Forging flanges play a crucial role in a myriad of industrial applications, seamlessly bridging the gap between traditional manufacturing and modern engineering needs. These essential components not only facilitate the connection and distribution of pipelines and pressure vessels but also ensure the robustness and integrity of engineering projects worldwide.
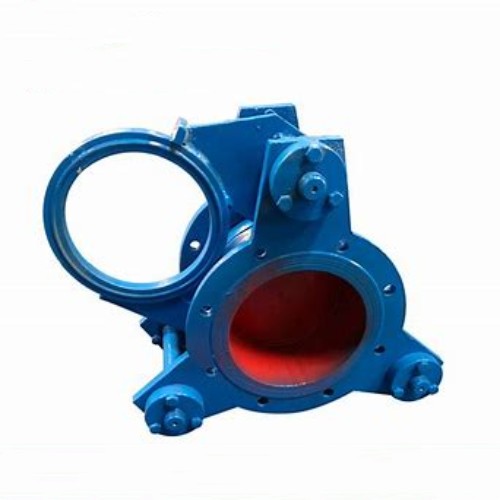
In industries ranging from oil and gas to chemical production, and even in mechanical settings, the demand for high-quality forging flanges remains consistently strong. The inherent properties of forged flanges, such as superior strength, resistance to wear and tear, and enhanced toughness, make them indispensable in environments where reliability and durability are non-negotiable.
Experience tells us that these flanges outperform their cast or machined counterparts significantly. The forging process involves heating a metal bar to a high temperature and then shaping it through compressive forces, which aligns the grain flow according to the shape of the flange. This process results in a final product with improved mechanical properties, such as increased impact resistance and fatigue strength, qualities that cannot be matched by other manufacturing methods. Field engineers and project managers have consistently vouched for the dependability of forging flanges in critical applications, affirming their choice through on-the-ground success stories and repeat usage.
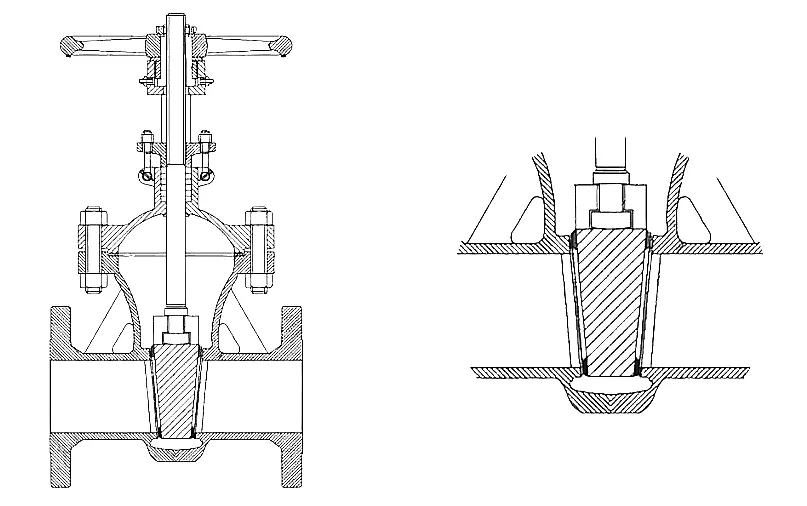
From an expertise standpoint,
understanding the nuances of different flange types is vital. For instance, slip-on flanges, which are slipped over the pipe and welded both inside and outside to provide strength, are often chosen for applications that require it to be easy to adjust in position. On the other hand, weld neck flanges are known for their reliability in high-pressure applications due to their long tapered hub which provides additional reinforcement. Blind flanges, used to terminate the end of a piping system, demonstrate the versatility of forging flanges across multiple use cases.
forging flange
Authoritativeness in the manufacturing and application of forging flanges comes from a history of rigorous adherence to industry standards. Reputable manufacturers subject their products to stringent testing protocols, meeting and often exceeding standards set by organizations such as the American Society of Mechanical Engineers (ASME), the International Organization for Standardization (ISO), and other regulatory bodies. This adherence ensures that the flanges not only meet the necessary technical requirements but also contribute to increased safety and efficiency in their end applications.
Trustworthiness is further cemented by the wealth of research and developmental progress in materials science, informing the selection of raw materials for forging processes. Advancements in alloy compositions and heat treatment techniques have pushed the boundaries of what forging flanges can achieve. Companies that invest in research and development in these areas not only improve their product lines but also enhance their reputation as leaders in the field, providing clients and stakeholders with products they can trust.
For product managers and specifiers, the selection of the right forging flange for specific projects is about more than just matching specifications. It's about leveraging the expertise of metallurgical engineers and industrial designers who understand the complexity and demands of each project. It involves a holistic approach that considers factors such as environmental conditions, expected loads, and potential stress points throughout the component's lifecycle.
As the global industry continues to evolve towards more sustainable and efficient practices, the role of forging flanges will undoubtedly expand. With a focus on innovative design and environmentally-friendly production processes, the future looks promising for these indispensable manufacturing components. The synergy between technological advancement and traditional craftsmanship in forging flanges promises not just continuity, but leadership in the development of reliable solutions for ever-challenging engineering environments.