The Art of Precision A Deeper Dive into Turbo Flange Manufacturers
In the realm of industrial engineering and high-performance machinery, turbo flanges hold a paramount position. These specialized components, often referred to as turbo flanges, are the vital connectors that facilitate the efficient transfer of energy and fluids in turbo machinery, such as turbo compressors and turbines. The manufacturing process for these intricate parts demands a unique blend of expertise, precision, and technological prowess.
Turbo flanges are not your ordinary fasteners; they are designed to withstand extreme temperatures, pressures, and rotational speeds. They are typically made from high-grade materials like stainless steel, Inconel, or titanium, each chosen for its superior strength, corrosion resistance, and heat tolerance. Manufacturers must adhere to strict industry standards, such as ASME B16.5, API 6A, or MSS SP-43, ensuring reliability and safety in even the most demanding environments.
The manufacturing process begins with meticulous planning and design. Advanced computer-aided design (CAD) software is utilized to create precise three-dimensional models, which are then optimized for manufacturability. Once the design is finalized, raw materials are precisely cut and shaped using state-of-the-art CNC machines, capable of achieving sub-millimeter accuracy.
Each step, from forging to machining, is critical. Forging helps to consolidate the material's grain structure, enhancing its strength and durability. Machining follows, where skilled artisans use various tools and techniques to achieve the required tolerances and surface finish Machining follows, where skilled artisans use various tools and techniques to achieve the required tolerances and surface finish
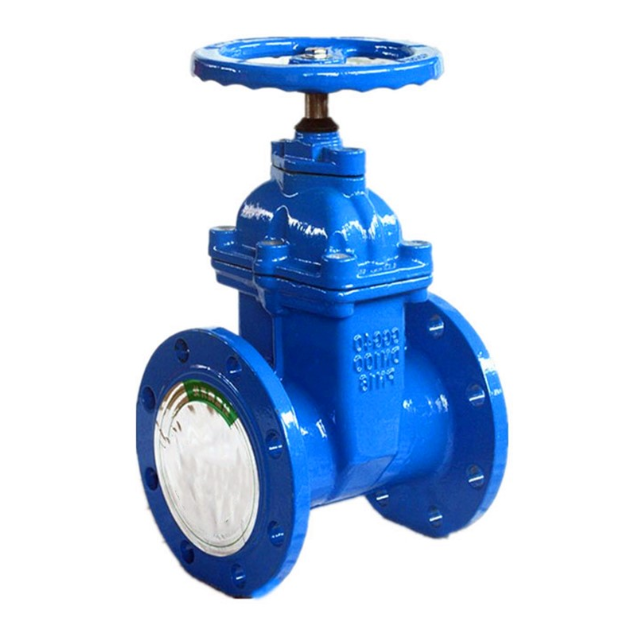
Machining follows, where skilled artisans use various tools and techniques to achieve the required tolerances and surface finish Machining follows, where skilled artisans use various tools and techniques to achieve the required tolerances and surface finish
turbo flanges manufacturer. This may involve drilling, threading, and honing to create the precise mating surfaces for a seamless seal.
Quality control is paramount in turbo flange manufacturing. Rigorous inspections, including non-destructive testing (NDT), are carried out at every stage to detect any defects or inconsistencies. This ensures that the final product meets the highest standards, minimizing the risk of failure under extreme operating conditions.
Moreover, many manufacturers invest in research and development to push the boundaries of innovation. They explore new materials, coatings, and designs to enhance performance, reduce weight, and extend service life. This commitment to continuous improvement is what sets top-tier turbo flange producers apart in an increasingly competitive market.
In conclusion, the world of turbo flange manufacturing is a testament to human ingenuity and engineering excellence. From conception to production, every aspect is a precision dance between technology and craftsmanship. As industries continue to evolve, so do the requirements for these vital components, driving manufacturers to refine their processes and deliver cutting-edge solutions. It is a journey that underscores the importance of reliable, high-quality turbo flanges in maintaining the efficiency and reliability of modern industrial systems.