Forged flanges, a crucial component in piping systems, have gained prominence due to their superior mechanical properties, durability, and reliability. In industries where safety and efficiency are paramount, such as oil and gas, petrochemicals, and water treatment, choosing high-quality forged flanges is non-negotiable. This article delves into the unique benefits and applications of forged flanges, backed by industry expertise and real-world experiences that enhance their credibility and trustworthiness.
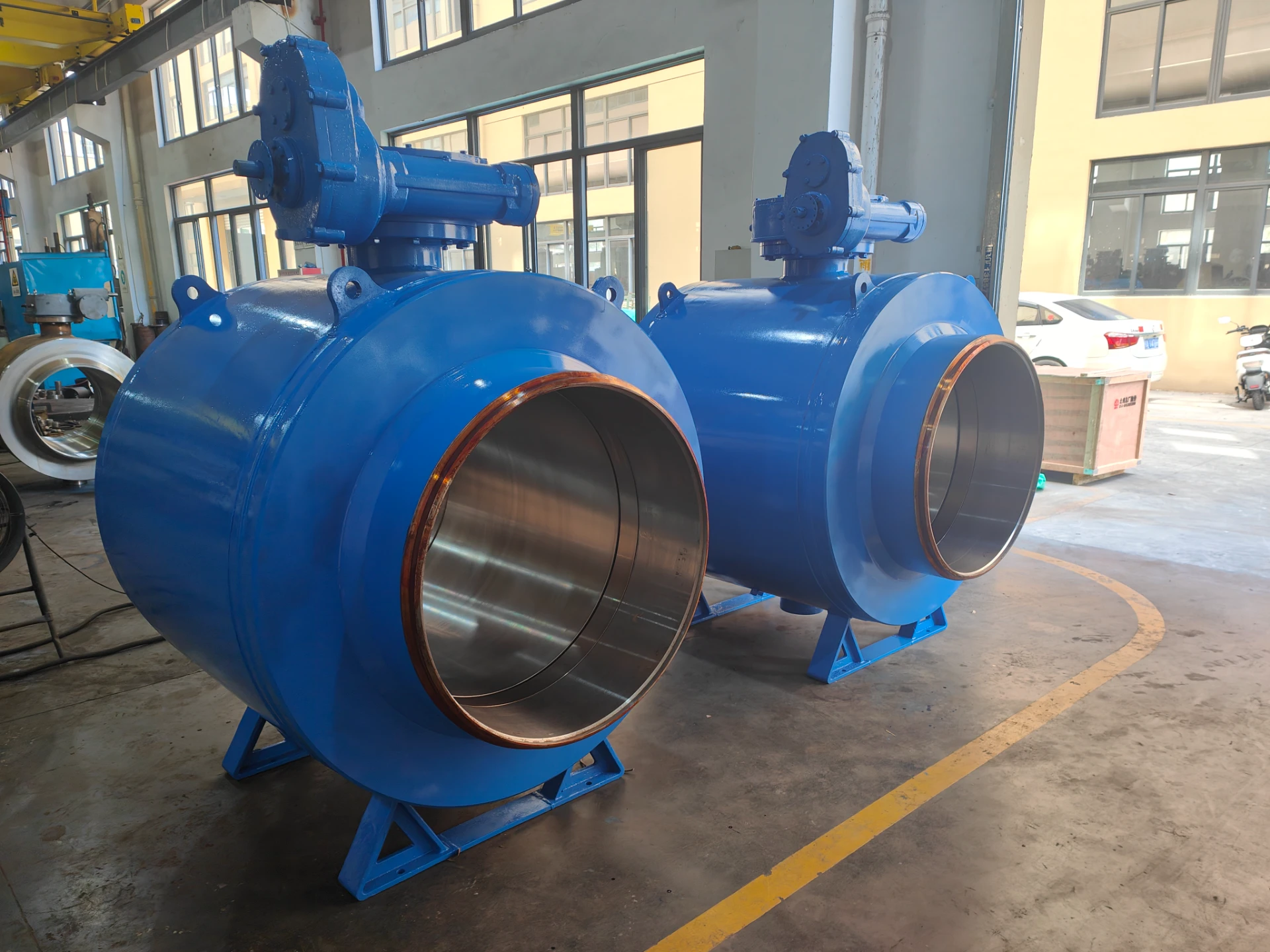
In the manufacturing realm, forged flanges stand out due to their method of production. Unlike cast flanges, which are poured into molds, forged flanges are created by physically shaping metals using compressive forces. This process aligns the grain flow in the metal, significantly increasing the component's strength and resistance to fatigue. It's this detailed crafting process that imbues forged flanges with their unparalleled durability and resilience, essential for high-pressure environments and critical system applications.
