Forged flanges represent a crucial component in the construction and manufacturing sectors for their central role in connecting pipes, valves, pumps, and other equipment. Their importance is underscored by a blend of rigorous engineering expertise and the necessity for impeccable reliability in high-stakes applications. This article delves into the unique advantages, profound expertise, and trustworthiness that forged flanges bring to critical industries.
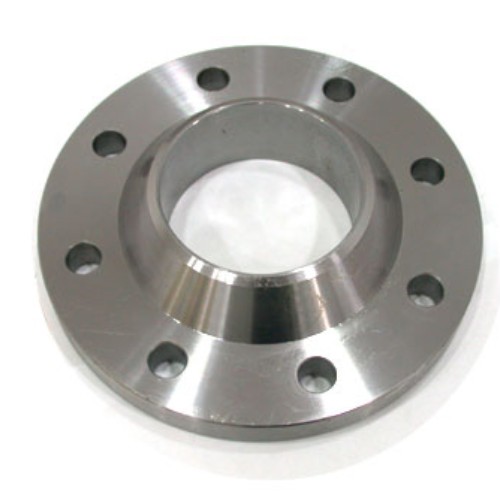
Forged flanges are developed through a robust process of heating and forming metal, typically carbon steel, alloy steel, or stainless steel, into a solid connectable structure. This process enhances the metal's mechanical properties, including tensile strength, fatigue resistance, and impact tolerance, ensuring durability in demanding environments. The superior grain structure obtained through forging makes these flanges exceptionally reliable across varied pressures and temperatures.
One of the key advantages of using forged flanges is their ability to withstand high stress and pressure conditions without deformation. This capability is essential in industries such as oil and gas, petrochemicals, and power generation, where system failures could have catastrophic consequences. A profound understanding of material science and engineering principles is vital in the production of forged flanges, affirming the relevance of expertise in their manufacture.
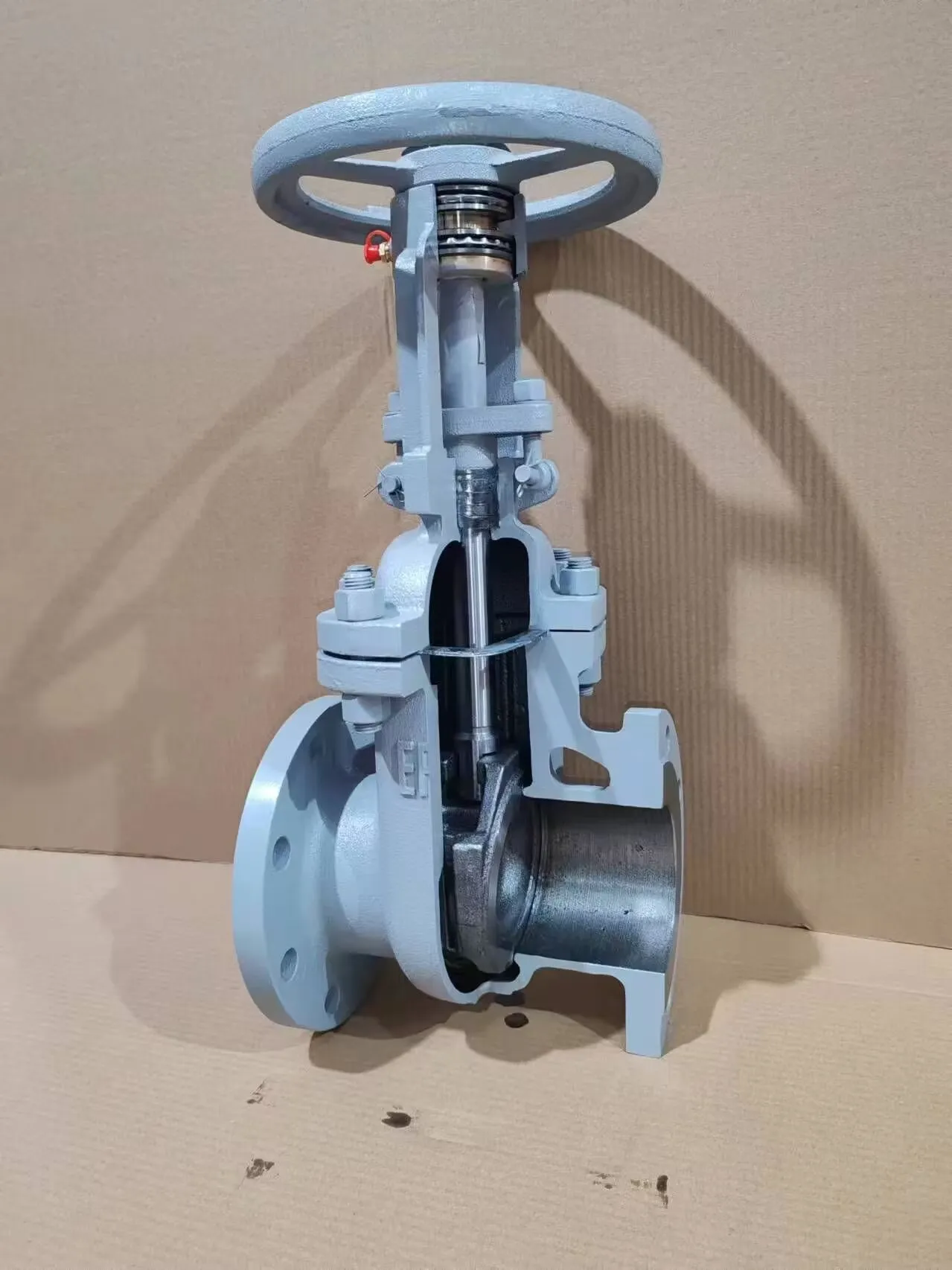
Professionally, manufacturers of forged flanges possess an authoritative stance due to their advanced technical processes and quality assurance measures. Standard procedures often involve meticulous material selection, precise forging techniques, and rigorous testing to comply with international standards like ASME, ANSI, and DIN. The insistence on such standards speaks to the authority and reliability these manufacturers command in the global market.
Beyond technical specifications, the trustworthiness of forged flange producers is rooted in their commitment to quality and performance consistency. Companies with ISO certifications and extensive field testing of their products are seen as vanguards in the industry, providing customers with the confidence that their flanges will operate flawlessly in their specified applications. This trust is reinforced through long-term partnerships with clients, building on a history of performance and dependability.
