In the modern world of fluid control, the three-way butterfly valve stands out as a revolutionary innovation, offering excellent flexibility, efficiency, and reliability for a variety of applications. What sets this valve apart is its unique design that enables fluid diversion, mixing, or shut-off, making it crucial in industries ranging from chemical processing to water management.
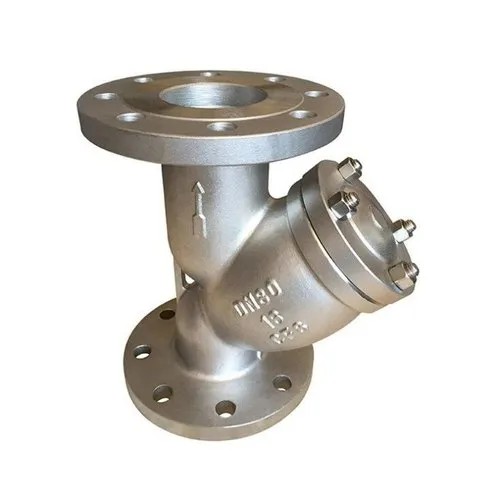
For organizations seeking to optimize their fluid control systems, understanding the intricacies of three-way butterfly valves is imperative. Unlike traditional two-way valves that simply open and close, the three-way butterfly valve facilitates the direction of flow in multiple paths, thus maximizing operational efficiency and minimizing downtime. This capability makes it an ideal choice for complex piping networks where flow needs to be redirected without interrupting the overall system.
The construction of a high-quality three-way butterfly valve is a testament to engineering excellence. Typically, these valves comprise a circular disc or vane with two to three ports, depending on the specific configuration needed for the application. The disc is mounted on a rotating shaft, which can be actuated manually or automatically. The material selection for these components is critical, as it directly influences the valve’s durability and performance. Common materials include stainless steel, which offers excellent corrosion resistance, and high-performance plastics for cost-effective applications.
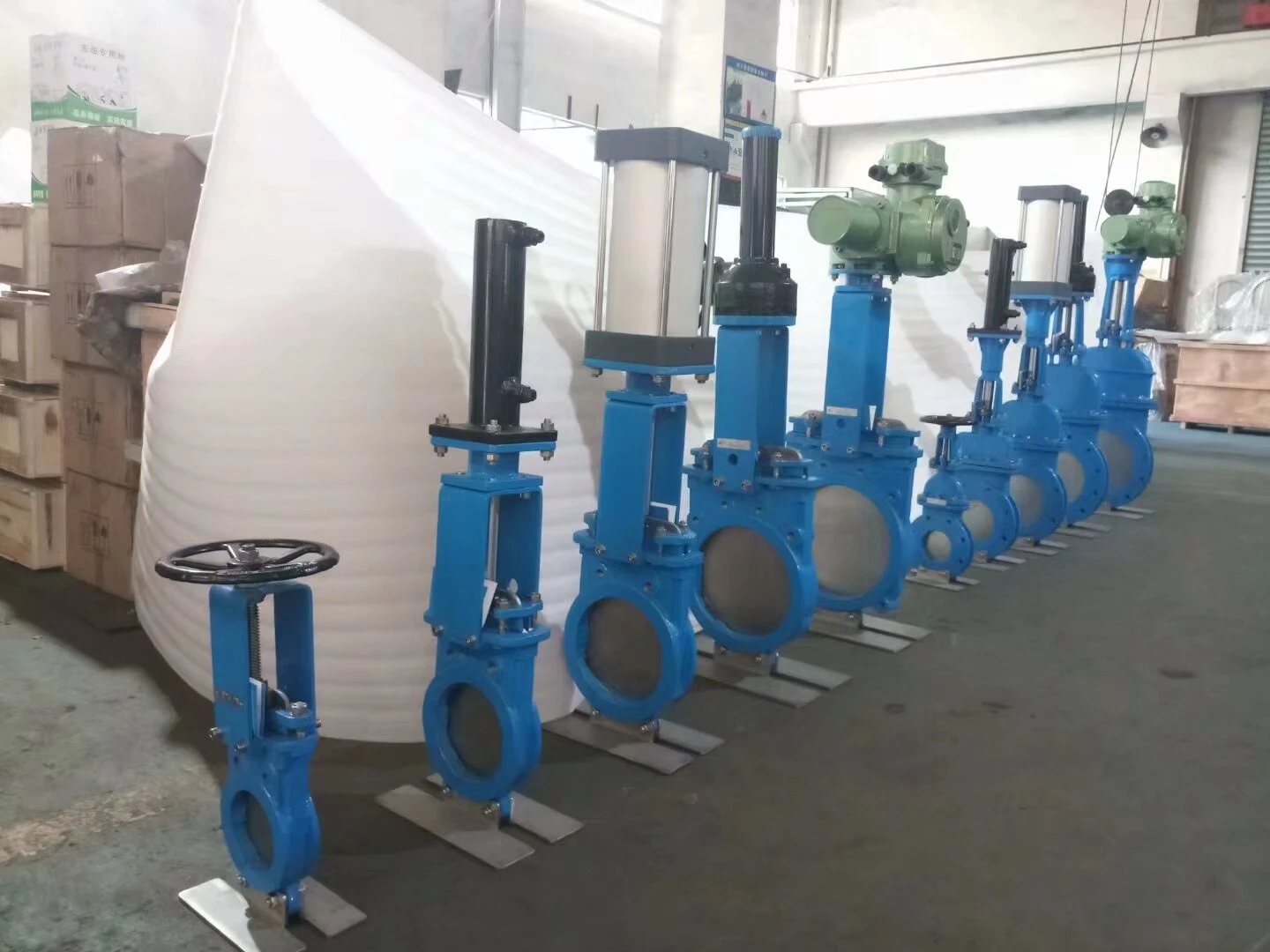
From an expert perspective, when assessing a three-way butterfly valve, one must consider factors such as pressure ratings, temperature ranges, and material compatibility with the fluid to ensure longevity and reliability. It's essential for engineers to conduct a thorough analysis of the system requirements and select a valve that meets both the operational needs and regulatory standards.
