The landscape of industrial fluid management is vast, yet one component stands out due to its vital function and versatility the check valve. Specifically, six variants of check valves serve various applications across multiple industries, each presenting unique features, advantages, and efficiencies. Understanding these can significantly enhance operational efficiency and reliability.
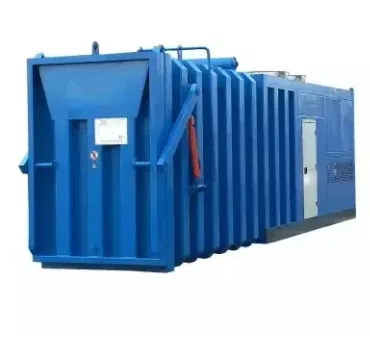
The first in this lineup is the swing check valve, renowned for its simple but effective design. Swing check valves utilize a disc that swings on a hinge or shaft to block reverse flow. They are widely used in water and wastewater systems, where minimizing water hammer and pressure drop is crucial. Their ability to handle large volumes of fluid with minimal pressure loss makes them indispensable in ensuring uninterrupted flow in municipal water systems and industrial plants. Users often praise their easy maintenance and long service life, crucial factors in systems where downtime equates to high costs.
Next, we have the lift check valve, utilized primarily in piping systems where frequent flow reversal is expected. Lift check valves operate using a gravity-assisted mechanism, where the disc rises with the flow and settles back against the seat upon flow reversal. These valves are highly valued in boiler feed lines and other high-pressure applications, offering a safeguard against the detrimental effects of backflow. Their robust construction suits environments where reliability and durability are paramount, protecting pumps and compressors from reverse flow damage.
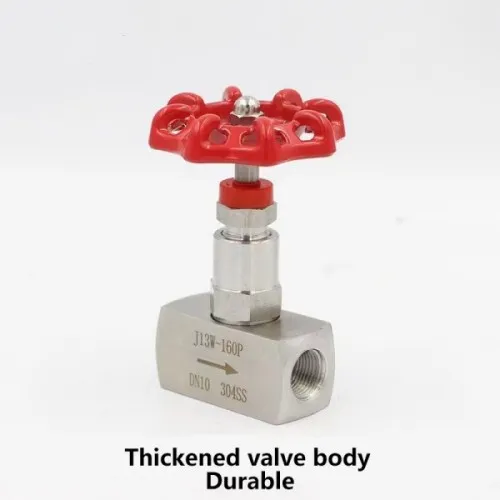
The wafer check valve represents a more compact solution, appreciated for its lightweight and space-saving design. Its slim profile does not compromise on performance, making it ideal for systems where space is a constraint. Wafer check valves are especially popular in HVAC systems, where their low-pressure drop and ease of installation make them a convenient and cost-effective choice. They are frequently used in applications where reducing weight and size is critical without sacrificing the reliability of fluid control.
In systems requiring non-slam functionality,
the silent check valve excels. Often found in high-rise buildings and chilled water loops, these valves mitigate water hammer with precision. They feature a spring-assisted disc, which closes just before flow reversal, thus preventing the sudden stoppage that causes water hammer. Silent check valves are less disruptive, protecting pipeline integrity and reducing maintenance costs associated with equipment wear and tear due to hydraulic shock.
6 check valves
Ball check valves, meanwhile, offer a robust and straightforward solution for handling viscous fluids or slurries. By using a ball that rotates and reseats itself, these valves minimize wearing, making them ideal for wastewater treatment plants and other industrial applications involving particulates. Their ability to handle high viscosity materials ensures continuous and reliable performance, important in applications where media properties are challenging, and process continuity is crucial.
Lastly, diaphragm check valves provide an exceptional option for applications where hygiene and sterility are top priorities. These valves employ a flexible diaphragm, which responds swiftly to changes in flow direction. This design is particularly beneficial in pharmaceutical and food processing industries, where contamination control is vital. The diaphragm effectively isolates the flow medium from the operational mechanism, maintaining sterility and enhancing process safety.
Choosing the correct type of check valve for your specific application hinges on understanding the unique demands of your system. Factors such as pressure ratings, media characteristics, flowrate, and installation constraints play a significant role in determining the best fit. Professionals in the field emphasize the importance of aligning the valve type and material with the specific operational criteria and regulatory requirements.
Expertise in selecting and installing check valves can mean the difference between seamless operation and costly disruptions. Industry authorities recommend regular performance assessments and maintenance checks to ensure these components function optimally. Trust established suppliers who offer detailed specifications, comprehensive service support, and robust warranties to uphold system performance and lifecycle cost-effectiveness.
In embracing these six check valve variants, industries fortify their commitment to efficient, reliable, and safe fluid management. The right check valve not only ensures directional flow but also safeguards infrastructure, optimizing operational longevity and performance. As fluid control technology advances, remaining informed and adaptive to innovations in valve design and functionality becomes imperative for practitioners aiming to maintain industry-best practices and standards.