In the complex world of industrial plumbing and fluid control systems, the DN200 gate valve stands out as a fundamental component. This specific valve is renowned for effectively managing substantial fluid flows in large-scale applications. The expansive diameter, denoted by the DN200 (with DN representing Diameter Nominal), highlights its suitability for systems requiring substantial throughput, like municipal water supply networks or industrial fluid transport pipelines.
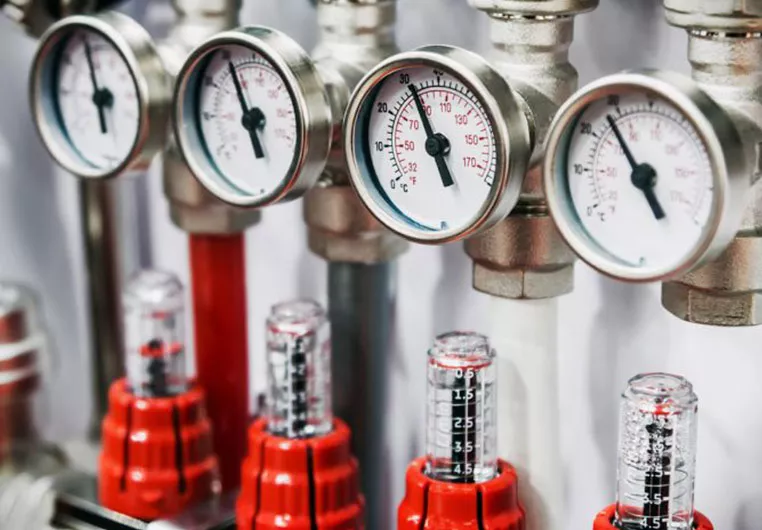
The construction of a DN200 gate valve is a testament to its durability and functionality. Typically designed with robust materials such as stainless steel, cast iron, or ductile iron, these valves demonstrate excellent resistance to corrosion and high temperatures. This resilience ensures a long operational life even under harsh conditions, a crucial feature for minimizing maintenance downtime and costs in large-scale setups.
From an engineering perspective, the precision in the manufacturing of DN200 gate valves ensures minimal fluid resistance when the valve is in the fully open position. The gate mechanism, sliding perpendicularly to the flow direction, provides a straight-path flow and negligible pressure drop, which is essential for systems that demand high-volume transfer with energy efficiency.
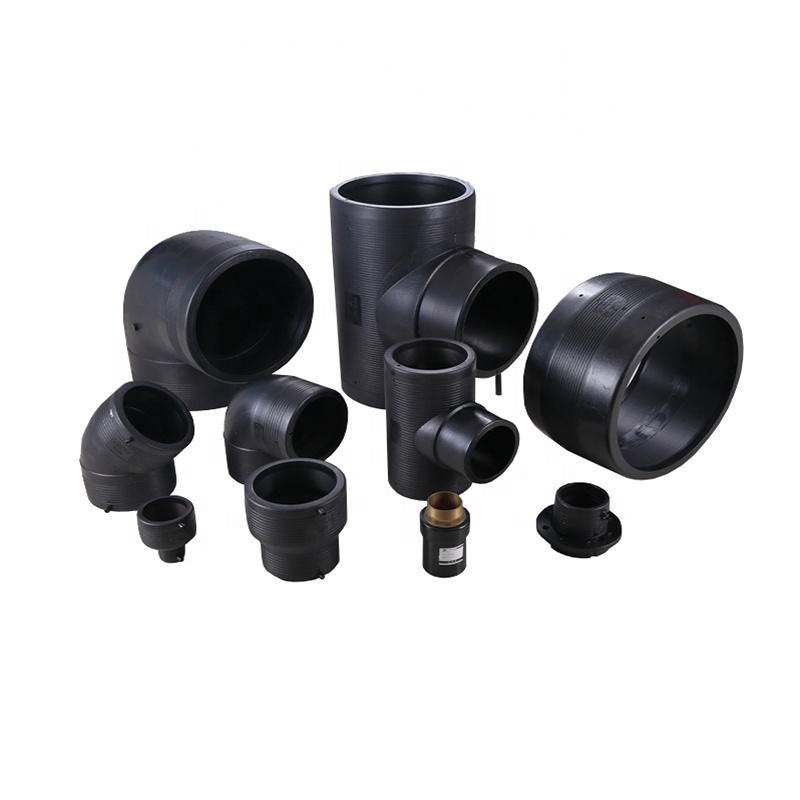
In practical applications, the role of the DN200 gate valve extends beyond simple flow regulation. It is pivotal for operational safety and process control. Industries such as petrochemicals, wastewater treatment, and energy production, where the accuracy and reliability of fluid management are paramount, frequently rely on these valves. Their ability to shut off or redirect vast fluid volumes rapidly can prevent overflows, leaks, or environmental hazards – incidents that could otherwise lead to catastrophic outcomes.
Experts in fluid dynamics often emphasize the importance of the DN200 gate valve's maintenance. Routine inspections ensure that the valve seats and seals are free of debris and damage. This practice helps maintain a tight closure and prevents leaks. The practicality of such maintenance routines is well-documented in industry standards and best practice guidelines, which underscore the valve's role in operational reliability.
dn200 gate valve
When it comes to installation,
the DN200 gate valve requires careful planning. Proper alignment and support to the surrounding pipework are essential to avoid undue stress on the valve body, which could lead to failure in service. Installation manuals and technical sheets from manufacturers play a crucial role in guiding engineers during this process, ensuring that theoretical designs translate successfully into practical applications.
The authority of the DN200 gate valve in industrial sectors is further reinforced by endorsements from regulatory bodies. Compliances with standards such as the American Society of Mechanical Engineers (ASME) and the International Organization for Standardization (ISO) not only affirm its engineering credentials but also establish its trustworthiness in safety-critical industries.
However, the expertise among different models and brands of DN200 gate valves varies. Factors such as ease of operation, automation capabilities, and the quality of materials can significantly impact the valve's performance and longevity. Therefore, selecting the right DN200 gate valve involves a thorough assessment of the specific operational requirements, including factors like maximum operating pressure, fluid characteristics, and environmental conditions.
In summary, the DN200 gate valve is an indispensable tool in industrial fluid management, combining robust construction, precision engineering, and operational reliability. Its design caters to the multifaceted needs of modern industries, emphasizing efficiency, safety, and durability. For stakeholders considering investment in large-scale fluid control systems, the DN200 gate valve offers a combination of innovative technology and proven performance, backed by expert recommendations and industry approvals. Thus, its role in optimizing industrial processes is both critical and irreplaceable, representing a cornerstone of fluid transport technology.