A specific experience from the oil and gas sector perfectly illustrates the reliability of forged flanges. During a project involving deep-sea oil exploration, a leading multinational faced extreme conditions where traditional flanges frequently failed due to pressure variations and corrosive environments. Upon integrating forged flanges into their systems, the company noticed a marked improvement in system reliability, which not only reduced downtime but also enhanced safety measures for field operators. This shift underscores the trust that industry leaders place in forged flanges when faced with challenging conditions.
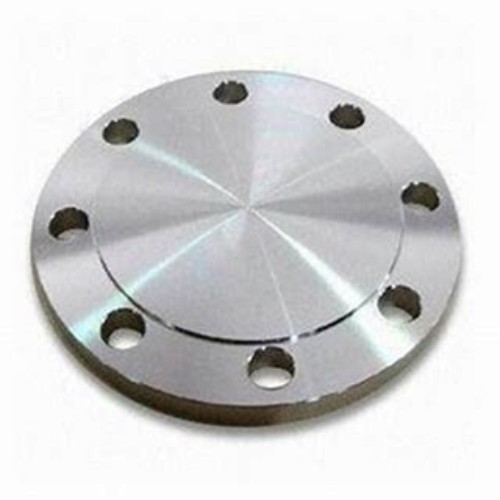
From an expertise standpoint, engineers and industry specialists advocate for forged flanges due to their adaptability to stringent specifications and standards. These components can be tailored to meet specific regulatory requirements, making them a preferred choice in sectors with rigorous safety and compliance demands. For instance, in nuclear facilities where operational integrity is of the utmost importance, forged flanges' consistency and strength ensure that the piping systems maintain their integrity over extended periods.
forged flanges
In addition to their mechanical advantages, the diversity of forged flanges in terms of shapes and sizes also adds to their appeal. Whether it's slip-on, blind, weld neck, or threaded designs, the options are expansive, catering to a variety of industrial applications. A case study involving a chemical processing plant highlighted how the implementation of different types of forged flanges throughout their piping networks significantly streamlined maintenance tasks, reducing wear and tear and ultimately optimizing overall plant performance. This adaptability showcases the expert design and engineering that goes into the fabrication of forged flanges.
Authoritativeness is further established by the compliance of forged flanges with international standards like ASME, ASTM, and DIN. These accreditations are not mere formalities but rather a testament to their quality, performance, and global acceptance. Manufacturers are constantly investing in cutting-edge technology and techniques, such as 3D simulation and testing modules, which enhance the precision and reliability of forged flanges, ensuring they meet the high standards required by international bodies.
Trustworthiness in the use of forged flanges is also developed through their environmentally friendly production process. The forging process typically requires fewer materials and results in less waste compared to alternatives, reducing the carbon footprint and aligning with sustainable business practices. Furthermore, ongoing research and development in metallurgical sciences promise even greater advancements in the production of forged flanges, with potential breakthroughs in materials that could further enhance their performance and environmental compatibility.
In conclusion, forged flanges offer a blend of strength, customizability, and compliance that ensures their continued prominence in industrial applications. Their proven track record across various sectors, compliance with rigorous international standards, and environmentally conscious production methods collectively reinforce their reputation as a trustworthy solution. Industry professionals seeking durability, reliability, and adherence to regulatory standards will find that forged flanges are not just a choice but rather an essential component in fostering safe and efficient industrial operations.