Flanges are fundamental components in various industries, particularly in sectors that involve piping and mechanical assemblies. Their primary function is to connect pipes,
valves, pumps, and other equipment to form a complete piping system. By providing an easy way to assemble and disassemble parts, flanges prove invaluable for maintenance, repair, and system expansion. But beyond their basic applications, flanges are integral to ensuring safety, reliability, and performance in many critical operations.
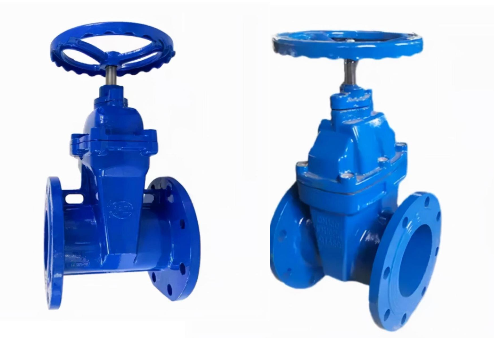
One of the most common materials used for flanges is stainless steel, renowned for its durability and resistance to corrosion and high temperatures. In high-stakes environments, such as chemical plants or offshore oil rigs, using stainless steel flanges ensures that the connections remain intact and leak-proof under challenging conditions. This reliability is essential for maintaining the integrity of the entire system, ultimately preventing costly shutdowns or catastrophic failures.
Moreover, flange design has evolved with technological advancements. Today, there are several types of flanges, each designed for specific purposes. For instance, slip-on flanges are known for their ease of installation; however, weld neck flanges provide superior strength, making them suitable for high-pressure and high-temperature applications. Blind flanges, on the other hand, are used to terminate the end of a piping system, offering the flexibility to easily access and extend the pipe if needed.
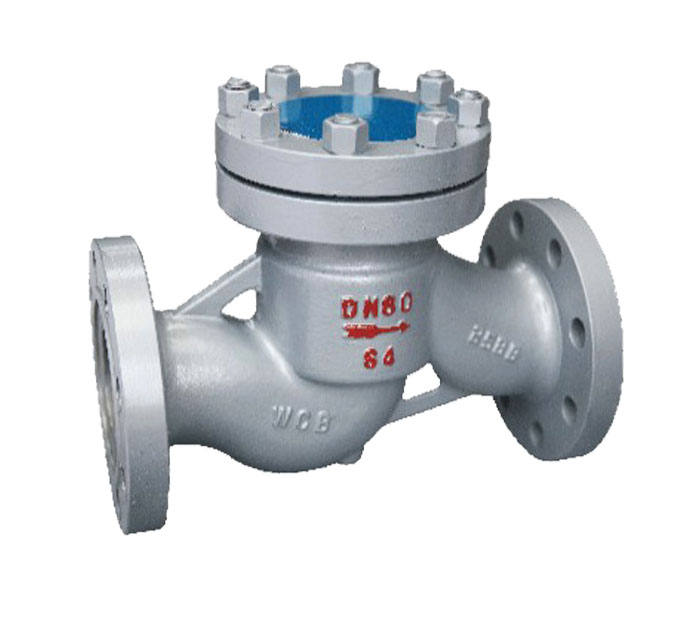
For high-frequency applications, like in radio transmission systems, flanges such as waveguide flanges are employed to ensure seamless energy transfer. These precision-engineered components are designed to minimize reflection losses and maintain the integrity of high-frequency signals. Their importance cannot be underestimated in the context of telecommunications and radar technologies, where signal clarity and strength are paramount.
The industry also recognizes the importance of flange standards, thanks to organizations such as the American Society of Mechanical Engineers (ASME) and the International Organization for Standardization (ISO). Having standardized dimensions and pressure classifications ensures compatibility and interoperability across different equipment and manufacturers. This is vital when sourcing flanges for global projects, as adherence to internationally recognized standards guarantees the flanges will fit and function as intended, irrespective of their origin.
flange
Quality assurance in flange manufacturing is another critical aspect that underscores their reliability. Many manufacturers implement rigorous testing procedures, including non-destructive testing methods such as ultrasonic or radiographic testing. These ensure that each flange meets the high standards necessary for their intended applications, providing peace of mind to engineers and project managers about the long-term performance and safety of their installations.
The advent of digital technologies also plays a role in the flange industry. Advanced simulation software allows engineers to model stress distribution and potential failure points in flange assemblies before physical production. This predictive capability ensures optimal design and helps in foreseeing any issues that could compromise safety or efficiency.
An often-overlooked aspect when discussing flanges is the environmental impact. As industries move towards sustainability, the materials and manufacturing processes for flanges are scrutinized for their ecological footprint. Manufacturers are increasingly looking to reduce waste and energy consumption, adopting greener practices while keeping up with regulatory standards.
For any business involved in systems using flanges, trusting a reputable supplier is a crucial decision. Suppliers not only provide high-quality flanges but also offer expert advice tailored to the specific needs of your project. Their expertise can guide appropriate material selection, flange type, and design specifications, ensuring that the system performs as required and aligns with industry regulations.
In conclusion, while flanges might appear deceptively simple, their role in industrial applications is pivotal. They ensure the safety, reliability, and efficiency of critical systems across various sectors, providing both robust physical connectors and a bridging connection between technological advancement and industrial practice.