Cryogenic check valves are an essential component in the intricate ecosystem of industrial and laboratory applications dealing with extremely low temperatures. The need for reliability and precision in cryogenic processes cannot be overstated, given their vital role in sectors such as aerospace, medical, chemical, and energy industries.
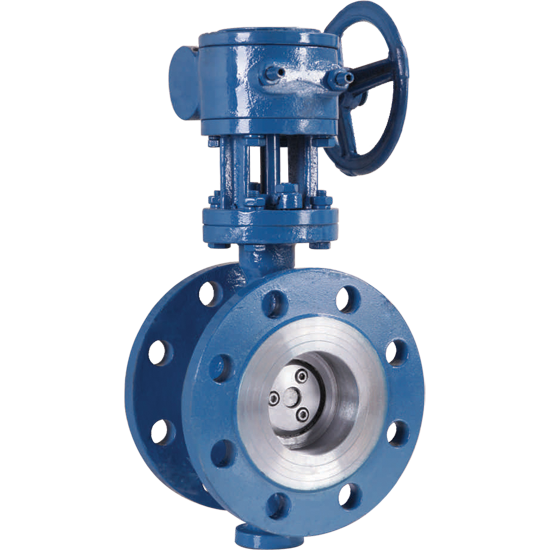
Understanding the critical role of cryogenic check valves begins with their fundamental design and purpose, which is to allow fluid to flow in one direction and prevent backflow, all while withstanding temperatures that can plunge below -150 degrees Celsius. This unique functionality positions them as vital gatekeepers in cryogenic systems, ensuring the safety and efficiency of operations under extreme conditions.
Experience in dealing with cryogenic check valves reveals a landscape of diverse applications where these components excel. In the field of liquid natural gas (LNG), for instance, cryogenic check valves are deployed to manage the flow and containment of LNG, preventing gas escape which could lead to catastrophic failures. Similarly, in space exploration, where every component must operate flawlessly in the void, these valves ensure the stable operation of propulsion systems carrying cryogenic fuels.
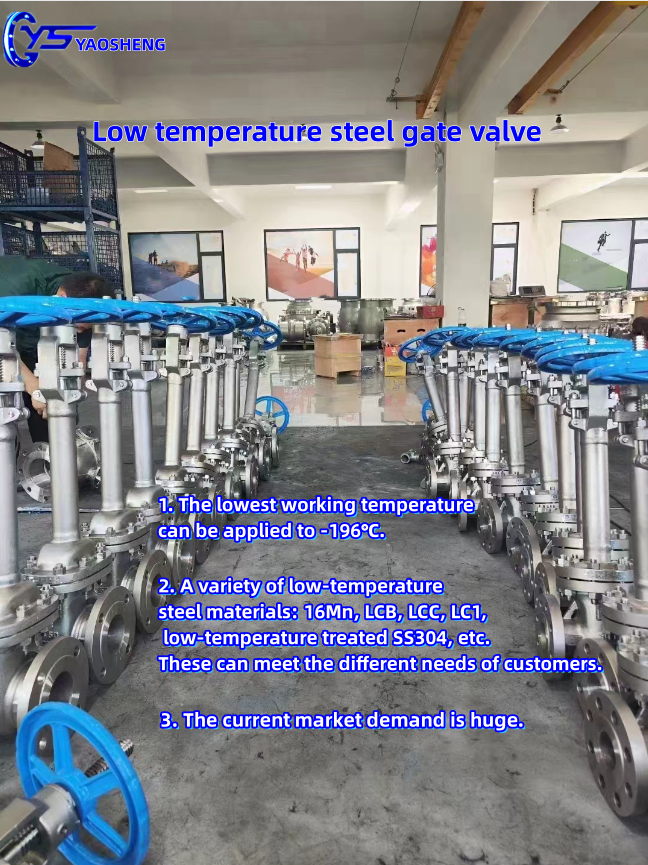
Expertise in selecting the right cryogenic check valve involves a keen understanding of materials and design specifications best suited for low temperature environments. The choice of materials, typically stainless steel or specialized alloys, helps maintain integrity and performance at cryogenic temperatures. Moreover, valve design often incorporates advanced sealing technology to resist freezing and to maintain its function over prolonged periods.
cryogenic check valves
Assessing the authoritativeness of cryogenic check valve manufacturers involves examining certifications and compliance standards like the American Society of Mechanical Engineers (ASME) and the European Committee for Standardization (CEN). Manufacturers adhering to these standards demonstrate a commitment to quality and safety, which is essential in high-stakes applications. Reference to successful case studies wherein manufacturers’ valves have effectively functioned in challenging projects further reinforces these manufacturers’ standings.
Trustworthiness in cryogenic check valve manufacturing is further established through rigorous testing and quality assurance practices. High-end manufacturers often engage third-party testing to validate their products' resilience under simulated operational conditions. This transparency provides end-users with confidence in the valve’s ability to handle precise and demanding applications.
The integration of technology and innovation in cryogenic check valve design has also shaped the landscape, with features such as enhanced sealing technologies and rapid closure mechanisms which address operational delays and improve safety. Real-world experiences have shown that investing in technologically advanced valves can reduce maintenance costs and extend operational life, a crucial consideration for industries with continuous processes.
In conclusion, the world of cryogenic check valves is characterized by the necessity for precision, reliability, and robust design. The ability of these valves to perform under some of the universe's most extreme conditions makes them invaluable to industrial processes requiring strict safety and efficiency standards. For end-users, partnering with reputable manufacturers that adhere to international standards and demonstrate a proven track record of innovation and reliability is fundamental to achieving desired outcomes in applications involving cryogenic technologies.