In the world of industrial applications, the DN50 flange stands out as a crucial component for constructing reliable and scalable piping systems. Its designation, 'DN50,' signifies a nominal diameter of 50 millimeters, aligning with the international metric standard that ensures wide acceptance across various industries around the globe. This article delves into the intricacies of DN50 flanges, exploring their types, applications, and what makes them an indispensable component in pipeline infrastructure.
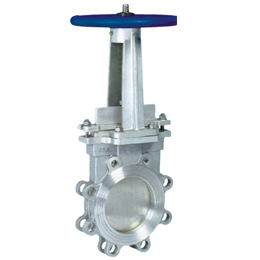
First and foremost, the DN50 flange is integral to the seamless connection of pipes, valves, pumps, and other equipment crucial for moving fluids within a system. These flanges create a secure bond, ensuring the systems remain leak-proof under significant pressure. The integrity of such connections is paramount, impacting not only the efficiency of operations but also the overall safety standards on site. It’s no surprise that in critical industries such as petrochemical, wastewater management, and food processing, the DN50 flange is a ubiquitous presence.
Various types of DN50 flanges are available on the market, each designed to address specific operational needs and constraints. Among the most common are the welding neck, slip-on, and lap joint flanges. Welding neck flanges, for instance, are renowned for their high-stress performance and are often employed in high-pressure environments. They offer a smooth transition of stress from the flange to the pipe, which is crucial in reducing the risk of failure when under load. Slip-on flanges, which are simple to install and align, are typically used in systems where pressure conditions are less demanding. The adaptability of lap joint flanges, often used with stub end fittings, makes them particularly suitable for applications requiring quick assembly or disassembly.
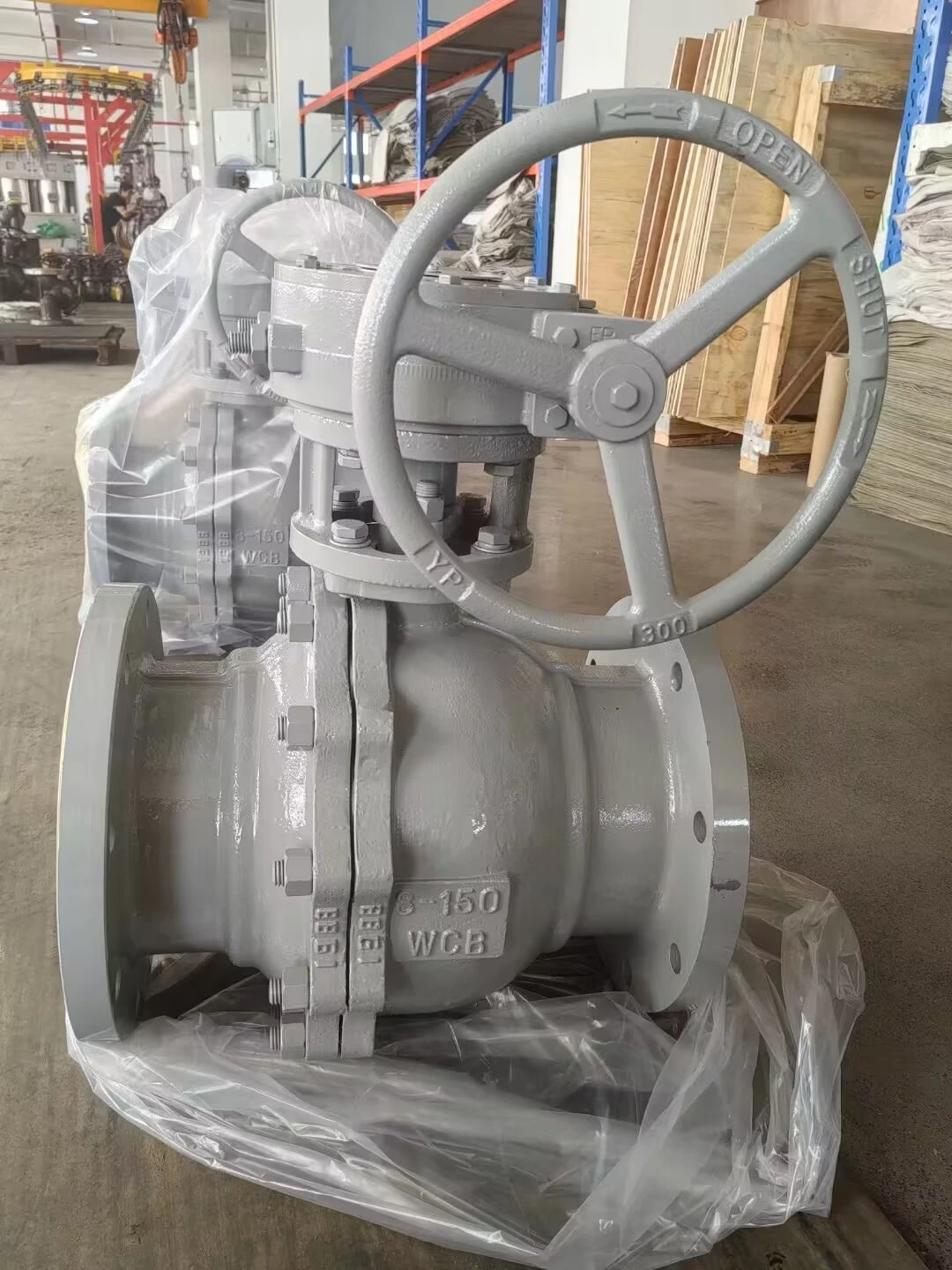
The material composition of DN50 flanges is yet another critical feature that dictates their suitability for various applications. Carbon steel, stainless steel, and alloy steel are among the common materials used in their construction. Stainless steel DN50 flanges, for example, are highly revered for their corrosion resistance, making them ideal for environments exposed to moisture and corrosive elements. Engineers often opt for carbon steel for its strength and cost-effectiveness in applications where corrosion resistance is not a primary concern. Alloy steel options provide a middle ground, offering enhanced mechanical properties and resistance that can be crucial in specialized industrial settings.
dn50 flange
From an expert’s perspective, selecting the right DN50 flange goes beyond understanding types and materials. It's crucial to consider the specific environmental conditions they will be exposed to, factoring in temperature ranges, the chemical makeup of the fluids transported, and external environmental conditions, such as potential exposure to pollutants. Moreover, compliance with industry standards such as ASME, ANSI, and ISO is non-negotiable to ensure that the flanges provide a reliable service life and meet safety standards.
Professionals emphasize the importance of regular maintenance and inspection of DN50 flanges. While made from robust materials, these components require periodic checks to identify signs of wear and tear, corrosion, or any deviations that might lead to system inefficiencies or failures. The implementation of a comprehensive maintenance program can extend the lifespan of these flanges and ensure optimal performance throughout their service.
Developing a deep understanding of DN50 flanges emphasizes not only technical specifications but also real-world applications and experiences. Field experts and engineers who have worked extensively with flanges often share insights that can greatly aid in the selection and management of these components, underscoring their expertise and solidifying best practices within the industry.
In conclusion, DN50 flanges serve as a backbone in industrial piping systems, offering flexibility, strength, and reliability that is hard to match. Their versatility in conjunction with a wide array of materials and designs provides industries with tailored solutions that enhance operation efficiency and safety. Embracing best practices when selecting and maintaining these flanges not only ensures compliance and operational excellence but also fortifies trust in the systems that drive today’s essential industries. As technology and materials science advance, the DN50 flange will continue to evolve, adapting to new challenges and demands while maintaining its critical role in industrial applications worldwide.