In the dynamic arena of construction and engineering, the selection and application of pipe valve fittings are crucial, not only for the functionality and safety of systems but also for their efficiency and longevity. As an expert in the field with over two decades in the industry, I have firsthand experience with the immense value these components bring. This article delves deep into the nuances of pipe valve fittings, offering insights from both an expert’s standpoint and practical experience, while also building on their authoritative and trustworthy applications.
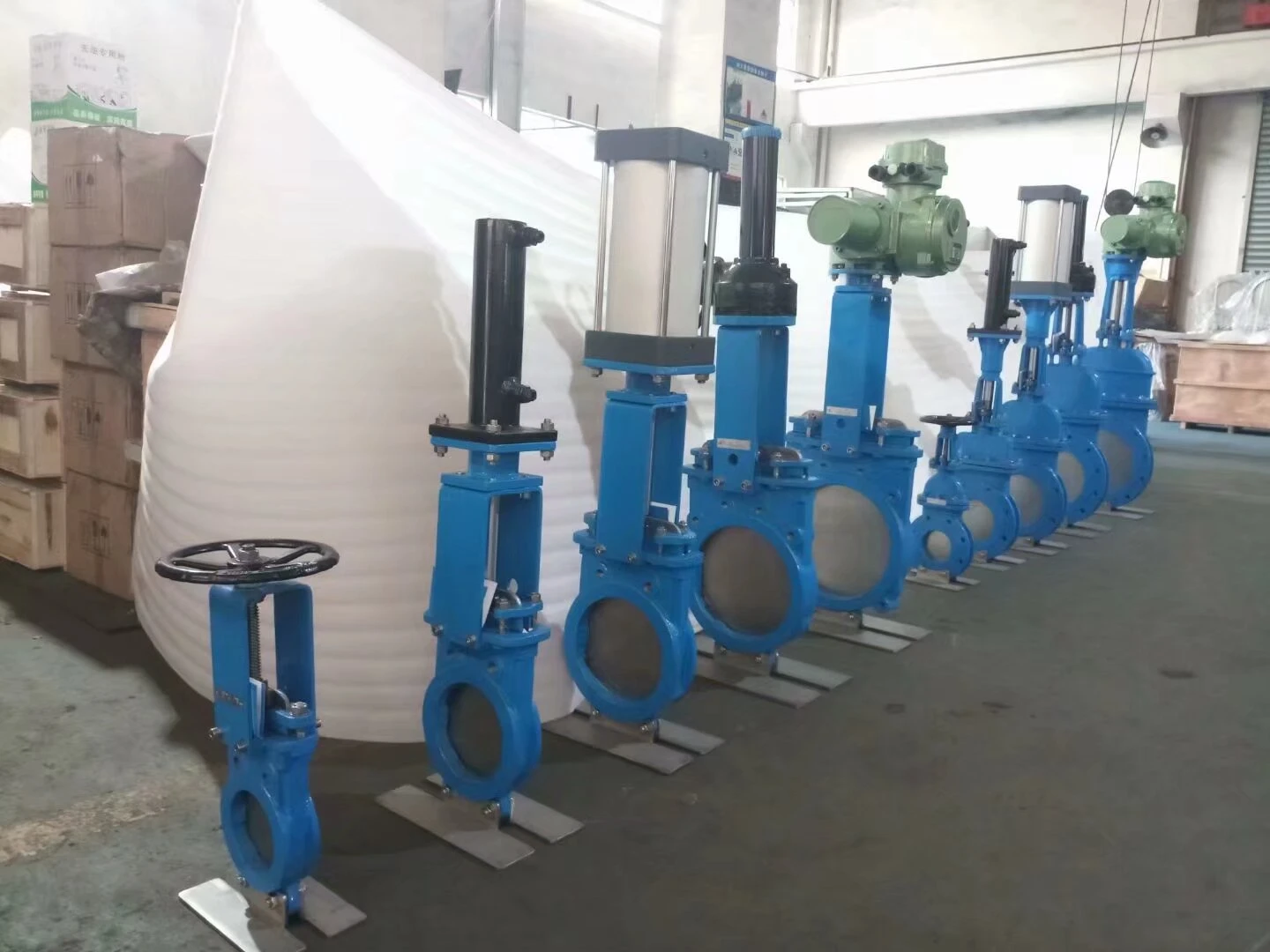
Pipe valve fittings serve as pivotal components ensuring the seamless flow of liquids and gases in a multitude of systems, ranging from residential plumbing to complex industrial processes. Their utility extends beyond mere connectivity; they are integral in pressure regulation, flow control, and maintaining safety protocols.
