Stop check valves play a pivotal role in various industrial and commercial applications, providing a reliable solution for controlling the flow of fluids. As an advanced type of valve, these components incorporate unique design features that offer several benefits over traditional check valves. Whether you are a seasoned engineer or a procurement specialist seeking the best equipment for your system, understanding the nuances of stop check valves will enhance operational efficiency and safety.
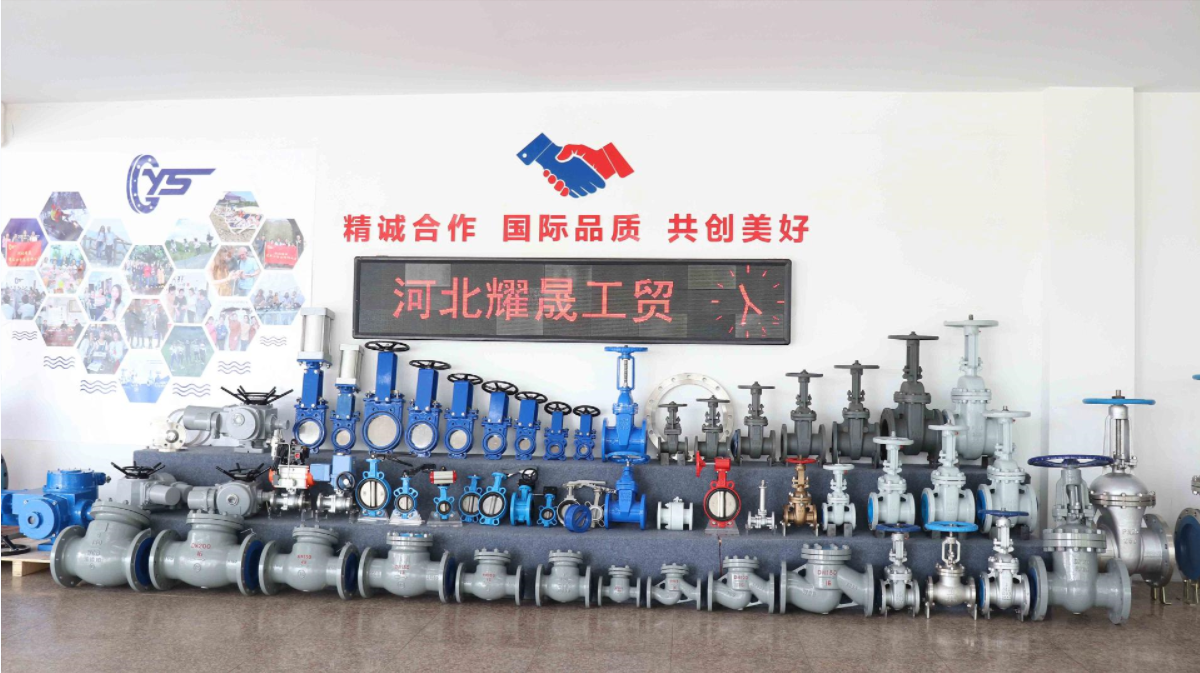
A stop check valve combines the functionality of a check valve with the ability to manually prevent flow regardless of pressure changes. This dual capability is critical in applications where preventing reverse flow is vital, such as in steam systems, boiler feed lines, or any fluid system requiring precise flow control. Unlike conventional check valves that rely solely on the differential pressure to close, stop check valves grant operators control to manually close the valve, functioning similarly to a globe valve when necessary.
Experience in the field reveals that the robustness and reliability of stop check valves significantly reduce downtime and maintenance costs. In industries such as power generation, where systems operate under high temperatures and pressures, these valves prevent backflow that could otherwise lead to equipment damage or catastrophic failure.
Stop check valves thus serve as an essential safety device, protecting both workers and machinery.
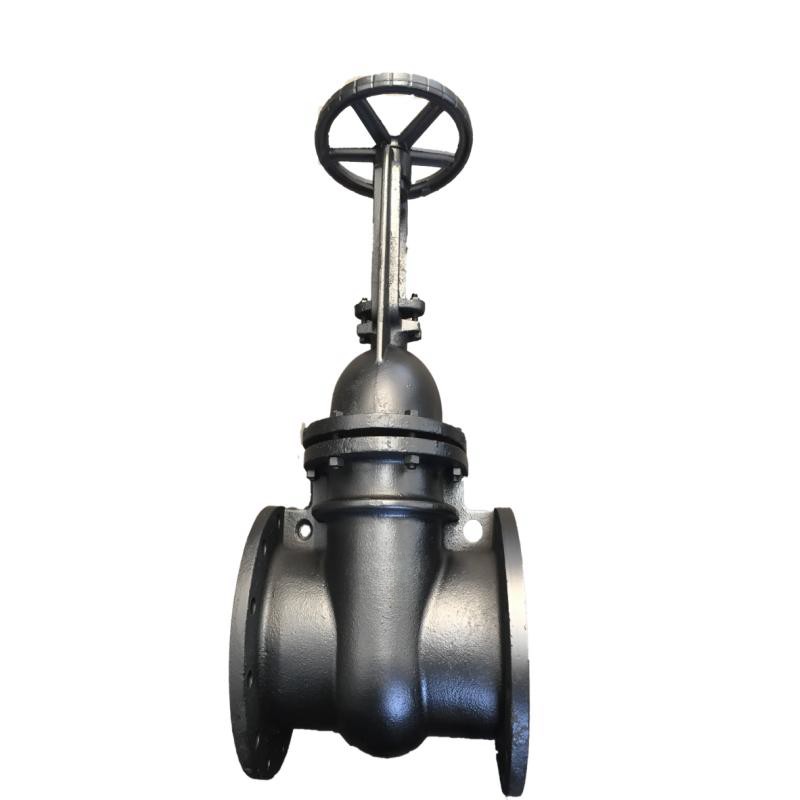
The design of stop check valves often includes a globe valve body, an internal disk that functions as a check mechanism, and a handwheel or actuator for manual operation. This design not only enhances durability but also simplifies maintenance procedures. The ease of replacing valve seats and discs without removing the valve from the pipeline underscores the design's consideration for long-term operation and maintenance efficiency.
stop check valve
As a product expert, it is essential to recognize the various materials and construction options available for stop check valves. These valves are often made from stainless steel, carbon steel, or other alloys, chosen based on the specific requirements of the application, such as resistance to corrosion, high temperatures, or particular chemical interactions. Selecting the right material can extend the life of the valve and ensure optimal performance under challenging conditions.
From an authoritative perspective, industry standards and certifications provide a benchmark for quality and performance. When selecting a stop check valve, look for products that meet or exceed established industry standards, such as those set by the American National Standards Institute (ANSI) or the American Petroleum Institute (API). These certifications not only assure reliability but also aid in regulatory compliance, which could be crucial for certain industries.
Trust in stop check valve functionality is not only built on material and design but also on ongoing innovation and field-testing. Leading manufacturers invest in research and development to produce valves that can withstand increasingly demanding applications. Their commitment to quality is validated through rigorous testing processes, ensuring that each valve performs as expected when integrated into a system.
In conclusion, stop check valves offer unparalleled control and reliability in managing fluid flow, making them indispensable in a range of industrial applications. By understanding their functionality, design specifications, and material considerations, and by choosing valves compliant with industry standards, buyers and engineers can optimize their systems for safety and efficiency. The comprehensive understanding of stop check valves—rooted in experience, expertise, authority, and trustworthiness—empowers industry professionals to make informed decisions that drive success.