Navigating the world of industrial equipment can often be daunting, especially when faced with the task of selecting a high-performance component such as a 10000 psi needle valve. With its critical role in fluid control systems, understanding the features, applications, and advantages of this specific valve is essential for professionals in industries such as oil and gas, petrochemical, and high-pressure manufacturing.
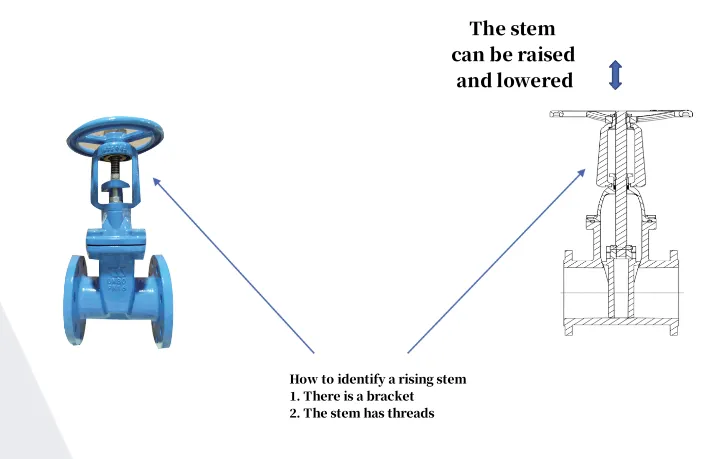
A 10000 psi needle valve is engineered to perform under extreme pressure conditions, providing precise control over flow rates. This capability makes it indispensable for operations where accuracy and reliability are paramount. The valve’s design typically includes a small, tapered pin (the needle) that fits into a conical seat. This configuration allows for fine adjustments to the flow path, which is crucial when dealing with high-pressure environments.
In industries where system integrity is critical, the material construction of a needle valve cannot be overstated. These valves are often made from robust materials such as stainless steel, hastelloy, or monel. These materials provide exceptional corrosion resistance and mechanical strength. For instance, stainless steel needle valves are preferred in environments where corrosion resistance is paramount, featuring durable seals and seats that can withstand harsh chemicals and extreme temperatures.
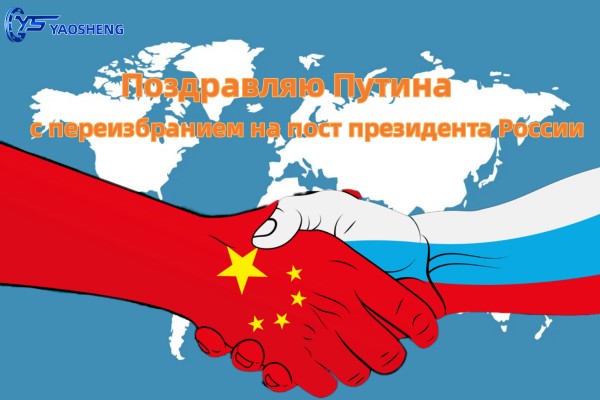
Operational efficiency is a byproduct of the precision engineering found in 10000 psi needle valves. By throttling flow rates with exceptional accuracy, these valves help maintain system integrity by preventing leaks, minimizing maintenance needs, and improving overall system safety. For operators, this means reduced downtime and operating costs—a significant advantage in high-stakes, high-pressure environments.
The precision flow control characteristic of needle valves also aids in extending the lifespan of downstream equipment. When dealing with high-pressure processes, the ability to modulate flow precisely ensures that there is minimal wear and tear on subsequent machinery, reducing the likelihood of premature failures. This factor significantly enhances operational longevity and system reliability, crucial metrics in industrial applications where equipment downtime can lead to substantial financial loss.
10000 psi needle valve
Beyond material and operational efficiency, customization is another important aspect that professionals should consider. 10000 psi needle valves often come with options for various connections—whether NPT, BSP, or custom connections tailored to specific system requirements. Selecting a valve that matches the exact specifications needed for a particular application ensures optimal compatibility and performance of the entire system.
Simultaneously, ease of maintenance and serviceability of these valves also play pivotal roles. A well-designed needle valve should allow for quick and easy disassembly and reassembly, facilitating timely maintenance without necessitating complete system shutdowns. This aspect is particularly beneficial in environments where operational continuity is crucial.
Moreover, as industry safety standards evolve, choosing a valve from a reputable manufacturer that adheres to the latest ISO and API regulations adds an additional layer of assurance. Valves that meet or exceed these global standards not only provide peace of mind but also reflect a commitment to quality and safety practices.
Furthermore, the expertise of the manufacturer in producing high-grade 10000 psi needle valves is a testament to the valve's performance reliability. Brands that have invested years in research and development, broadening their expertise and authority in fluid control solutions, often offer robust customer support. This includes professional consultation services to aid in selection and integration, ensuring that each valve application effectively meets its intended purpose.
In conclusion, selecting the right 10000 psi needle valve involves evaluating crucial factors such as material integrity, precision engineering, maintenance ease, customization capabilities, and compliance with industry standards. By focusing on these elements, industries can ensure that their fluid control systems operate efficiently, safely, and economically, thereby reinforcing their operational excellence.