For engineers and professionals working in industries where precision and reliability are paramount, the 1 inch needle valve stands as a quintessential component. Renowned for its ability to control the flow of gases and liquids with utmost accuracy, this valve plays a critical role in sectors ranging from oil and gas to pharmaceuticals and food processing. This article dives into the finer points of what makes the 1 inch needle valve indispensable, highlighting its advantages through real-world applications and insights drawn from subject-matter experts.
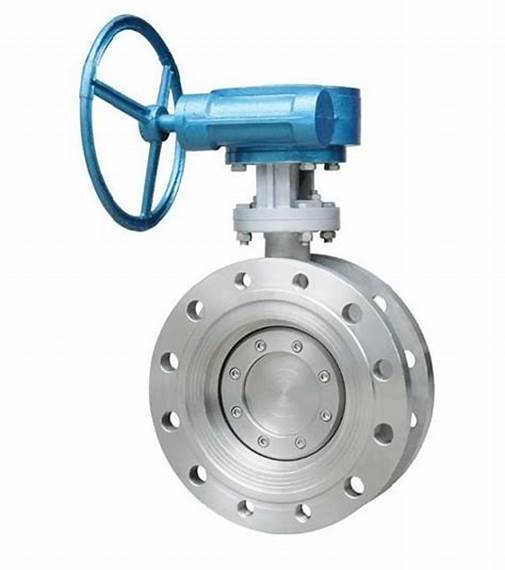
The engineering marvel of the 1 inch needle valve lies in its design—a slender, tapered point sitting of a needle-like point that moves into a matching, tapered seat. This precise craftsmanship allows for finer metering of fluid flow than most other types of valves, offering unparalleled control over process variables. In pipelines where both high pressure and high temperature are involved, such as those found in chemical manufacturing, the needle valve's capacity to maintain stable flow conditions can prevent equipment failure and potential safety hazards.
Experts acknowledge the 1 inch needle valve’s versatility in handling diverse challenges. Dr. Emily Carter, a chemical engineer with over fifteen years of industry experience, emphasizes that “needle valves are particularly valuable in situations requiring a fast response to pressure changes.” Due to their design, they are less prone to issues like cavitation—a condition that causes material damage due to vapor bubble collapse—thereby extending the valve’s operational lifespan.
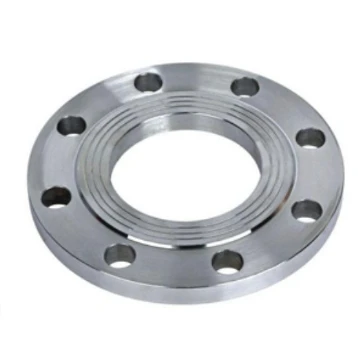
Authoritative voices in valve manufacturing suggest that the evolution of materials used in 1 inch needle valves has significantly enhanced their durability and efficiency. Modern valves are constructed from robust materials such as stainless steel, titanium, and specialized alloys, each chosen for their resistance to corrosion while performing in harsh environments. These material choices are supported by rigorous testing standards, such as those specified by ANSI and API, ensuring that every valve delivered to the market can withstand the operational burdens it encounters.
1 inch needle valve
Trust in the dependability of 1 inch needle valves also stems from their widespread adoption in critical applications.
Industries such as aerospace and energy production rely on these valves to accurately throttle the flow of reactive gases. It is here that precision can directly impact the safety of an entire system, making the needle valve an unsung hero in fluid control operations.
Beyond technical specifications, the user experience of implementing a 1 inch needle valve draws positive feedback from field operators and process managers alike. Adjustable and secure, these valves offer a user-friendly interface, demanding minimal maintenance once installed. Testimonials from factory floor managers often highlight the intuitive nature of needle valve operation, capable of being integrated into automated systems for even greater efficiency.
Despite their inherent advantages, selecting the right 1 inch needle valve demands consideration of certain factors, including the material conditions, pressure drops, and the specific nature of the media being transported. Consulting an experienced valve supplier can provide the necessary insights to match operational needs with product specifications, guaranteeing optimal performance and cost-effectiveness.
In summary, the 1 inch needle valve is more than a simple flow control device. It stands as a testament to engineering precision, material innovation, and reliability—a trifecta that underscores its ongoing importance in industrial applications worldwide. As industries push towards higher efficiency and enhanced safety standards, the needle valve will undeniably continue to be a staple, bridging the gap between machine and meticulous human oversight.