In the realm of authority, major manufacturers of three-way butterfly valves have contributed extensively to the standardization of valve design and performance benchmarks. Organizations like the American National Standards Institute (ANSI) and the International Organization for Standardization (ISO) have established guidelines that ensure the interoperability and safety of these systems. As a result, purchasers can trust that valves meeting these standards will deliver reliable performance in their intended applications.
3 way butterfly valve
Trustworthiness in the context of three-way butterfly valves is about assurance that the valve will perform as expected over its service life. Manufacturers often provide detailed documentation, warranties, and technical support to reinforce this trust. End-users are encouraged to review these resources carefully and engage directly with manufacturers or certified distributors to verify certifications and compliance with industry standards.
The experience of installing and operating a three-way butterfly valve can vary significantly based on the complexity of the system and the specific requirements of the application. Installation typically involves aligning the valve with the existing piping system, ensuring a proper seal, and integrating the actuation system if automation is desired. Users have reported that the simplicity of the butterfly valve design often results in quicker installation times compared to more traditional valve systems.
Operationally, three-way butterfly valves are praised for their low maintenance requirements and energy efficiency. Their streamlined structure minimizes flow resistance, resulting in lower energy consumption for fluid transport. Regular maintenance checks, however, remain essential to identify potential wear and tear, particularly in high-pressure or high-temperature scenarios.
In conclusion, the three-way butterfly valve is a strategic component in modern fluid control systems, offering unparalleled flexibility and performance. Its design reflects a synthesis of engineering prowess and material science, ensuring that it can meet the high demands of contemporary industry. As technology continues to advance, the integration of smart sensors and automation in these valves is anticipated to further enhance their capabilities, offering even greater precision and control in fluid management.