High pressure pipe fittings are integral components in numerous industries, ensuring the safe and efficient transport of fluids and gases under elevated pressures. These specialized fittings are engineered to withstand extreme conditions, making them essential for maintaining the integrity and performance of piping systems. Let's delve into the critical aspects that underline the importance, expertise, authority, and trustworthiness of high pressure pipe fittings in diverse applications.
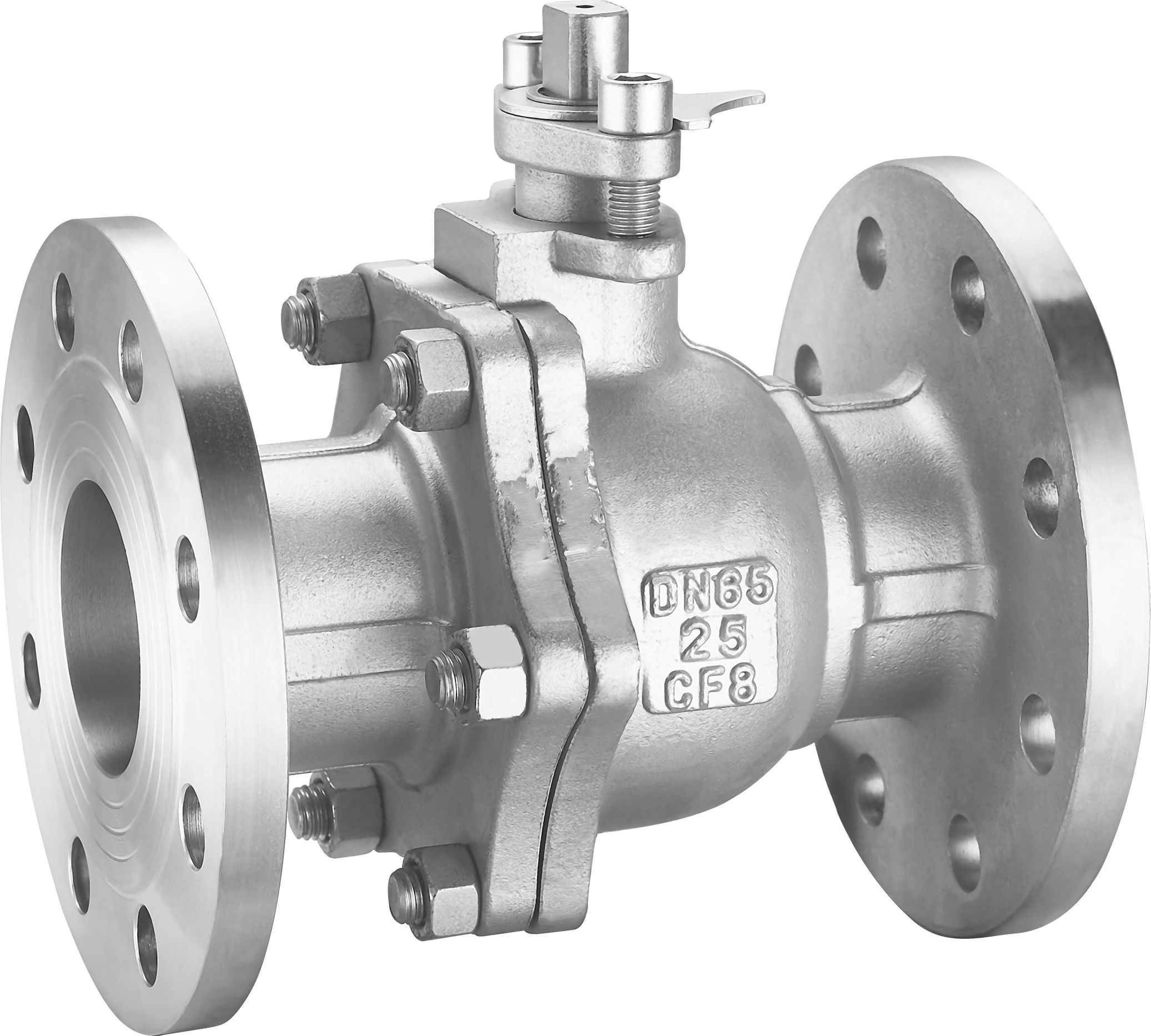
High pressure pipe fittings, crafted from robust materials like stainless steel, carbon steel, and alloys, are designed to handle pressures that typically range from 700 to 6000 psi and beyond. The ability to sustain such pressures makes them indispensable in industries such as oil and gas, petrochemical, power generation, and pharmaceuticals. Their reliability in harsh and demanding environments underscores their necessary role in global infrastructure.
A key experience underpinning the use of high pressure fittings is their critical role in preventing leaks and system failures. In the oil and gas industry, for example, these fittings are used in drilling operations, refineries, and transportation pipelines. The consequences of failure in these settings can be catastrophic, resulting in environmental damage, financial loss, and jeopardizing human safety. Hence, the selection of high-quality,
certified fittings is paramount.
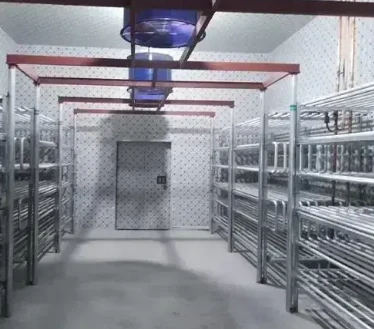
Expertise in the field of high pressure pipe fittings involves an understanding of the engineering principles governing the design and application of these components. This includes knowledge of stress analysis, material science, and the mechanics of fluid dynamics. Manufacturers employ advanced techniques such as computer-aided design (CAD) and finite element analysis (FEA) to ensure that their fittings conform to industry standards and can withstand the challenging conditions they will face.
In terms of authoritativeness, industry standards such as those set by the American Society of Mechanical Engineers (ASME) and the American Petroleum Institute (API) serve as benchmarks for quality and performance. High pressure fittings must often conform to these stringent standards to be deemed suitable for use in critical applications. Manufacturers who consistently adhere to such standards establish themselves as leaders in the field, earning the trust of their clients.
high pressure pipe fittings
Trustworthiness is essential when it comes to high pressure pipe fittings. Clients need assurance that the products they purchase will perform reliably over time. This trust is built through rigorous testing and quality control measures, which often include pressure testing, non-destructive testing (NDT), and inspections. These processes are crucial to verify the integrity and performance of each fitting, ensuring they meet the required specifications.
The market for high pressure pipe fittings is continually evolving with advancements in materials and manufacturing processes. Innovations such as the development of corrosion-resistant alloys and coatings expand the lifespan of these fittings in corrosive environments. Additionally, the introduction of automation and robotics in manufacturing enhances precision and efficiency, reducing production errors and ensuring consistent quality.
As the demand for reliable and durable infrastructure components grows, the importance of high pressure pipe fittings will continue to rise. Industry professionals must stay abreast of the latest technology and compliance standards to ensure the safe and efficient operation of their systems. The selection of the appropriate fittings not only involves technical considerations but also economic factors such as cost efficiency and lifecycle costs.
In summary, high pressure pipe fittings are vital to industries reliant on complex piping systems operating under severe conditions. They embody the principles of experience, expertise, authority, and trustworthiness – characteristics that assure their performance and reliability. By adhering to rigorous engineering standards and implementing advanced manufacturing practices, manufacturers ensure these fittings meet the highest quality and safety benchmarks, thus maintaining their central role in industrial applications worldwide.