Stainless steel gate valves have long been a critical component in various industrial and commercial applications due to their resilience and reliable performance. When selecting the right valve for any pipeline infrastructure, several factors must be considered to ensure optimal effectiveness and safety.
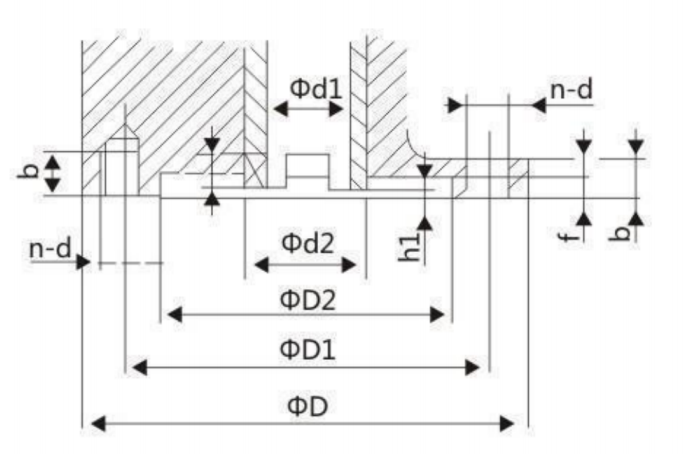
One of the distinguishing attributes of stainless steel gate valves is their remarkable durability. Unlike valves made from other materials, stainless steel valves resist corrosion, which is an indispensable feature for systems exposed to harsh environments and aggressive media. This resistance is primarily due to the chromium content in stainless steel, which forms a passive layer of chromium oxide that prevents further surface corrosion. This makes them particularly suitable in industries such as petrochemical, maritime, and food processing, where exposure to moisture and corrosive substances is unavoidable.
Furthermore, the mechanical properties of stainless steel gate valves are superior. They maintain high tensile strength and hardness, essential for withstanding high pressure and extreme temperatures. This is a crucial consideration for sectors such as oil and gas, where operational conditions can be intensely demanding. The ability to perform well under stress without warping or failing guarantees that systems run smoothly, reducing downtime and maintenance costs.
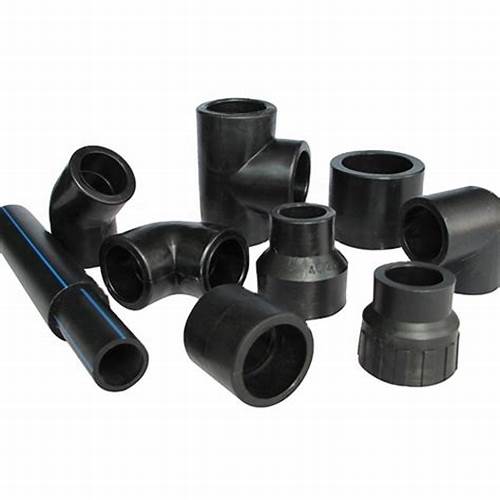
In terms of design, the gate valve is often preferred for their minimal flow resistance when fully opened. This is achieved through a linear motion of the gate to either stop or allow flow, ensuring efficient operation. An often understated benefit is the ability to perform bi-directional sealing, allowing the valve to effectively seal the pressure from both inlet and outlet directions. This functionality is vital in applications where flow direction may vary, thereby enhancing operational flexibility.
Expert opinions reinforce that choosing the correct specification of stainless steel is critical.
Types such as 304 and 316 stainless steel are frequently recommended due to their enhanced chemical resistance. Grade 316, in particular, is favored where salt exposure is prevalent, such as in marine environments, due to the inclusion of molybdenum which further strengthens its anti-corrosive performance.
stainless steel gate valves
From an engineering perspective, it is crucial to consider the method of valve actuation. Options range from manual handwheels to automated systems, such as pneumatic or electric actuators. The choice largely depends on the specific requirements of the application, with automated systems offering advantages in environments where rapid response or remote operation is required.
Reliable manufacturers adhere to rigorous production standards and testing protocols to ensure the highest quality and consistency in their stainless steel gate valves. These standards are pivotal for ensuring the safety and efficiency of industrial operations. A valve from a reputable provider typically comes with complete certification and documentation, which is a testimony to its trustworthiness and compliance with industry norms.
Maintenance is also a critical aspect of stainless steel gate valves. While the material itself provides exceptional reliability, regular checks and maintenance routines are recommended to prolong the lifespan of the valve and prevent unforeseen failures. The simplicity of design in gate valves allows for straightforward maintenance procedures compared to more complex valve types.
In summary, stainless steel gate valves are an excellent investment for various applications, credited not only for their robust performance and longevity but also for their adaptability to different environments and conditions. Choosing valves from trusted manufacturers, understanding the specific material and design requirements, and implementing effective maintenance strategies will ensure sustainable, efficient, and safe operations.