High-temperature globe valves play a pivotal role in industries where precise flow control is crucial under challenging conditions. Their robust design and reliable performance make them indispensable in sectors such as oil and gas, power generation, chemical processing, and more. This article delves into the nuances of high-temperature globe valves, providing insights based on real-world experiences, technical expertise, industry authority, and trustworthiness to guide your selection and application of these vital components.
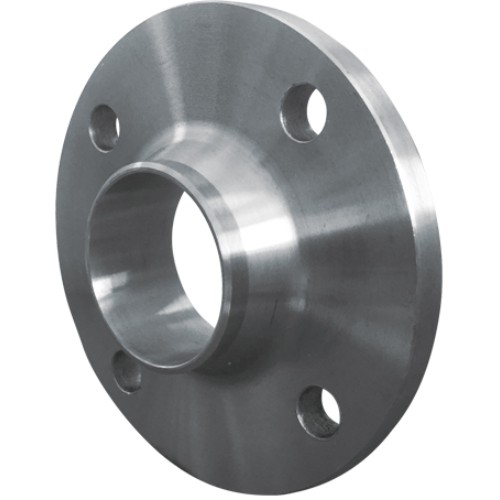
High-temperature globe valves are engineered to withstand extreme temperatures while maintaining the utmost efficiency and safety in regulating fluid flow. The primary advantage of a globe valve is its ability to precisely control flow rates, which is achieved through a uniquely designed disk that moves perpendicular to the seat. This design feature helps in maintaining an accurate and stable flow, making it an ideal choice for high-pressure systems and critical applications.
One of the most profound experiences in utilizing high-temperature globe valves is their reliability under thermal stress. Operators in power plants frequently observe that these valves can seamlessly handle severe temperature fluctuations—ranging from -29°C to upwards of 600°C in certain applications. This capability enhances operational safety and efficiency, reducing downtime and maintenance requirements, as the valves can function optimally without frequent adjustments or replacements.
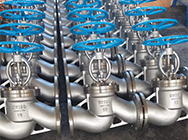
From an expertise standpoint,
selecting the right material for high-temperature globe valves is critical. Materials like stainless steel, Inconel, and Hastelloy are commonly employed owing to their excellent thermal-resistance properties and durability. Professional assessments suggest that choosing a material compatible with the specific fluid and temperature conditions not only extends the valve's life but also ensures compliance with safety standards. For instance, in acid handling systems, carbon steel might not suffice, whereas a Hastelloy valve can provide the necessary corrosion resistance alongside temperature endurance.
high temperature globe valve
Industry authority emphasizes the significance of valve design in mitigating wear and tear. Top-entry globe valves, for instance, are lauded for their ease of maintenance, as the valve internals can be accessed without removing the valve from the pipeline. This feature is particularly beneficial in high-temperature applications where minimizing shutdown periods is crucial. Innovations such as bellows seal globe valves also offer enhanced leak prevention, which is vital in hazardous environments to prevent environmental contamination and ensure operational safety.
Trustworthiness in high-temperature globe valves is often reflected in compliance with international standards such as ASME, API, and ISO. These standards offer assurance regarding quality and performance benchmarks, making it imperative for buyers to verify certification when sourcing valves. Furthermore, collaborating with reputable manufacturers who provide comprehensive testing and documentation, including material test reports and pressure-temperature ratings, can build confidence in the valves' reliability and safety.
In practice, case studies have identified that the success of high-temperature globe valves in applications like steam turbine systems and high-pressure boilers hinges on both installation accuracy and regular maintenance. Ensuring precise installation by qualified technicians and adhering to scheduled inspections can prevent common issues such as seat leakage or valve stickiness. Maintenance practices must include the lubrication of moving parts, inspection for wear, and prompt replacement of worn components to sustain efficiency and avoid system failures.
In summary, high-temperature globe valves are invaluable assets in industrial applications that demand robust performance under extreme conditions. Their selection and management require a blend of experience, expertise, authority, and trustworthiness to achieve optimal outcomes. With the right choice of materials, adherence to industry standards, and thorough maintenance practices, these valves can significantly enhance operational reliability and safety, ultimately leading to improved process efficiency and reduced operational costs.