The high pressure check valve stands as a cornerstone in numerous industrial applications, meticulously engineered to ensure unidirectional flow and prevent costly backflow in systems where pressure variations are significant. These valves are stalwarts in industries like oil and gas, petrochemical, and water management, where high-pressure conditions demand robust solutions.
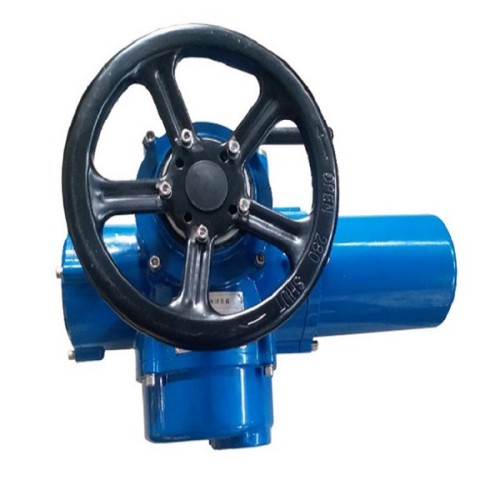
These devices operate with precision and reliability, making them indispensable for maintaining operational integrity. Crafted typically from high-grade materials such as stainless steel or brass, high pressure check valves are preferred for their corrosion resistance and durability. The choice of material often depends on the application's specific requirements, such as fluid type and temperature, ensuring that the valve performs optimally even in the most demanding conditions.
Expertise in high pressure check valve technology involves understanding their mechanics. At their core, these valves rely on a simple yet effective mechanism where pressure pushes a disc or ball into an open position, allowing fluid to flow through. If the pressure decreases or reverses, the disc or ball returns to the closed position, effectively sealing the passage. This automatic operation is crucial for systems where manual intervention is impractical.
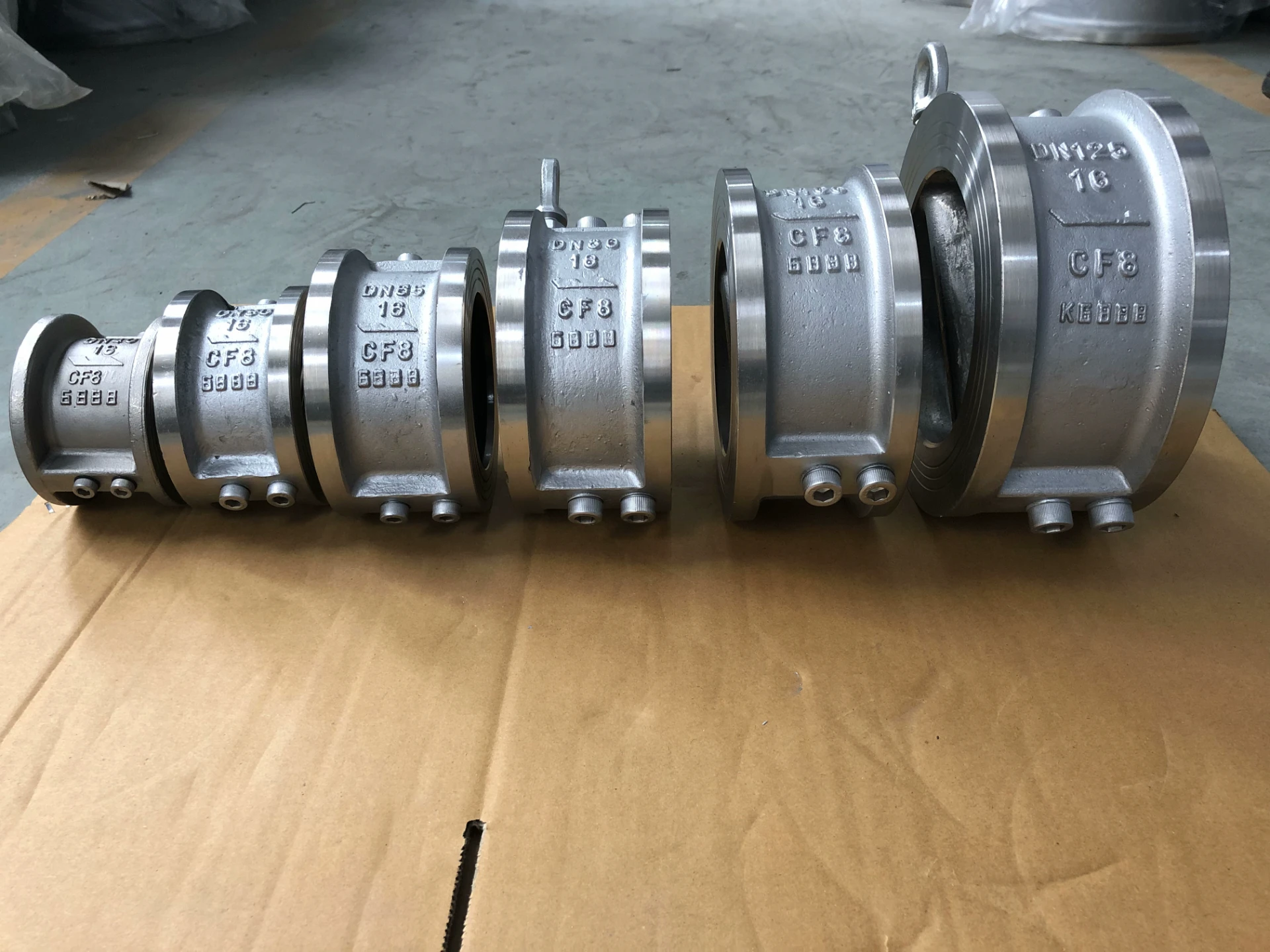
What sets apart high pressure check valves is their unparalleled reliability under extreme conditions. Engineers appreciate these valves for their ability to handle sudden pressure surges, which can otherwise destabilize a system. With minimal maintenance requirements, they represent a cost-effective solution over the long term. However, proper installation and periodic inspections are crucial to ensure their seamless operation and longevity.
high pressure check valve
From an expert's lens, it's vital to select the correct valve size and pressure rating. Mismatches in these specifications can lead to valve failure, system malfunction, or even safety hazards. Therefore, consulting with valve specialists or referring to detailed product datasheets can help in making informed choices, ensuring the valve meets the system's exact demands.
Trust in high pressure check valves is bolstered by rigorous testing and certification processes. Manufacturers often subject these valves to extensive pressure and thermal cycling tests to ensure that they meet international safety and performance standards. Certifications from bodies such as API, ASME, or ISO add a layer of confidence, validating that these valves can withstand the rigorous demands they are subjected to.
It is also essential to consider the layout and design of the system where these valves will be deployed.
A well-planned system helps in minimizing hydraulic losses and enhances the valve's effectiveness. Properly installed high pressure check valves not only contribute to the safety and efficiency of the system but also optimize the energy consumption, which is a critical consideration in energy-intensive industries.
In conclusion, high pressure check valves play a pivotal role in safeguarding industrial systems, ensuring fluid flow is consistent and reliable. Their design and material selection cater to specific needs, making them versatile components in diverse settings. With the backing of expert knowledge and rigorous standards, these valves offer peace of mind, empowering industries to focus on their core operations without the concern of flow disruptions.