Globe valves, specifically those classified as Class 150, play an instrumental role in various industrial applications. Their design, operation, and materials make them a preferred choice for managing fluid flow. Understanding the intricacies of globe valves, particularly Class 150, can enhance operational efficiency, safety, and system longevity in industrial settings.
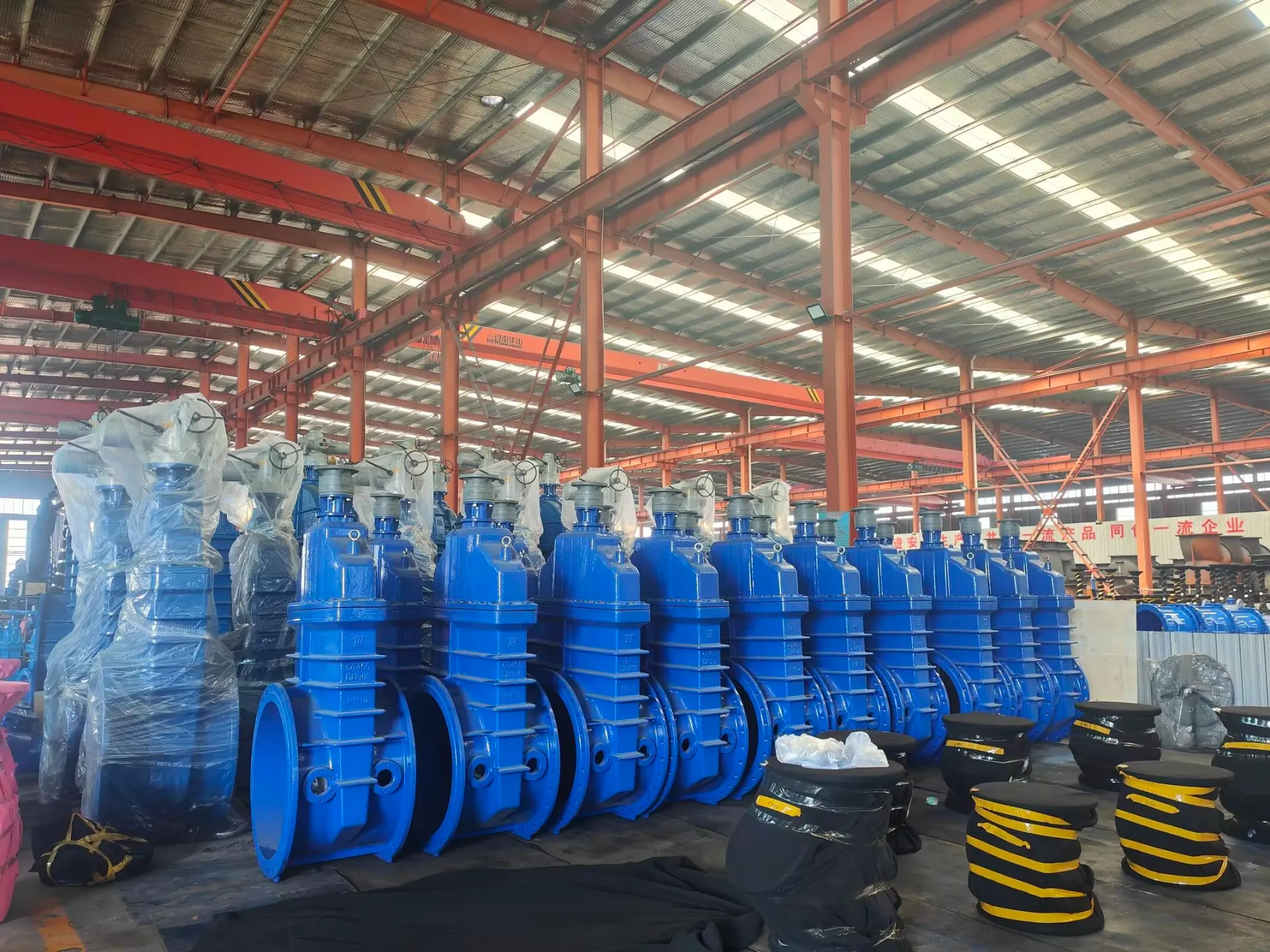
Globe valves are engineered to regulate flow in a pipeline by lifting a disc, or plug, off a valve seat, allowing the fluid to flow through. The design of the globe valve provides an inherent throttling capability, making it ideal for applications where flow regulation is paramount. Class 150 globe valves are designed to handle moderate pressure and temperature levels, typically suited for a wide range of industrial applications, including oil and gas, chemical processing, and water treatment systems.