1. Diverse Applications and Types
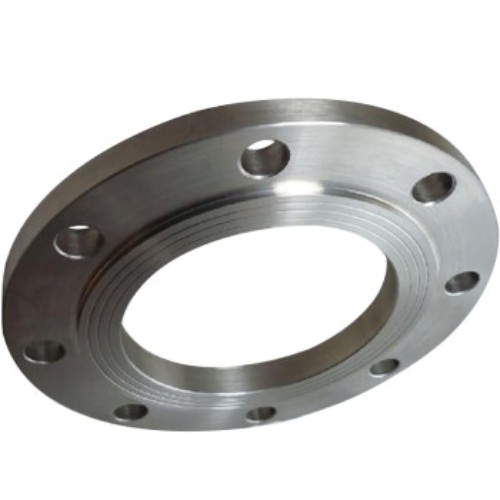
One of the key considerations is comprehending the wide array of types and applications that pipe valve fittings come in. Gate valves, ball valves, butterfly valves, and check valves each serve unique functions. Gate valves are typically used where a linear flow of fluid is essential and should be controlled, while ball valves offer robust shut-off capabilities. Butterfly valves, known for their lightweight construction, provide easy flow regulation in large systems, whereas check valves prevent backflow, safeguarding the integrity of pipelines.
Choosing the right type depends on several factors, including the fluid type, pressure requirements, and the environment where they will be deployed. For instance, chemical plants may require corrosion-resistant materials such as stainless steel or brass, whereas aluminum might suffice in less aggressive environments.
2.
Material Considerations
The material of the valve fitting is instrumental in determining its efficacy and longevity. Common materials include brass, stainless steel, PVC, and carbon steel. Each material has its distinct advantages brass is favored for its durability and resistance to corrosion; stainless steel is prized for its strength and ability to withstand high temperatures; PVC is lightweight and cost-effective for less demanding applications; and carbon steel is known for its robustness.
From an experienced standpoint, the choice of material should align with the specific demands of the environment. Environments subject to wide temperature fluctuations or corrosive substances will degrade incompatible materials swiftly, leading to potential system failures.
3. Installation and Maintenance Expertise
pipe valve fittings
Proper installation and routine maintenance significantly influence the performance and lifespan of pipe valve fittings. Meticulous attention must be paid during installation to ensure that all components are aligned correctly and securely fastened. This prevents leaks and enhances the efficiency of the flow system. Furthermore, regular maintenance, including inspections and cleaning, is vital to prevent sediment build-up that could obstruct flow or damage the system.
Have you ever encountered a sudden drop in system pressure or unexpected leaks? These are often symptoms indicating that maintenance routines need reevaluation or that the wrong fitting type was initially chosen. Adopting a proactive approach can prevent costly downtimes and extend the operational lifespan of the systems.
4. Advanced Technology and Innovations
The field of pipe valve fittings is not stagnant; it is continually being enhanced by technological innovations. Smart valve technology, for instance, integrates IoT solutions allowing for real-time monitoring and remote operation. These advancements not only provide convenience but also bring a new level of safety and operational efficiency.
The emergence of automated systems has brought about a revolution in industrial applications. With these systems, valves can adjust dynamically based on real-time data, optimizing flow and pressure without manual intervention. This approach minimizes human error and enhances the overall safety of operations.
5. Safety and Compliance
Lastly, ensuring that pipe valve fittings conform to industry standards and regulations is non-negotiable. Safety and compliance certifications such as ANSI, ASME, and ISO should be the benchmark during the selection process. These certifications are a testament to the product’s reliability and alignment with global safety standards.
In conclusion, understanding the diverse types, material benefits, precise installation methods, and leveraging technological advancements in pipe valve fittings can significantly influence the operational success of any project. By prioritizing safety, compliance, and adopting innovation, organizations mitigate risks and ensure the unwavering trust of stakeholders and clients alike.