Forged globe valves are an essential component in various industrial applications, known for their strength, reliability, and ability to regulate fluid flow. With decades of advancement in manufacturing techniques, these valves have become indispensable in industries ranging from oil and gas to power generation. Understanding their intricacies and the benefits they offer can significantly enhance operational efficiency and system longevity.
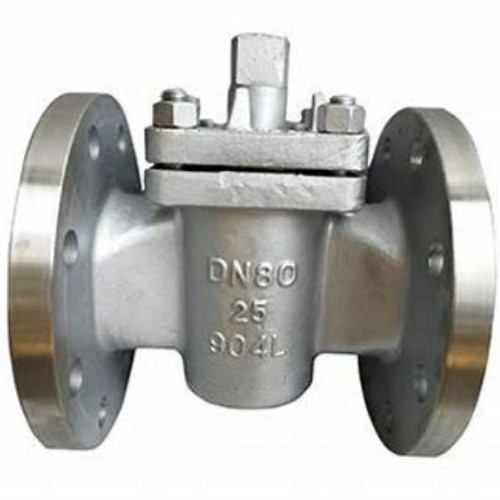
Forged globe valves are primarily used in applications where flow control is crucial. Unlike other types of valves that simply start or stop flow, globe valves provide precise control over flow rates. The secret behind their efficacy lies in their unique design, which allows operators to throttle fluid flow with higher accuracy than other valves. This makes them ideal for situations where fluid volume needs to be adjusted with precision, protecting equipment downstream from the risks of pressure fluctuations.
The forging process itself is a testament to the durability of forged globe valves. Forging involves shaping metal under high pressure and temperature, refining its grain structure and enhancing its mechanical properties. This process yields a more robust valve than those produced by casting. Cast valves, though suitable for many applications, often have inconsistencies in their structure that can lead to weaknesses. On the other hand, the consistent grain flow in forged valves translates into superior strength and reliability, which is particularly crucial in high-pressure and high-temperature environments.
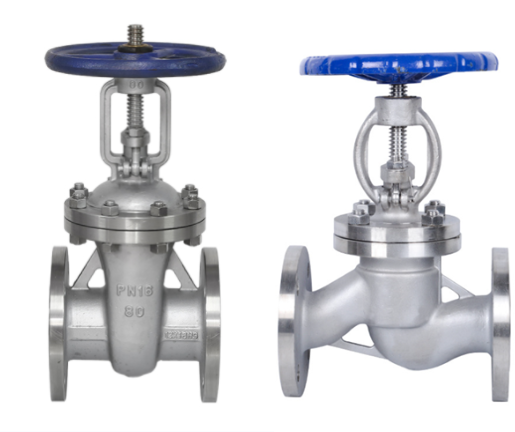
Expertise in material selection further elevates the quality of forged globe valves. Depending on the application, these valves can be manufactured from a variety of metals, including stainless steel, carbon steel, and exotic alloys like Inconel. Each material offers unique advantages; stainless steel provides excellent resistance to corrosion, carbon steel offers exceptional strength at a lower cost, and Inconel can withstand extreme temperatures and conditions. Selecting the right material is essential to maximizing the valve’s lifespan and performance, which is why consulting with experienced professionals during the selection process is advised.
Authoritativeness in the industry comes from not only high-quality manufacturing but also rigorous testing and certifications. Leading manufacturers subject their forged globe valves to extensive pressure testing, ensuring they perform flawlessly under rated conditions. Certifications from organizations like ISO or ASME further assure customers of a valve’s quality, safety, and compliance with international standards. This level of scrutiny and certification underlines the authority that renowned manufacturers command in the marketplace.
forged globe valves
Trustworthiness in a product is built over time through consistent performance. Reliability of forged globe valves in demanding applications, such as in refineries or chemical plants, fosters trust with operators who rely on these components to maintain safety and efficiency. The reputation of a manufacturer, bolstered by decades of consistent product excellence and customer satisfaction, is instrumental in establishing trust. Service and technical support, available from knowledgeable professionals, further enhance this trust, ensuring that any issue can be addressed promptly, minimizing downtime and operational disruptions.
Industrial case studies highlight the transformative impact of switching from less reliable valves to forged globe valves. Notable improvements in plant efficiency, reduced maintenance costs, and enhanced safety metrics are common outcomes. For example, a large-scale petrochemical facility that replaced its cast valves with forged globe valves reported a significant reduction in equipment failures and maintenance shutdowns, leading to a measurable increase in productivity and cost savings.
Experience from field applications offers valuable insights into best practices for installation and maintenance of forged globe valves. Proper installation is critical; ensuring correct alignment and support can prevent issues such as stem wear and leaks over time. Regular maintenance, including routine inspections and timely servicing, further extends the life of the valve. Many industry veterans advocate for the establishment of a preventive maintenance schedule to address minor issues before they escalate into major problems.
In conclusion, forged globe valves stand out due to their unparalleled strength, dependability, and precision in flow control. These attributes, backed by expert material selection, authoritative certification standards, and the real-world trust they garner, make them a preferred choice across many sectors. By investing in forged globe valves, businesses not only enhance their operational efficiency but also secure peace of mind with a product designed to perform reliably under pressure.