In industrial applications, the reliability of components is of utmost importance. One such critical component is the sealing flange, a fundamental part that ensures leak-proof connections in piping systems. From the oil and gas industry to pharmaceuticals and beyond, sealing flanges play a pivotal role.
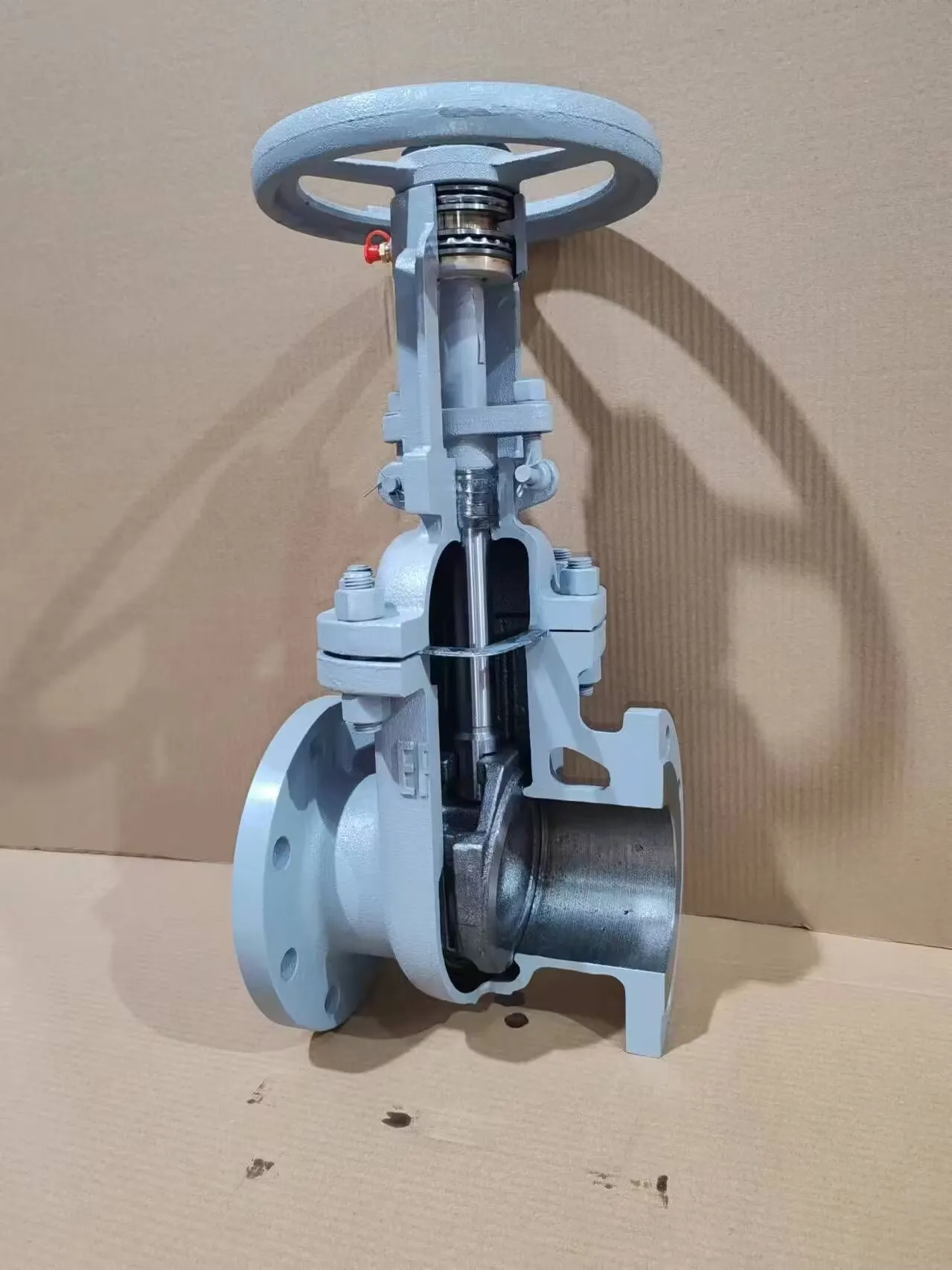
Experienced engineers recognize that the right selection of sealing flanges can make a significant difference in operational efficiency. The choice involves material compatibility, temperature, and pressure conditions. Industries have strict compliance standards that these flanges must adhere to, ensuring safety and performance.
Sealing flanges come in various designs, such as welding neck, slip-on, socket weld, and blind flanges. Each type serves a specific purpose. For example, welding neck flanges are perfect for high-pressure situations due to their long tapered hub, which provides strength and reduces stress. Choosing the wrong type can result in catastrophic failures, making expertise in flange selection crucial.