forged flange
Experience is a critical component of operational competence in the forged flange sector. Historical data and case studies often point to instances where the successful deployment of forged flanges mitigated risks and enabled robust performance under extreme conditions. This accumulated experience transcends mere product knowledge, incorporating lessons learned from diverse industrial applications and continuously refined manufacturing techniques.
Specialization within this domain often involves tailoring products to specific industrial needs, showcasing a deep understanding of customer requirements and industry dynamics. Expertise in custom forging allows manufacturers to offer solutions that are meticulously aligned with precise specifications, further enhancing their authority as industry leaders.
The incorporation of innovative technologies in the forging process is indicative of a progressive and farsighted approach. Advanced simulation software, modern Quality Control (QC) methodologies, and automated technologies are increasingly prevalent, allowing manufacturers to push the boundaries of what is possible in flange design and production. Such advancements contribute significantly to the enhanced experience, expertise, and trustworthiness of forged flange producers.
A critical consideration in the flange manufacturing sector is environmental responsibility. Leading companies are implementing sustainable practices, such as optimizing material use and energy-efficient forging processes, which reflects their commitment to environmental stewardship. This aspect not only meets regulatory requirements but also earns the trust of environmentally-conscious clients, further reinforcing the credibility of reputed manufacturers.
In conclusion, forged flanges stand as a testament to engineering excellence, underlined by a synergy of experience, expertise, authority, and trust. Their manufacturing processes are as demanding as the applications they serve, necessitating an unwavering focus on quality and innovation. As industries continue to evolve, the role of forged flanges remains pivotal, driven by their unmatched reliability and the steadfast commitment of those who produce them. Manufacturers that embody these principles solidify their position at the forefront of the sector, ensuring the safety and efficiency of critical infrastructure worldwide.