Cryogenic butterfly valves are essential components in industries that handle low-temperature processes, often as cold as -196°C, such as liquefied natural gas (LNG), cryogenic gases, and other applications requiring robust and reliable performance under extreme conditions. With advancements in technology and increasing global demand for cryogenic systems, understanding both their design and operational expertise has become paramount.
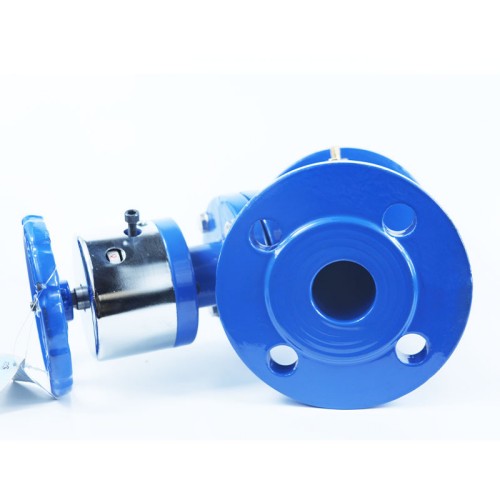
These valves are characterized by their unique ability to regulate flow efficiently in cryogenic conditions. One notable feature is their lightweight build and compact design, which not only saves space but also ensures easy integration into existing piping systems. This adaptability is crucial for industries striving to enhance their operational efficiency without significant overhauls.
Experience in the field indicates that these valves are remarkably reliable when constructed from materials like stainless steel, Inconel, and bronze, which offer superb resistance to low temperatures and the stresses of thermal cycling. Expertise in material science informs the choice of these materials, ensuring the valves maintain integrity and performance without embrittlement or leakage over time.
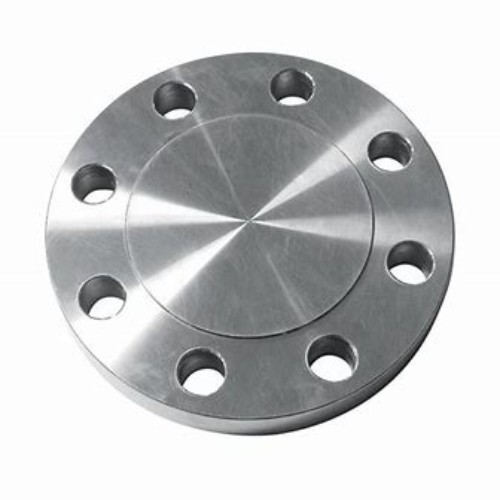
Professionals working with cryogenic systems attest to the importance of a meticulous manufacturing process. The precision required during the valve production is non-negotiable, as even a minor flaw can lead to costly leaks or failures. A high degree of craftsmanship is evident in the rigorous testing procedures these valves undergo, often involving helium leak detection and cryogenic immersion tests to validate their performance under operating conditions.
Furthermore, operators rely on these valves for their ease of maintenance and long service intervals. The design focuses on minimal friction and wear, attributed to their innovative seal systems that are crafted for high cycle durability. This minimizes the downtime and operational costs associated with maintenance, reinforcing their superb reliability in continuous processes.
cryogenic butterfly valves
For industries seeking authority in their operations, partnering with reputable manufacturers of cryogenic butterfly valves is crucial. Market leaders like Emerson, Flowserve, and Velan dominate due to their consistent delivery of quality products and comprehensive support services. They provide extensive documentation, training, and troubleshooting to ensure smooth installation and operation.
Trustworthiness in cryogenic applications is achieved through adherence to international standards such as ISO, API, and ASME. These certifications validate that valves are not only designed meticulously but also tested against the most stringent international benchmarks. This assurance is crucial for industries considering the high stakes involved in cryogenic operations, where safety is paramount.
Moreover, real-world case studies shed light on the successes of cryogenic butterfly valves in critical applications. LNG plants, for example, report improved process efficiency and safety due to the enhanced flow control these valves provide. Similarly, in aerospace technology, they play a pivotal role in the safe handling of rocket fuels, showcasing their versatility and reliability across different sectors.
In conclusion, cryogenic butterfly valves are indispensable for industries that operate in extreme low-temperature environments. Their efficient flow regulation, durable materials, and precise engineering contribute to their status as trustworthy and authoritative components in critical industrial applications. Embracing continuous innovations and adhering to rigorous standards will ensure these valves remain at the forefront of cryogenic technology, supporting industries in pushing the boundaries of what's possible in cryogenic processing.