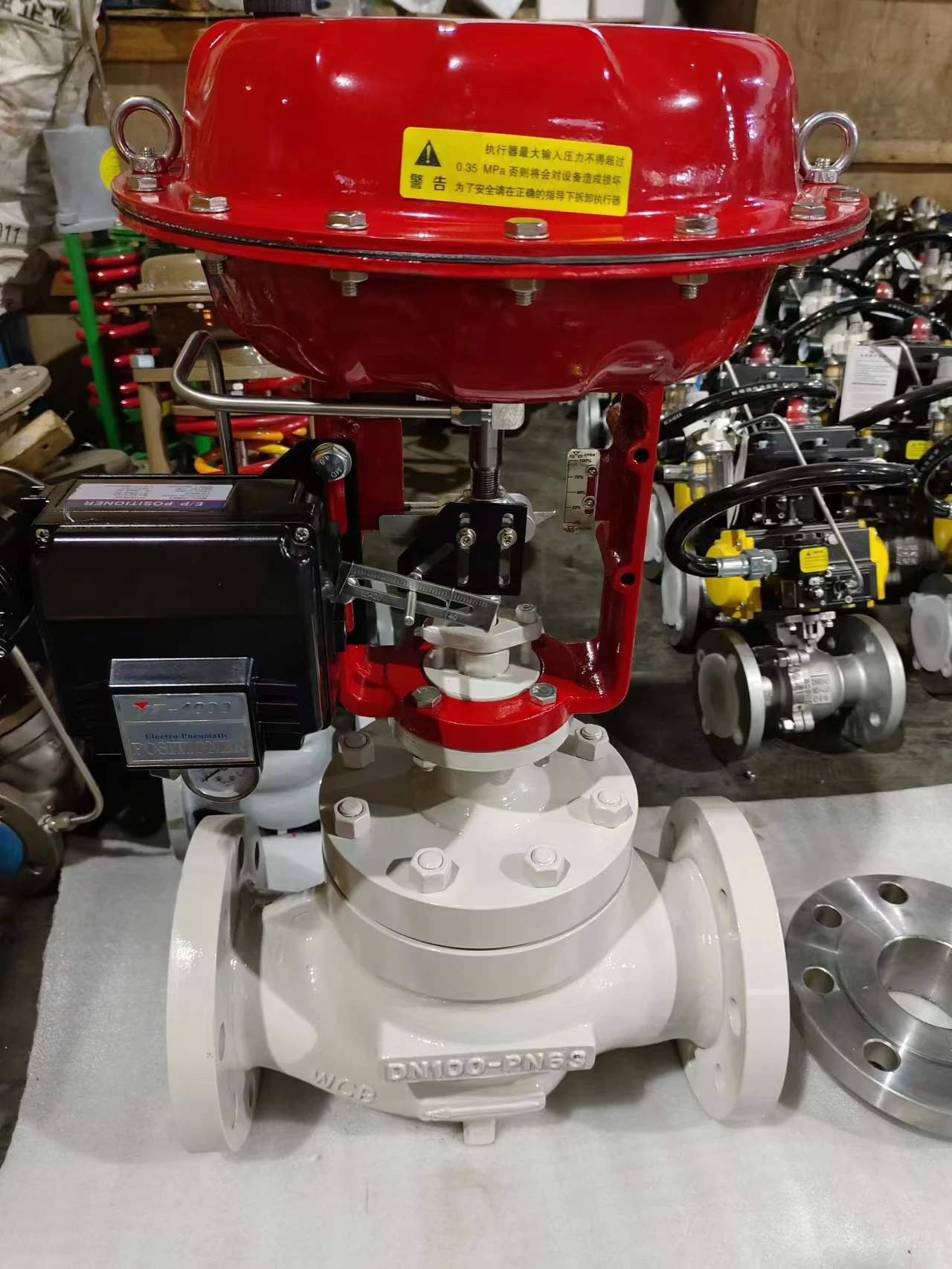
Material choice also significantly affects the performance of a sealing flange. Options range from carbon steel and stainless steel to more exotic alloys like Inconel or Monel, each offering different benefits. Stainless steel is favored for its corrosion resistance, while carbon steel offers strength and affordability for less demanding applications. The selection of the appropriate material requires a thorough understanding of the environmental conditions and the media being transported through the pipes.
Authoritative sources in the industry underscore the necessity of regular maintenance and inspection of sealing flanges. Even the most robust materials can degrade over time due to environmental factors, leading to potential leaks. A reliable maintenance protocol involves regular torque checks on bolts and inspections for signs of wear or corrosion. Neglecting these procedures can lead to operational disruptions and financial losses.
sealing flange
Moreover, advancements in sealing technology are leading to more reliable sealing solutions. Enhanced gasket materials, such as PTFE or expanded graphite, offer superior resilience against a range of temperatures and pressures. These innovations, coupled with precise installation techniques, improve the sealing integrity, thereby extending the lifespan of flanges.
Trustworthiness in sealing flange performance also comes from reputable manufacturers who adhere to stringent manufacturing standards and testing protocols. Many manufacturers align with international standards such as ASME, ASTM, or DIN, providing assurance of quality and compatibility in global markets. When selecting a vendor, verifying compliance with such standards is an essential step to ensure long-term trust in the product's performance.
Another facet of trustworthiness is the traceability of flange materials. Documentation such as material test reports (MTRs) provides insights into the material properties and assures that the flanges meet the required specifications. This traceability is particularly vital in industries where any deviation from the standard could have severe repercussions.
In conclusion, the selection and maintenance of sealing flanges demand a comprehensive understanding of both the technical aspects and the operational context. Industry experts and authoritative bodies continually emphasize the importance of choosing the right type, material, and manufacturer to optimize both safety and efficiency. As industries move towards more complex and demanding environments, the role of sealing flanges becomes even more critical, solidifying their place as indispensable components in modern industrial applications.