From an experience perspective, globe valves offer reliability when precision flow control is essential. Industries that have implemented Class 150 globe valves often cite their ease of operation and maintenance, as well as their robust construction. The valve's design allows for straightforward sealing, minimizing leakage risks which can be critical in preventing operational disruptions and ensuring safety.
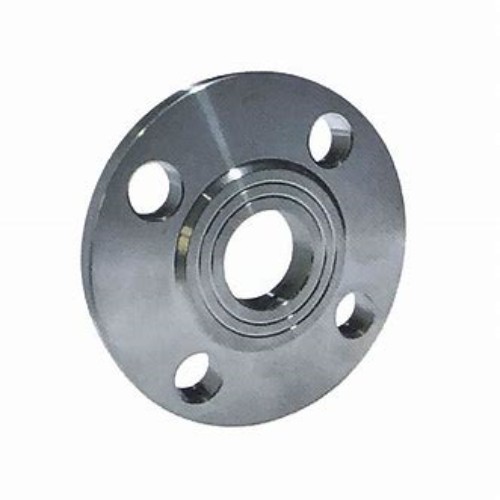
Expertise in selecting the right globe valve involves understanding the specific needs of the application. Class 150 refers to the pressure-temperature rating, which denotes that these valves can handle pressures up to approximately 285 psi at ambient temperatures. This rating guides industry professionals in selecting the appropriate valve to ensure compatibility with system pressures and operational temperatures, thus avoiding over-specification, which can be costly, or under-specification, which can be dangerous.
The construction material of Class 150 globe valves can vary from cast iron and carbon steel to stainless steel, each offering different levels of corrosion resistance, strength, and temperature tolerance. Selecting the right material contributes significantly to the valve’s longevity and performance. For instance, stainless steel is preferred for corrosive environments due to its superior resistance to rust and chemical degradation.
globe valve class 150
When discussing authoritativeness, manufacturers of Class 150 globe valves are often industry leaders who adhere to stringent standards set forth by organizations such as the American National Standards Institute (ANSI) and the American Society of Mechanical Engineers (ASME). These standards ensure the valves meet specific performance criteria, ensuring durability and reliability under prescribed conditions. An authoritative manufacturer not only supplies high-quality valves but also provides comprehensive technical support, facilitating proper installation and maintenance, and thereby extending the service life of the valves.
Trustworthiness in the context of Class 150 globe valves is strengthened by the transparency of manufacturing processes, quality assurance protocols, and documented performance testing. Customers can rely on established brands that offer warranties and post-purchase support, attesting to their commitment to product quality and customer satisfaction. User reviews and third-party certifications can further bolster confidence in the reliability and safety of these valves.
Incorporating Class 150 globe valves into an industrial setup is not solely about managing flow control but also about ensuring system efficiency and safety. The right valve choice can prevent costly system failures, decrease downtime, and improve overall operational performance. Consequently, comprehensive knowledge of the valve's design, materials, manufacturer credentials, and field applications is crucial.
Ultimately, globe valves, particularly in Class 150, represent a cornerstone in the fluid management systems across various industries. Their precision, reliability, and alignment with international standards make them indispensable. As industrial operations continue to demand more precise control and sustainable solutions, the selection and application of the right globe valve become critical components of a successful system.