In the realm of industrial components, the 2-inch flange is an invaluable asset, commonly used across diverse fields such as plumbing, manufacturing, and construction. Understanding its applications, manufacturing nuances, and material considerations help in leveraging its maximum potential. With over two decades of industry experience, I've witnessed firsthand the transformative impact that choosing the right flange can have on an operation's efficiency and reliability.
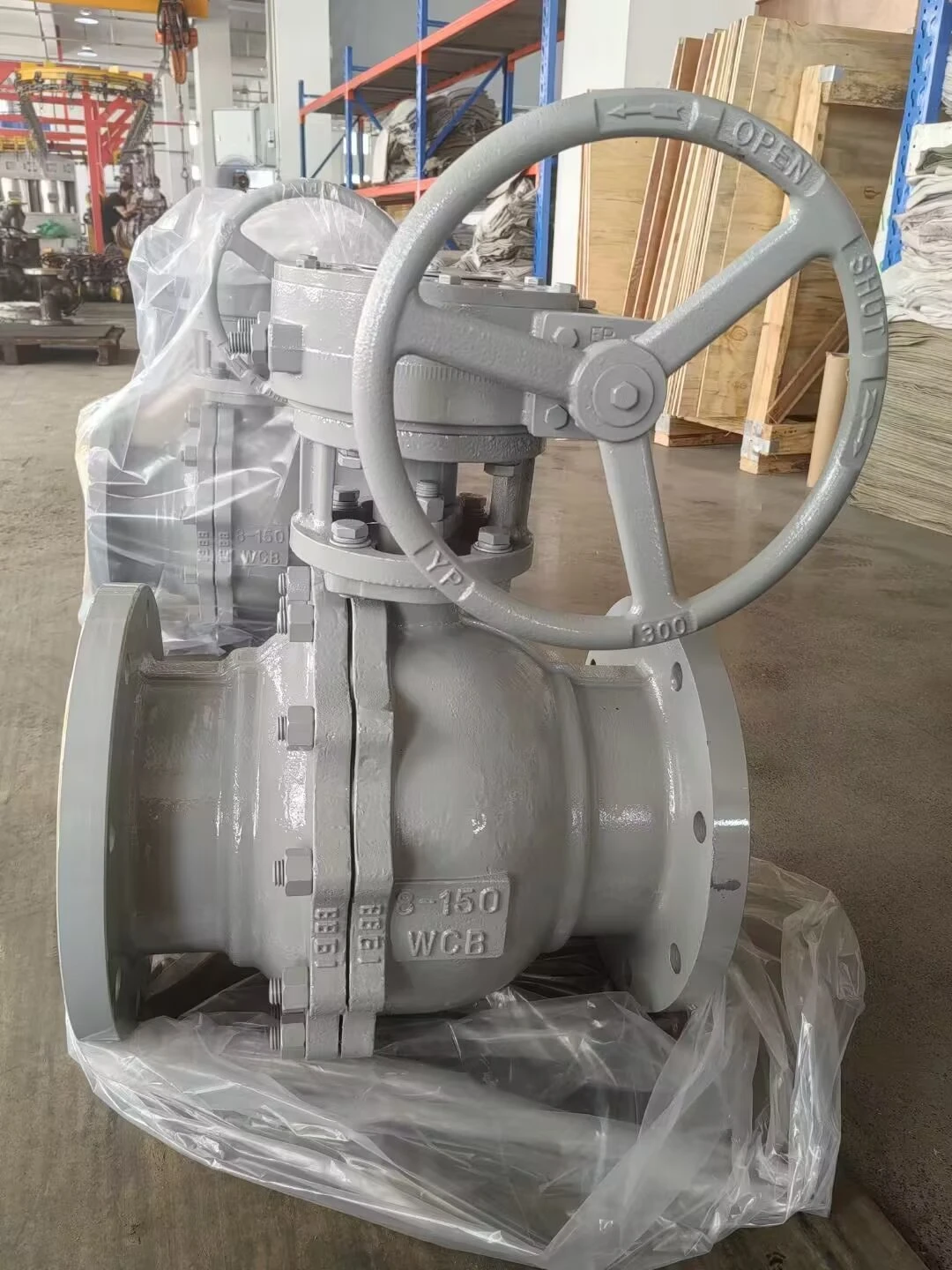
A 2-inch flange, though seemingly simple, is a critical connector used to join pipes, valves, pumps, and other equipment. It creates a secure and robust seal, essential for maintaining the flow of materials and preventing leakage, thus fostering safe and efficient operations. The flange’s size, specifically its 2-inch diameter, signifies its versatile fit for pipes of the same size, ensuring a tight and secure connection.
