Welding a flange is a critical task in the domain of pipe fitting and structural engineering, requiring a keen eye for detail and a profound understanding of welding principles. This article delves into the technicalities of the welding process, offering insights from seasoned experts in the field to ensure a comprehensive understanding aimed at enhancing product efficacy and safety.
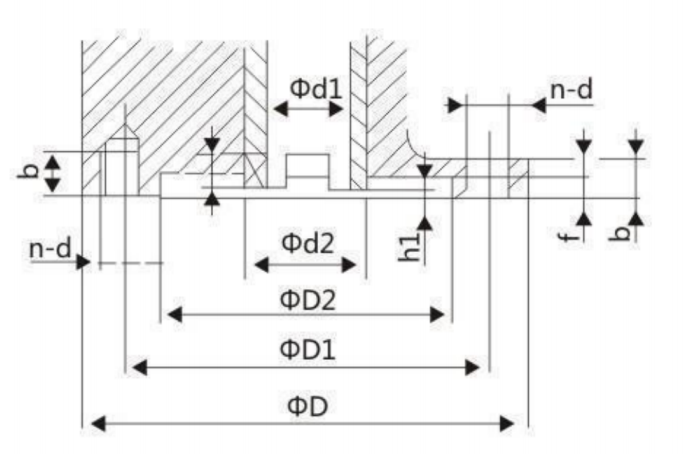
Flanges, essentially protruding rims or edges on pipes, play an instrumental role in connecting different segments or facilitating a superior load-bearing structure. Their significance in the construction, automotive, and manufacturing industries cannot be overstated, demanding precise welding techniques to maintain integrity and functionality.
The process begins with the meticulous preparation of the flange and the pipe it will be welded to. It is imperative to deploy high-quality materials; selecting a flange compatible with the pipe’s material ensures that the resulting weld can withstand operational stresses. Common materials include carbon steel, stainless steel, and alloy steel, each chosen based on specific application needs.
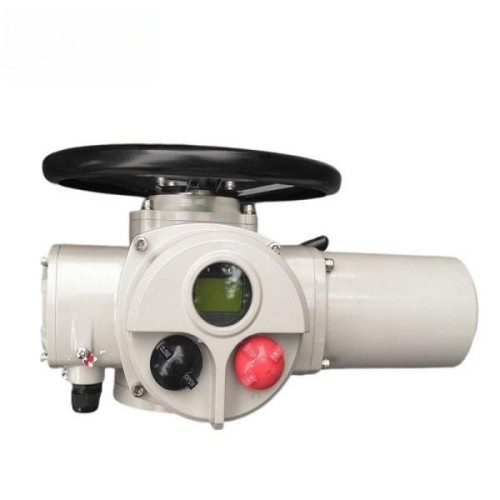
Before welding, thorough cleaning of the joining surfaces is non-negotiable. Contaminants such as rust, oil, or paint must be removed to avoid compromising the weld quality. Utilizing solvents or wire brushing offers an effective technique, creating a pristine surface for the welding process.
A seasoned welder understands the importance of alignment and fit-up. Precision in aligning the flange to the pipe ensures that once welded, the flange will perform its function without inducing stress concentrations or misalignment in the system. Employing pipe clamps or tack welding can aid in maintaining integrity during full welding operations.
When it comes to the actual welding, choice of technique is critical. For high-quality and durable results, many professionals advocate for the TIG (Tungsten Inert Gas) or MIG (Metal Inert Gas) welding methods. TIG welding, with its ability to produce clean and precise welds, is ideal for thinner materials or applications with stringent aesthetic demands. On the other hand, MIG welding offers speed and efficiency, making it suitable for thicker materials or less visually demanding tasks.
welding a flange
Heat management is an aspect that cannot be overlooked. During welding, controlling the heat input is vital to prevent warping or weakening the material. Expert welders often employ techniques such as backstepping or cascading to manage and distribute heat evenly. Pre-heating the metal is another strategy used to alleviate thermal stress, particularly when dealing with thicker flange materials.
Post-weld inspection constitutes a fundamental step in the process, often involving both visual examination and non-destructive testing (NDT) methods. Techniques such as ultrasonic testing or radiography can help uncover any internal flaws or weaknesses that could compromise the structural integrity.
Skill and expertise, reflected in both technique and choice of equipment, underpin successful flange welding. Technological advancements have introduced automated welding systems, which, while efficient, still necessitate human oversight to adjust parameters and ensure standards are met.
Documenting the process is essential for maintaining trust and accountability, especially in regulated industries. Traceability of materials, adherence to welding procedure specifications (WPS), and a detailed report of inspections contribute to an authoritative project completion.
In summary, welding a flange demands a balance of artistry and science; it is the product of years of hands-on experience and the application of advanced welding techniques. By following best practices, industry regulations, and innovative techniques, professionals ensure that welded flanges attain the highest standards of durability and reliability. Each step, from preparation to inspection, underpins the trustworthiness and integrity of the final product, instilling confidence in both contractors and clients alike.