Pneumatically actuated butterfly valves have become indispensable components in various industries due to their efficiency, reliability, and speed in controlling flow. Whether you are involved in the chemical, water treatment, food and beverage, or oil and gas industries, these valves offer a robust solution for managing fluid dynamics. Understanding their construction, functionality, and applications can offer deeper insights into why they are an advantageous choice.
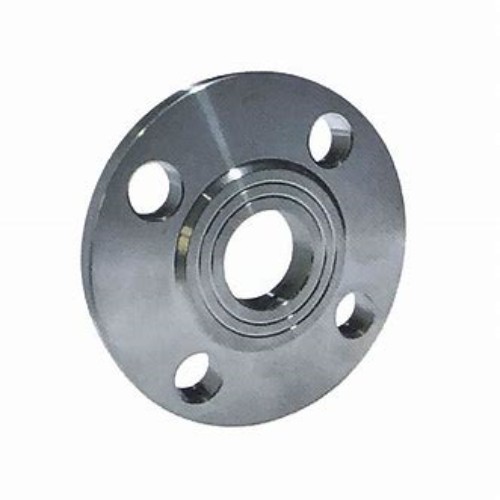
Pneumatically actuated butterfly valves operate by utilizing compressed air to manipulate the valve's disc position, which in turn modulates the flow of liquids, gases, or slurries. The core component, the disc, is centrally located in the pipe and operates via a shaft that is either connected directly to the actuator or indirectly through gears. This design ensures a quick response time, which is critical for applications requiring precise control.
From an engineering perspective, the efficiency of pneumatic butterfly valves lies in their simplistic yet effective design. Compared to other valve types such as gate or ball valves, butterfly valves are compact and lightweight, leading to lower installation costs and minimal space requirements. The actuator plays a crucial role, converting the energy of compressed air into mechanical motion. This energy conversion process is smooth and efficient, minimizing energy losses and enhancing operational reliability.
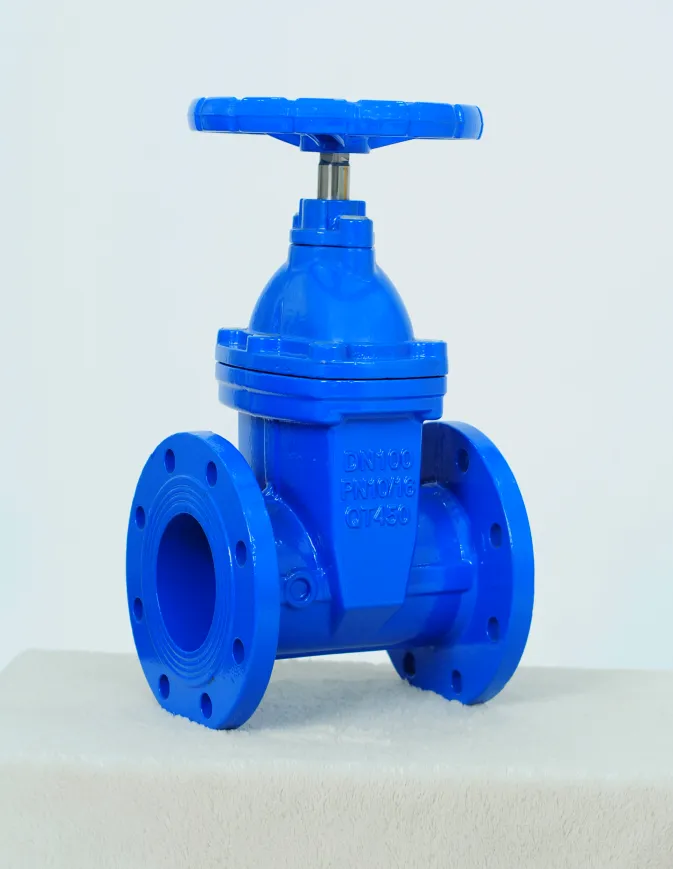
Moreover, advancements in materials technology have significantly improved the durability and performance of these valves. The discs are often constructed from stainless steel, which provides excellent resistance to corrosion and wear. In chemically aggressive environments, PTFE (Polytetrafluoroethylene) linings may be used to further resist chemical attack. For the body, materials can range from cast iron to more modern alloys, depending on the pressure and temperature conditions of the application.
pneumatically actuated butterfly valves
In terms of expertise, the precision control offered by pneumatical actuation allows users to fine-tune fluid dynamics with high accuracy, which is a critical requirement in industries such as pharmaceuticals, where precise mixing ratios are vital for product quality. Additionally, the integration of advanced control systems can further enhance their functionality. Modern pneumatic actuators can be equipped with smart positioners that facilitate remote monitoring and automated adjustments, thus allowing for more sophisticated system integrations with the Industrial Internet of Things (IIoT).
Authoritativeness in the domain is often supported by compliance with international standards and certifications. Renowned manufacturers ensure that their pneumatically actuated butterfly valves meet the high safety and quality standards set by global organizations such as the American Society of Mechanical Engineers (ASME) and the International Organization for Standardization (ISO). These certifications not only indicate superior quality but also reassure users of the product’s safety and reliability in critical applications.
Trustworthiness is further established through the proven track record and extensive applications of pneumatically actuated butterfly valves. Testimonials from industry leaders highlight how these valves have consistently provided dependable service in extremely challenging environments, from managing the flow of crude oil in off-shore rigs to controlling water supply in municipal treatment facilities. Their ability to perform reliably under high-pressure scenarios while minimizing leakage and energy consumption has cemented their reputation as a valuable component in fluid control systems.
In conclusion, the selection of pneumatically actuated butterfly valves is often justified by their superior design, engineering, and adaptability across various industrial applications. Their capability to offer precise control, endure harsh environmental conditions, and integrate seamlessly with modern technological solutions makes them a first-choice asset in the realm of fluid dynamics. By understanding their operational mechanics and benefits, users can make informed decisions to enhance the efficiency and reliability of their systems. As technology evolves, further enhancements in valve design and materials will continue to expand their application scope, affirming their vital role in modern industry infrastructure.