime and maintenance costs.
pneumatic actuated butterfly valve
The precision afforded by pneumatic actuated butterfly valves is another key advantage. In applications requiring fine-tuned control over flow rates—such as in pharmaceuticals or food and beverage industries—the ability to quickly adjust and maintain exact flow parameters is paramount. These valves provide consistent and repeatable operation, facilitating high-quality production processes.
Safety, an indispensable aspect in any industrial setting, is impressively bolstered with pneumatic actuated systems. The absence of electrical components minimizes the risk of sparks, making these valves ideal for flammable environments. In addition, they are typically robust enough to handle varied pressure environments without compromising functionality, adding an extra layer of security and reliability.
As industries continually strive towards sustainable practices, the energy efficiency of pneumatic actuated butterfly valves cannot be overstated. Utilizing compressed air, an energy source often readily available in industrial settings, means less reliance on electricity which aligns with energy-saving initiatives. The reduced energy consumption contributes not only to lowered operational costs but also aligns with the global trend towards environmentally conscious industrial operations.
In conclusion, pneumatic actuated butterfly valves stand as a testament to mechanical ingenuity, offering robust, efficient, and reliable flow control solutions across various industries. Their design simplicity, coupled with operational efficacy, renders them an essential component for any modern industrial system, reinforcing productivity and ensuring the highest standards of operational excellence. As industries evolve, leveraging such cutting-edge technologies will undoubtedly be pivotal in achieving optimized engineering outcomes.