In the realm of plumbing and piping systems, the choice of components can dramatically affect the efficiency and durability of the entire assembly. One critical component that often goes underappreciated yet plays a pivotal role is the pipe union fitting. Understanding the nuances of pipe union fittings, their applications, and optimal usage not only enhances the longevity of your systems but also maximizes cost-effectiveness, making them indispensable in industrial, commercial, and residential plumbing solutions.
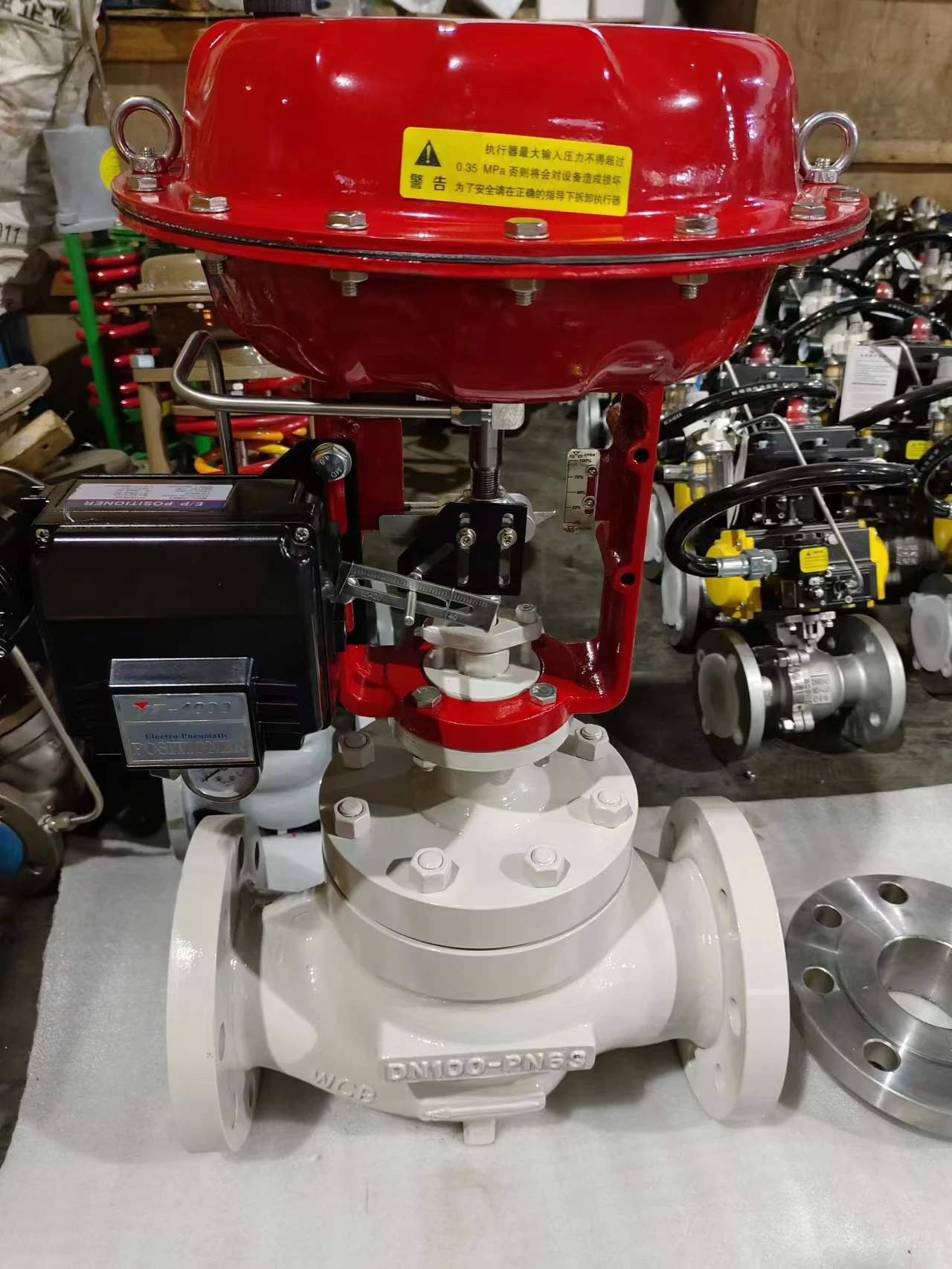
Pipe union fittings stand out for their unique capability to join two sections of a piping system without requiring complex tools or specialized skills. Unlike permanent fittings, which require cutting or significant alterations to remove or replace, union fittings allow for easy dismantling and maintenance. This feature becomes especially critical in systems that require frequent inspections, replacements, or cleaning, ensuring that downtime is minimized and operational efficiency is upheld.