Expertise in selecting the right flange starts with understanding the operational environment. Environmental conditions such as temperature, pressure, and the type of fluid being transported significantly impact the material choice. Common materials include carbon steel, stainless steel, and PVC, each providing specific advantages. Carbon steel flanges are favored for their strength and durability in high-pressure applications. On the other hand, stainless steel offers excellent resistance to corrosion, making it ideal for transporting corrosive or sanitary materials. PVC flanges, while less durable than their metal counterparts, are cost-effective and resistant to corrosion, suitable for lower-pressure applications.
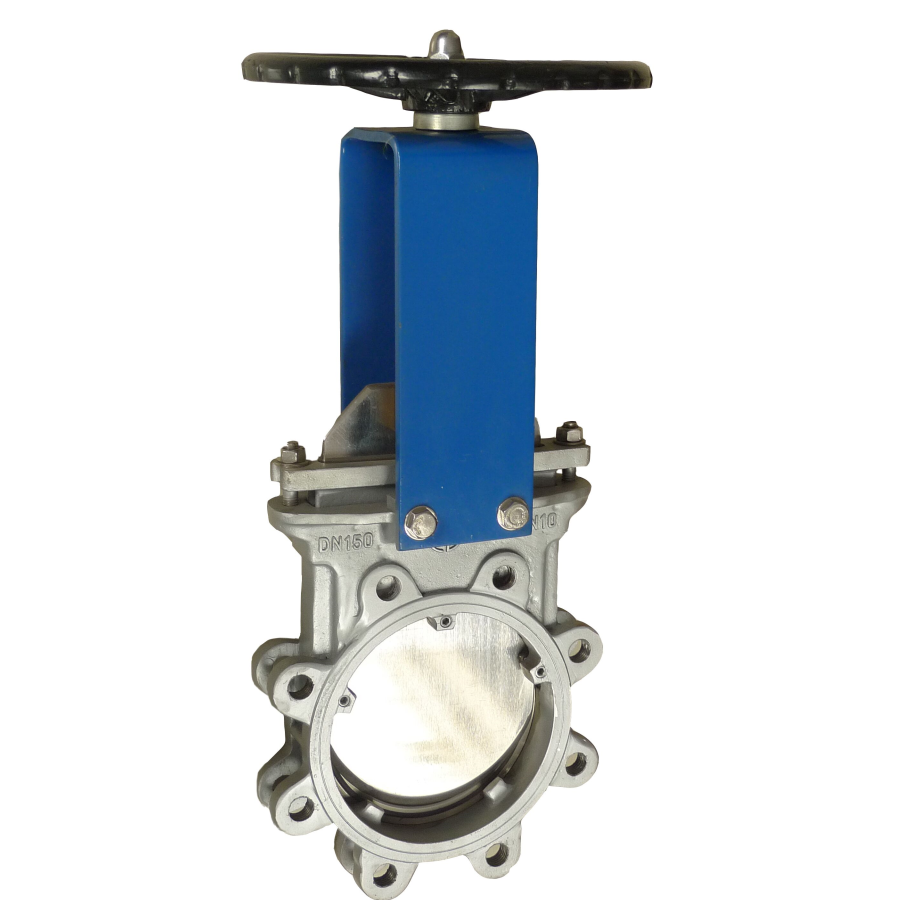
Trustworthy sourcing of flanges is equally paramount. Partnering with established manufacturers that comply with international standards like ASME (The American Society of Mechanical Engineers) ensures components meet strict quality controls, essential for reliability and safety. Certifications and adherence to standards not only guarantee durability but also provide peace of mind regarding the flange's performance under specified conditions.
2 inch flange
From an authoritative positioning, employing best practices in flange installation and maintenance extends the lifespan of the component and the entire system. Proper alignment and torque application during installation prevent unnecessary stress on the flange, reducing the risk of failure. Routine inspections are vital to identify signs of wear, such as corrosion or deformation, early. Implementing a maintenance schedule aligns with the principle of proactive management, minimizing downtime and preventing costly emergency repairs.
Real-world experience underscores the significance of tooling and expertise in the handling of 2-inch flanges. Advanced CNC machining techniques available today permit precise production of flanges, enhancing the seal quality and ensuring compatibility with existing infrastructure. This precision is crucial in systems where even the slightest misalignment can lead to operational inefficiency or safety hazards.
In summary, the 2-inch flange, though a modest component, plays an essential role in industry processes. The judicious selection of material, commitment to quality standards, and adherence to proper installation and maintenance practices underpin its effectiveness. By leveraging these strategies, businesses not only improve operational efficiency but also enhance safety and prolong the lifespan of their systems, demonstrating a holistic approach to industrial management. As the landscape of industrial operations continues to evolve, the 2-inch flange remains a testament to the blend of simplicity and complexity in achieving robust engineering solutions.