The design of pipe union fittings typically involves three parts a nut, a female end, and a male end. The nut tightens around both the male and female ends to lock the pipes into place. This straightforward mechanism not only facilitates easy installation but also ensures a secure connection that resists leaks and withstands pressure fluctuations, thereby bolstering the system's integrity and reliability.
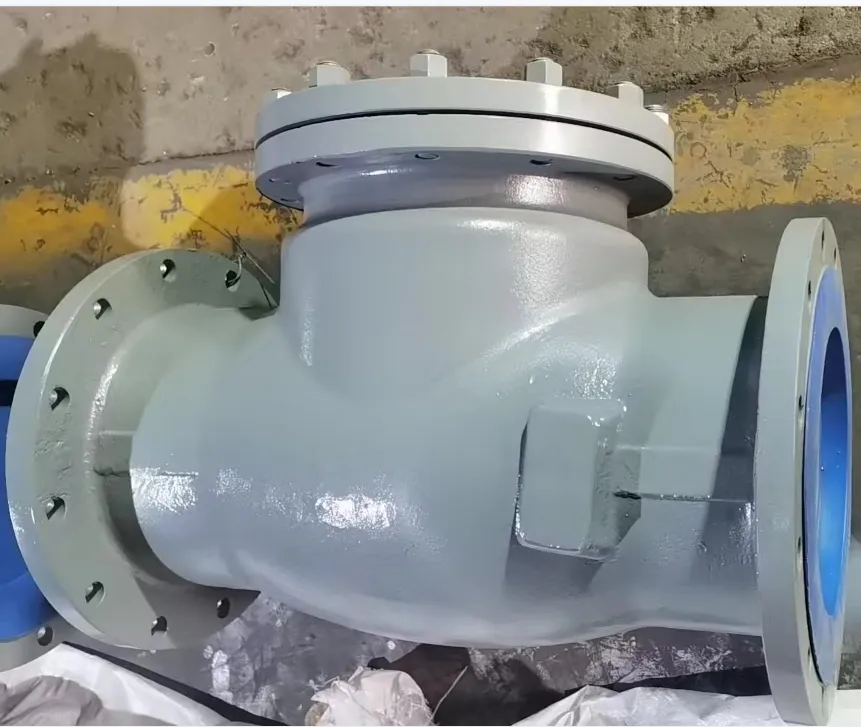
Selecting the appropriate material for a pipe union fitting pivots on the system's specific requirements, including the nature of the fluid transported and the environmental conditions. Common materials include galvanized iron, brass, stainless steel, and plastic, each catering to different needs. Stainless steel fittings, for instance, are ideal for high-pressure systems or those transporting corrosive fluids, given their robustness and resistance to corrosion. In contrast, brass fittings are often preferred for their durability and lower cost in applications involving hot water or less abrasive fluids.
From an industry expertise standpoint, an optimal strategy when integrating pipe union fittings into a system is to consider not only the current demands but also future modifications. Systems are often subject to change, whether due to upgrades, expansion, or changing regulatory requirements. Therefore, investing in quality fittings that offer flexibility and ease of modification can lead to significant savings down the line. Furthermore, compliance with industry standards and certifications is non-negotiable, as these guarantee both safety and quality.
pipe union fitting
When it comes to installation, best practices advocate for a methodical approach. Initial alignment and cleanliness of the connecting surfaces are critical, preventing unnecessary wear or contamination. Hand-tightening should precede final tightening with tools to avoid over-torquing, which can damage the threads or compromise the seal. Additionally, incorporating a regular inspection schedule will ensure that the fittings maintain their integrity over time, addressing any issues before they escalate into costly repairs.
For businesses and contractors, understanding the intricacies of pipe union fittings not only promotes efficiency but also builds client trust. Demonstrating a commitment to quality and reliability by selecting and installing the right fittings enhances your reputation as a knowledgeable provider. Clients are increasingly informed and value transparency and expertise, making it imperative that every choice reflects an understanding of both technological advancements and best practices.
Moreover, maintaining a robust relationship with suppliers can augment this expertise.
Suppliers often have the most up-to-date information on innovations and trends within the industry. Engaging with them can yield insights into new products that may offer superior performance, thereby giving your business a competitive edge and fostering a narrative of authority and trustworthiness in your service delivery.
In summary, pipe union fittings may appear as minor components within a broader system, but their impact on operational efficacy and maintenance costs is profound. Through informed selection, meticulous installation, and consistent maintenance, these fittings can significantly enhance system performance. Elevating one's expertise in these components not only improves system reliability but also fortifies a company’s standing as a leader in quality and innovation, ensuring long-term client satisfaction and business success.